In recent years, advancements in point cloud handling technology have led to a diverse array of tools in the market. Amid the ongoing digital transformation, the integration of 3D scanning and point cloud technologies has empowered the implementation of robust engineering solutions and revolutionized processes like Scanning to CAD, BIM, and CAE.
Benefits of Point Clouds
The primary advantage of employing point cloud technology lies in the digitization of physical objects. Utilizing 3D scanners simplifies the process of converting physical objects into point cloud data as a more straightforward and cost-effective approach compared to creating digital data from scratch using CAD or CG software. Another key benefit is the precision of reproducibility. 3D scanners enable the creation of accurate 3D digital data by capturing physical objects. This is particularly useful in cases where manual reproduction in CAD/CG software would be challenging.
Expanding Applications of Point Cloud Utilization
Digitalization of Products and Parts in Manufacturing
Over the years, point cloud technology has become a crucial asset in the manufacturing sector. One of its typical applications is generating data for simulating automotive parts or electronic components using Computer-Aided Engineering (CAE). Additionally, 3D scanning is employed to create part or mold data and inspect produced components by comparing them to the original digital data.
In these instances, scanned point cloud data must undergo transformation into polygon and Computer-Aided Design (CAD) models, commonly referred to as reverse engineering. The challenge lies in generating highly accurate CAD data from a point cloud, especially in areas where no points have been captured or where there is unevenness in the points. Even with acceptable point cloud quality, creating CAD surfaces from the coordinate information of each point is not an easy process.
Elysium CADdoctor, available through the Altair Partnership Alliance, offers automated CAD model generation from point clouds. CADdoctor excels at transforming scanned data into a usable Boundary Representation (B-Rep) model. Should issues arise with your source point cloud or polygon data, CADdoctor has the capability to heal and optimize your data for precise results. Its reverse engineering features can automatically identify fillets and other elements, ensuring the delivery of high-quality surfaces.
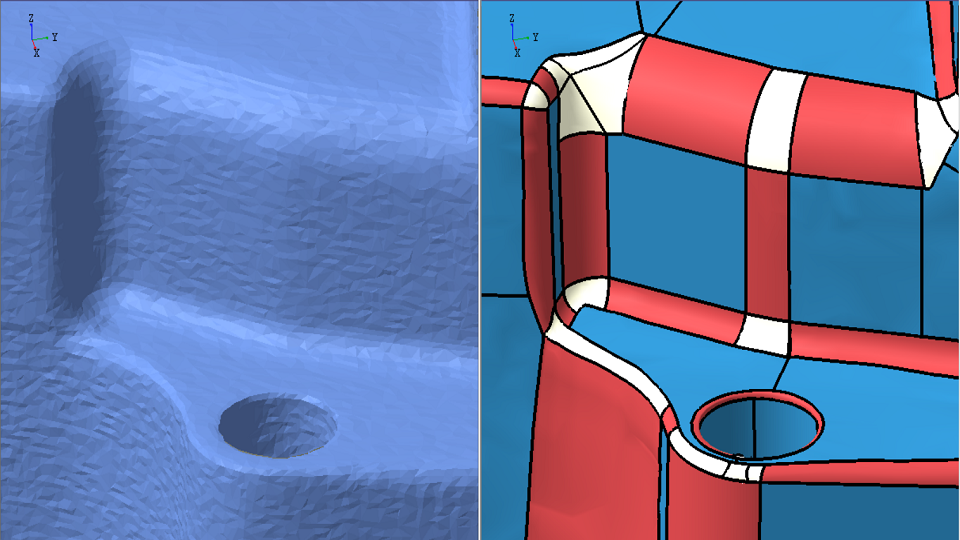
In the realm of CAE, there is a growing demand for quick and straightforward generation of models for simulation. The reverse engineering function of CADdoctor generates Brep models from scanned parts, providing efficient solutions to prepare models for CAE simulation.
Digitalization of Large Buildings and Structures
The trend of 3D scanning for large buildings and structures is on the rise, serving various purposes such as planning factory layouts, implementing facility changes, creating accurate as-built drawings, and verifying evacuation routes and work pathways. Often, existing buildings, factories, and infrastructures lack comprehensive drawings, and even when available, they might be partial or outdated due to daily on-site modifications or changes. Capturing point clouds through 3D scanning emerges as an effective solution, swiftly and accurately digitizing the actual state of diverse environments, including manufacturing facilities, commercial buildings, plants, bridges, roads, and infrastructure facilities.
Introducing Elysium InfiPoints, the latest release tailored for Altair Partnership Alliance users, providing a comprehensive solution to address these challenges. InfiPoints adeptly processes billions of points within point cloud data, automatically extracting geometries for modeling elements like planes, pipes, ducts, and steel. InfiPoints streamlines the process, ensuring efficiency and accuracy in capturing complex structures and layouts.
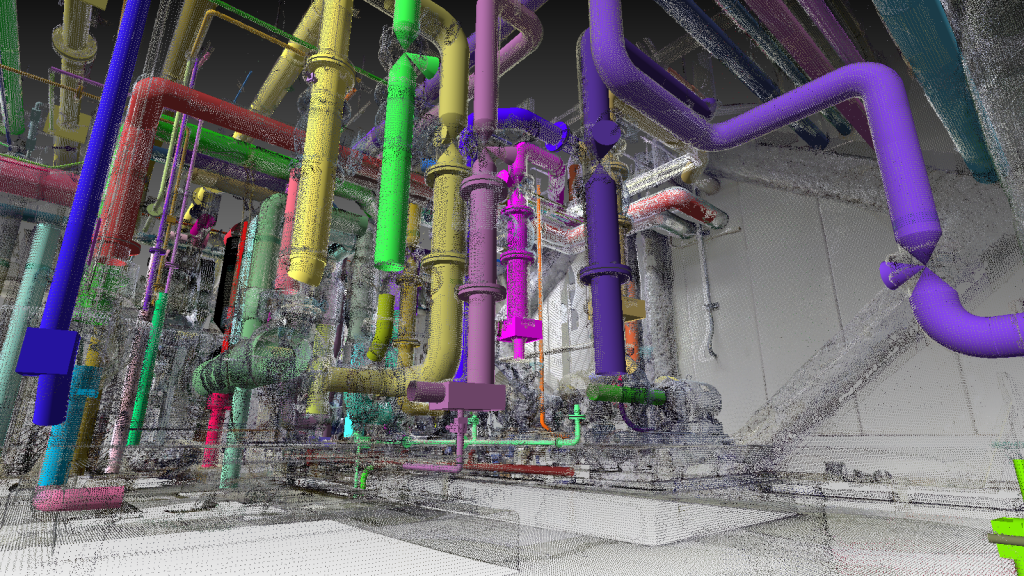
Scan to BIM Use Case
The integration of 3D Scanners and InfiPoints has revolutionized the process of equipment and facilities replacement/installation work. In the traditional approach, creating as-built drawings involved manual efforts based on on-site physical measurements. Even when existing drawings were available, they often proved inaccurate or failed to align with the actual equipment due to years of modifications. On-site physical measurements, particularly in high or inaccessible areas, were both time and cost-intensive, necessitating the use of scaffolds.
The innovative approach, leveraging 3D Scanners, InfiPoints, and Building Information Modeling (BIM) software, has resulted in a substantial reduction in the time required for replacement/installation work. InfiPoints preprocesses point cloud data, facilitating precise measurements of distances and angles within the virtual environment. It extracts planar and cylindrical geometry from the point cloud, automatically generating CAD models for equipment and piping systems that seamlessly integrate into BIM software.
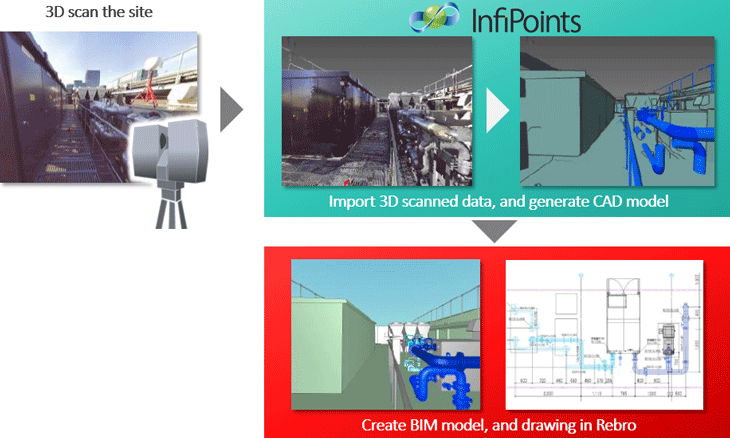
This advanced method, compared to the traditional manual creation of drawings based on on-site measurements, significantly shortens the lead time for BIM model creation, offering a more accurate and time-effective solution for the dynamic demands of equipment and facilities replacement/installation projects.
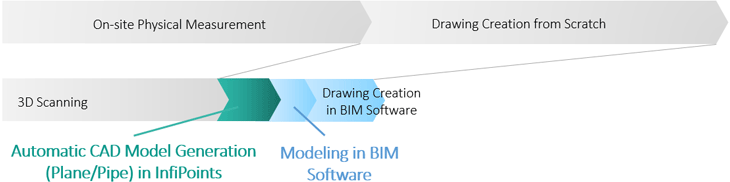
Scan to CAE Use Case
The synergy of 3D scanners and InfiPoints introduces a streamlined approach to 3D modeling for large interior spaces, with applications extending to Computer-Aided Engineering (CAE) simulations, including Computational Fluid Dynamics (CFD) and thermo-fluid analysis.
To begin, 3D scanners capture point cloud data for various interior spaces such as offices, restaurants, or entire buildings. InfiPoints then seamlessly extracts surface data, effectively composing a comprehensive representation of the space. This extracted surface data becomes a valuable asset for CAE simulations, particularly in applications like airflow analysis within specified spaces.
This innovative method significantly simplifies the Scan to CAE process, allowing for the seamless incorporation of actual-world conditions into simulations. By utilizing the 3D models generated by InfiPoints in CAE simulations, such as CFD and thermo-fluid analysis, organizations can conduct more simulations effortlessly, leveraging the true-to-life characteristics of the scanned interior spaces. This approach marks a significant advancement, enhancing the accuracy and efficiency of preparing models for CAE simulations based on the real-world environment.
Making an Impact with InfiPoints
InfiPoints stands out as a transformative software solution, converting raw point cloud captures into actionable deliverables. Widely adopted across multiple industries, including architecture, construction, shipbuilding, automotive, and more, InfiPoints caters to a diverse user base ranging from scan technicians, surveyors, designers, engineers, and quality analysts.
The impact of InfiPoints is evident in its demonstrated time-saving capabilities and quality assurance across various functions. Users benefit from its efficiency in quickly assembling multiple scan types, including terrestrial and drone scans, into a cohesive project. A notable example involves a hydroelectric project, where a user harnessed the combined point cloud to generate an accurate representation of exterior terrain and perform collision detection for the replacement of interior equipment during the overhaul of an existing facility.
In addition, InfiPoints serves as a powerful tool for creating floor plans or 3D models when documentation is unavailable or outdated. This multifaceted software solution empowers users to navigate complexities in their respective industries, enhancing both efficiency and accuracy in project execution.
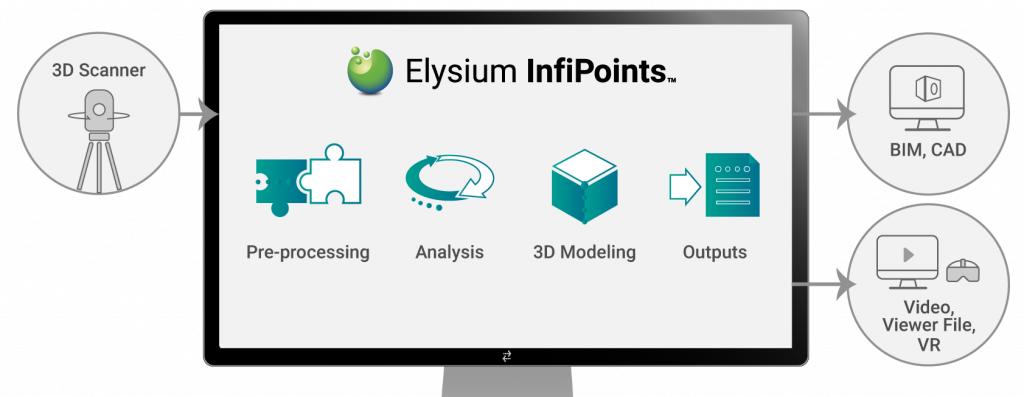