The Value of Front-Loading and Design Rule Checks
To minimize costly rework in downstream processes, designers often invest significant effort into Design Rule Checks (DRCs)—a practice known as front-loading. One vital category of these checks ensures that the designed geometry is suitable for subsequent production steps.
This approach is a key component of what’s broadly known as Design for Excellence (DFX).
What Is DFX, and Why Does It Matter?
DFX is a proactive design philosophy that incorporates downstream knowledge—from manufacturing to inspection—to ensure the final product meets performance expectations, complies with quality standards, and is produced cost-effectively.
The fundamental principle is simple: addressing design issues early in the development cycle is drastically more cost-effective than resolving them in later stages. Detecting problems in production or post-release can result in significant delays, rework, or even multi-million-dollar losses.
In fact, industry studies show that over 80% of manufacturing-related issues originate in the design phase.
Despite its clear benefits, putting DFX into practice remains challenging for many organizations.
Real-World Challenges with DFX Adoption
While Design for Manufacturability (DFM) is the most widely implemented DFX discipline, companies are increasingly applying DFX to other domains, such as:
-
DFA: Design for Assemblability
-
DFC: Design for Cost
-
DFS: Design for Safety
-
DFE: Design for Environment
-
DFT: Design for Testability
However, one major obstacle is the lack of standardization within the industry or within the company. DFX criteria are often tailored to each organization’s unique manufacturing strategy and production capabilities. As a result, companies must develop their own DFX checklists and processes.
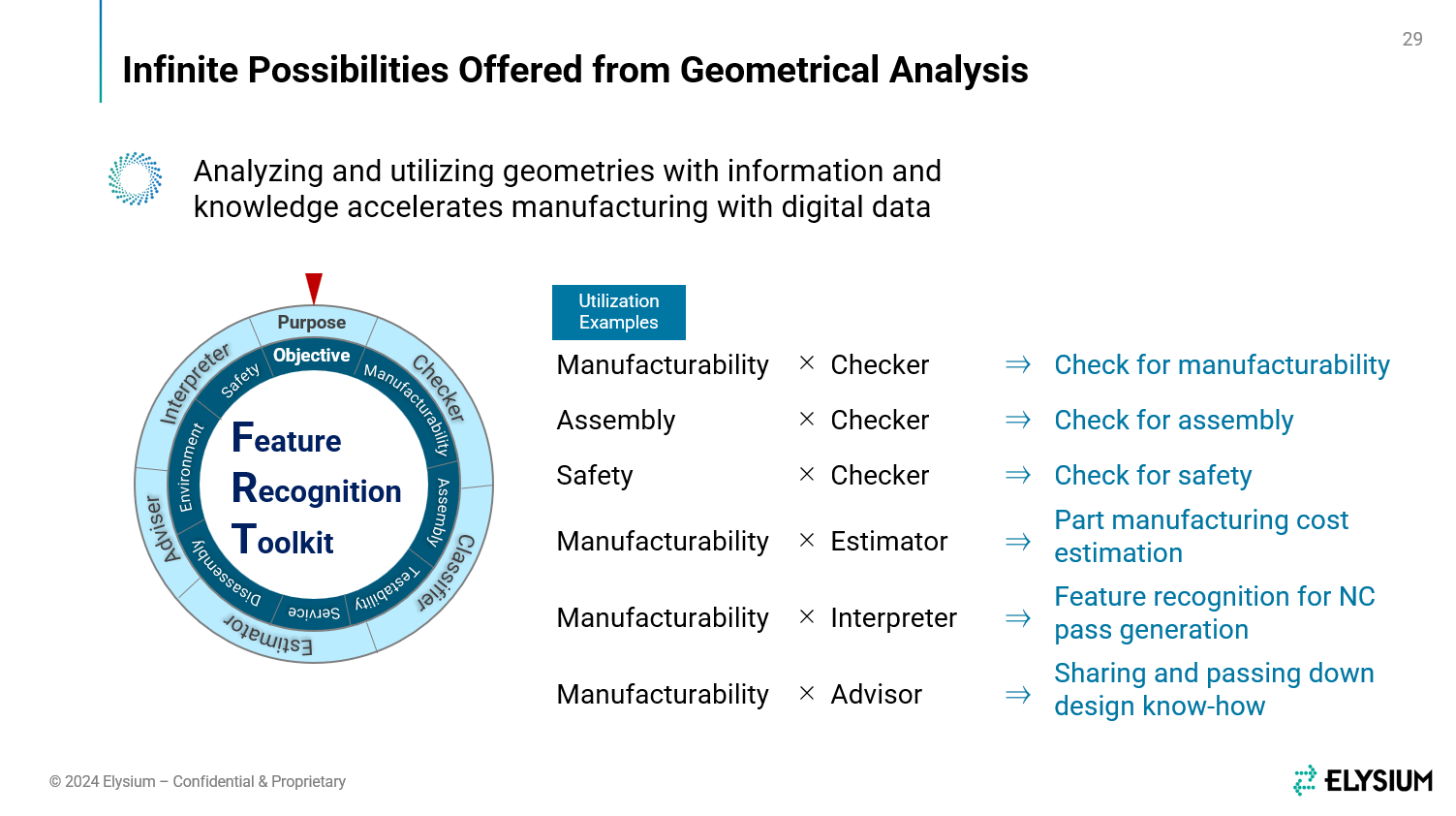
Elysium’s Approach to DFX
Traditional CAD checks rely on engineers to manually inspect and measure geometry—a time-consuming and inconsistent process dependent on individual experience.
Elysium addresses these challenges with the DFX Analyzer, a solution within 3DxSUITE that provides an automated, CAD-based solution for DFX checks.
Starting from a 3D CAD model, the DFX Analyzer can detect, analyze, and evaluate geometry according to DFX principles. Results are presented in an easy-to-navigate list, and detected issues can be visually reviewed in a 3D viewer. Reports can also be exported to Excel for further documentation or collaboration.
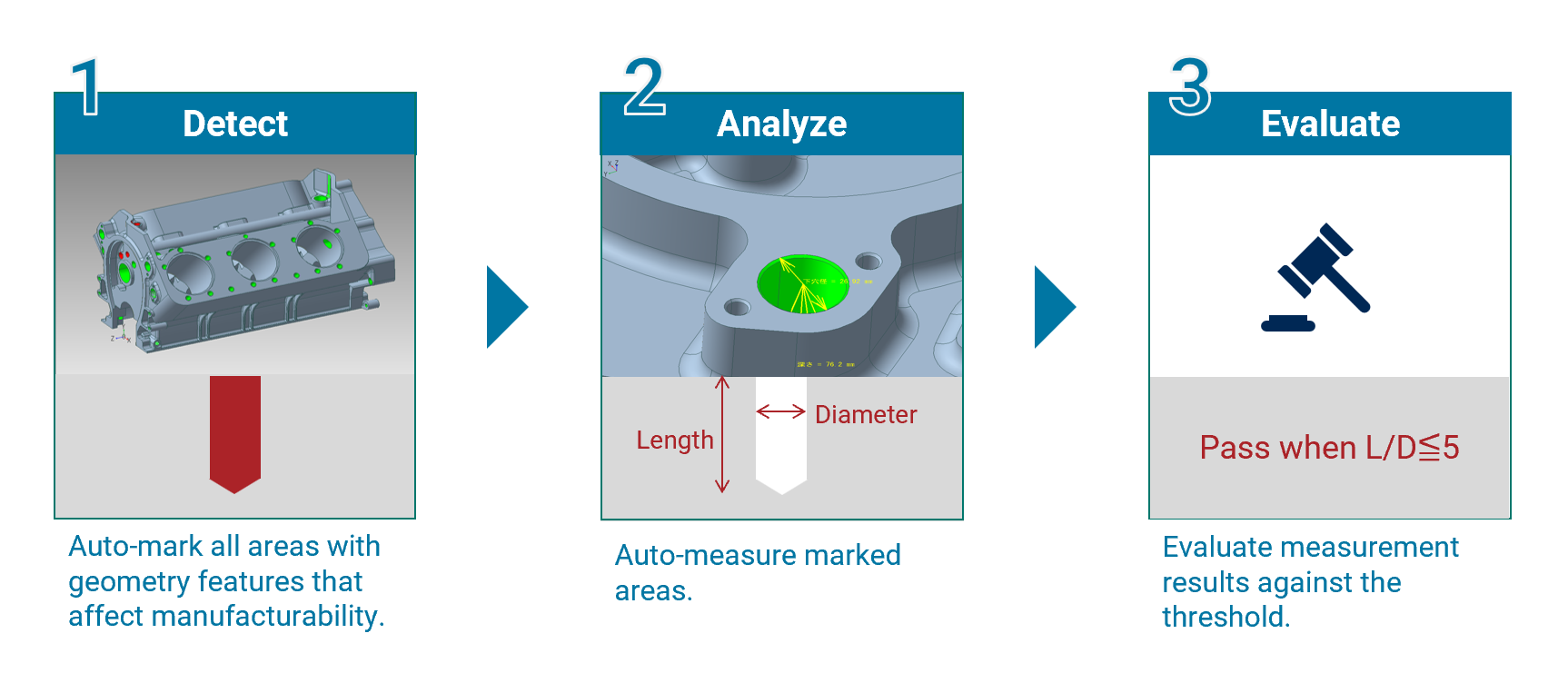
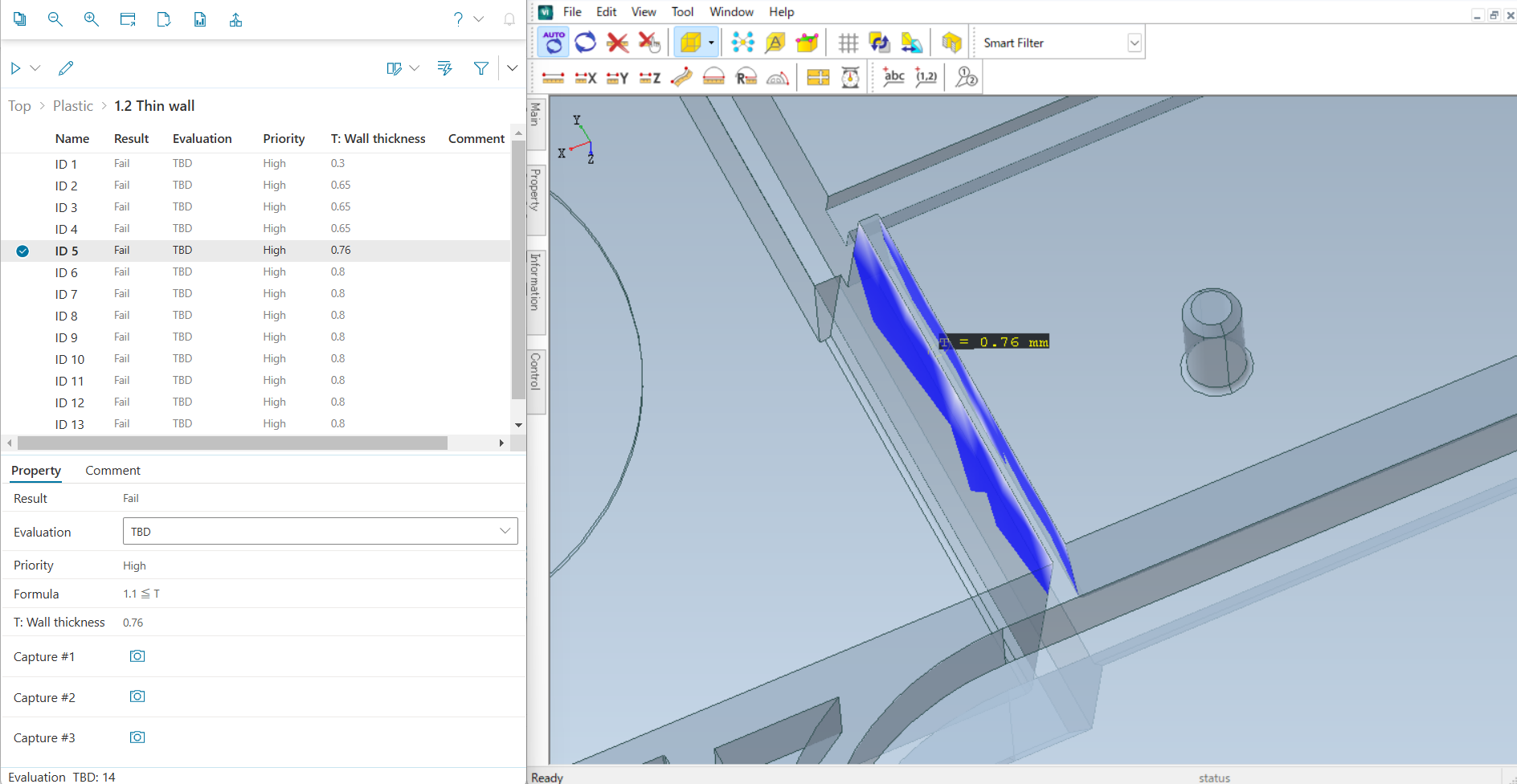
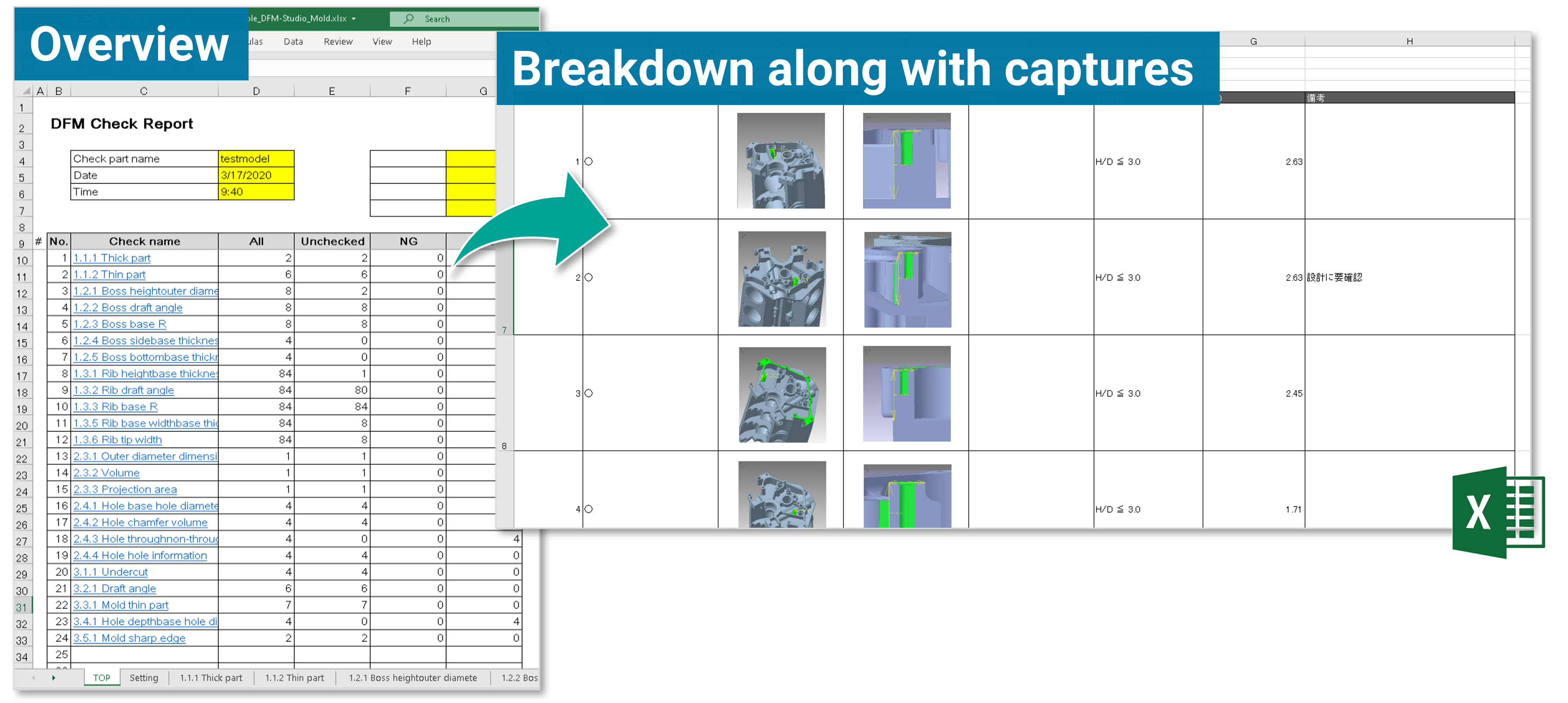
Key Features of DFX Analyzer
Fully-automatic
DFX Analyzer automates the detection of a wide range of geometric features, streamlining checks and ensuring consistent results regardless of the engineer’s background.
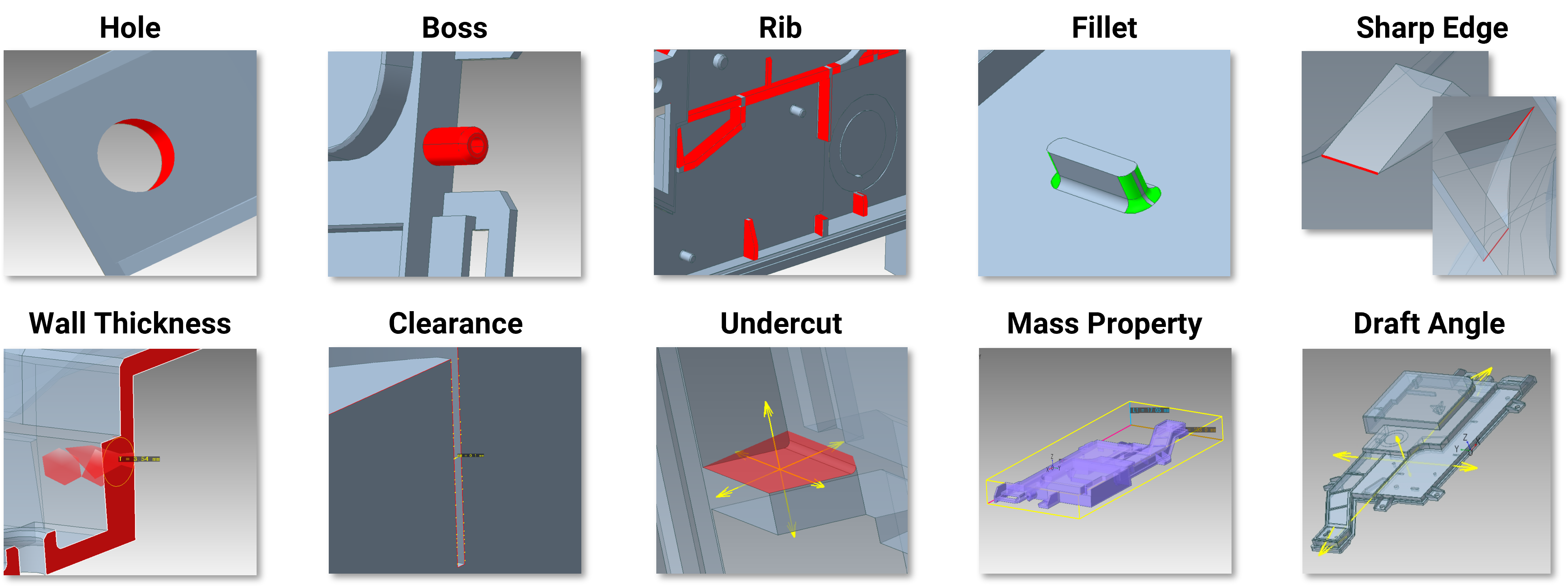
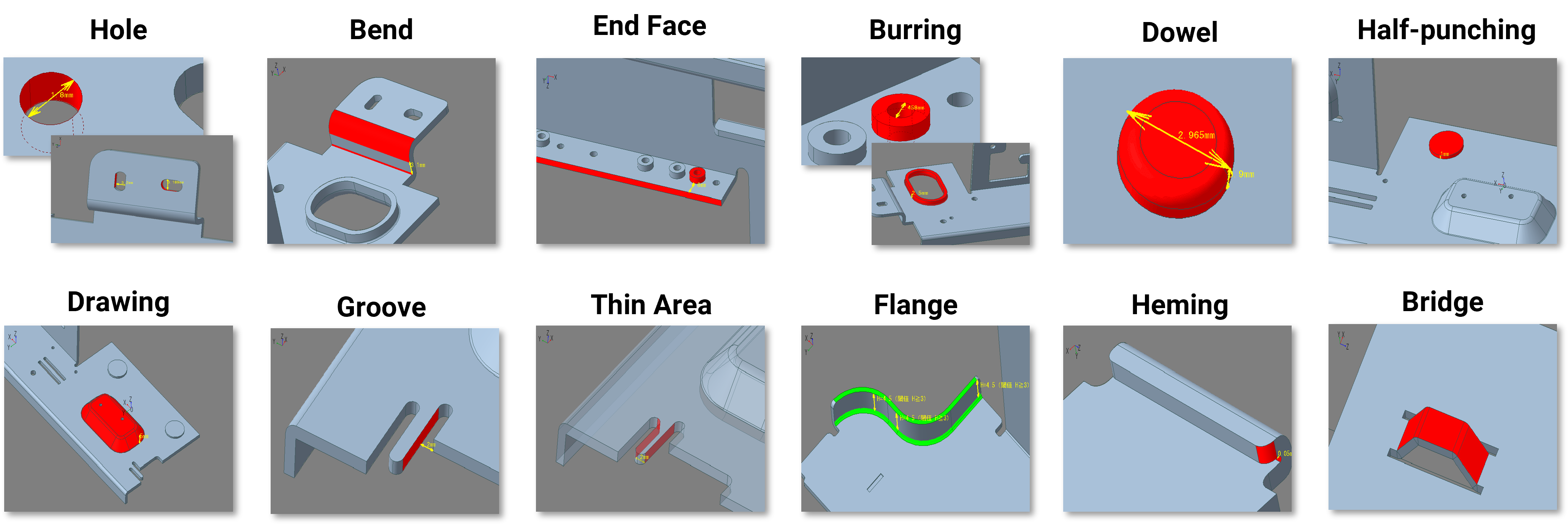
Customizability
Because DFX requirements vary by industry and organization, flexibility is essential.
With Geode SDK, a Python-based scripting engine, Elysium enables users to customize check logic to fit their specific needs. This adaptability has allowed Elysium to support custom checks for a variety of sectors and manufacturing processes.
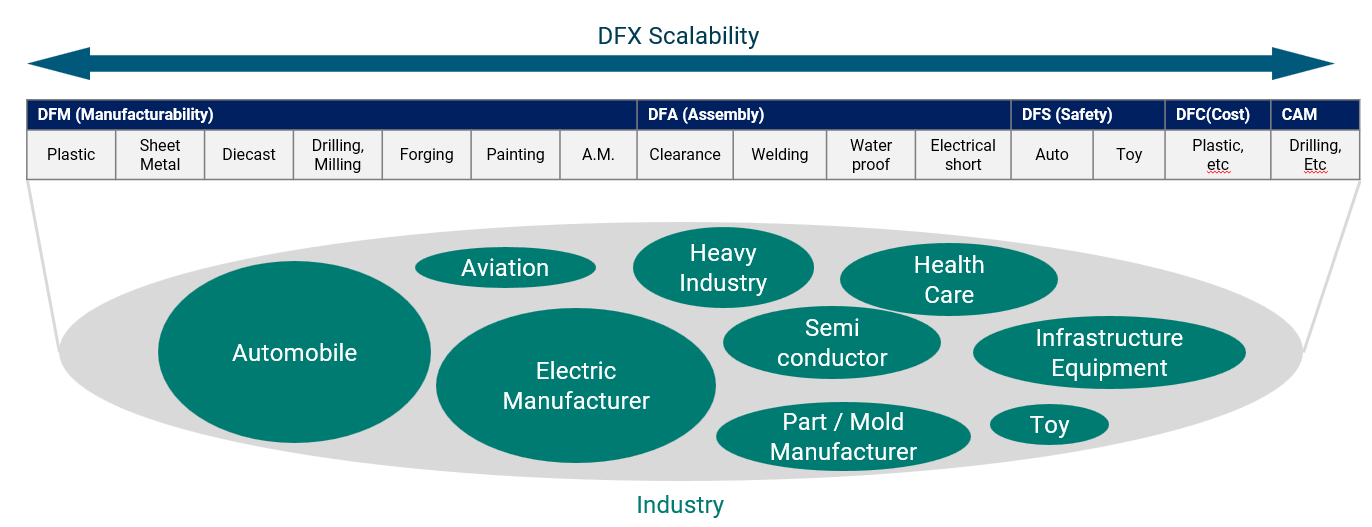
Interoperability
Modern manufacturing environments often involve multiple CAD platforms with differing capabilities. Each platform typically has its own unique features and limitations, often requiring separate tools for different file formats.
DFX Analyzer, as part of 3DxSUITE, supports all major CAD systems, including neutral formats like STEP and JT—making it a versatile, cross-platform solution.
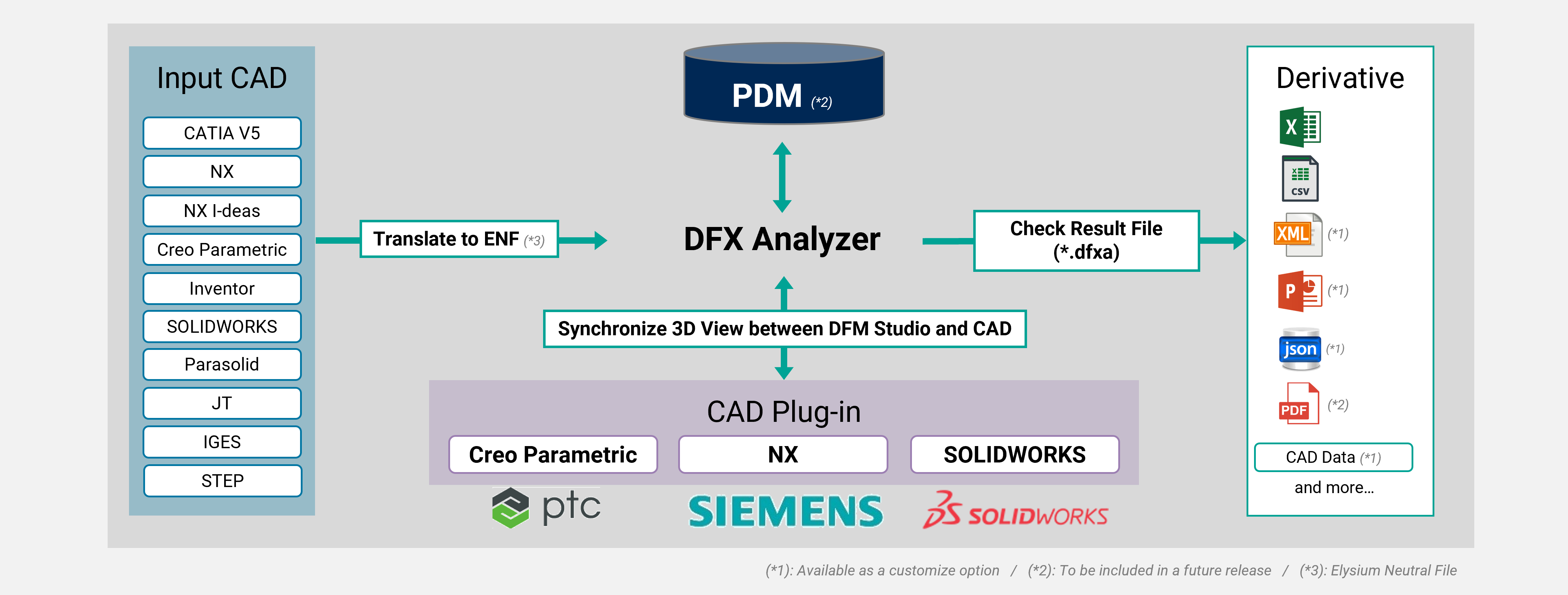
Where to Start?
Implementing DFX using CAD data isn’t a one-click process—but it starts with taking the first step.
Elysium offers a suite of out-of-the-box DFX checks for:
-
DFA: Assemblability
Ready to bring DFX to your design workflow?
Contact Elysium today to learn more!