Executive Summary
Recent breakthroughs in 3D modeling—particularly the integration of laser scanning and point cloud data processing—have redefined how Computer-Aided Engineering (CAE) simulations are approached. With solutions like Elysium’s InfiPoints, engineers can now bypass time-consuming model recreation workflows by directly converting real-world scans into CAE-ready models. This white paper outlines the “Scan to CAE” methodology, its value proposition, and case studies that demonstrate measurable improvements in simulation efficiency and accuracy.
Introduction
As digital transformation accelerates across industries, 3D modeling technologies have become indispensable in fields like architecture, manufacturing, and infrastructure management. High-resolution laser scanning, paired with point cloud processing, enables the creation of accurate 3D models for large-scale interior and exterior environments. This capability becomes especially powerful when integrated with CAE tools for simulations such as:
- Computational Fluid Dynamics (CFD)
- Radio Wave Propagation Analysis
- Structural Integrity Analysis
Elysium’s InfiPoints software processes billions of point cloud data points, extracting geometric elements like planes, pipes, ducts, and structural components. As a partner of the Altair Partner Alliance (APA), Elysium provides an end-to-end “Scan to CAE” workflow that empowers engineers to conduct advanced simulations with high fidelity and speed.
Digitalization of Large-Scale Structures
The use of 3D scanning for digitizing large buildings and industrial structures is rapidly expanding. Its applications span:
- Factory layout planning
- Facility upgrades
- As-built documentation
- Safety planning and evacuation route design
Often, existing environments lack complete or up-to-date blueprints due to ongoing modifications. Laser scanning offers a fast and precise solution for capturing spatial data. Facilities such as commercial buildings, manufacturing plants, bridges, and infrastructure installations can all benefit from this digitalization.
Limitations of Traditional Workflows
Conventional CAE workflows often require manual model recreation using CAD tools—especially when original documentation is missing or obsolete. This not only consumes time and labor but also distracts CAE professionals from their core simulation tasks.
The “Scan to CAE” approach mitigates these issues by allowing direct model generation from real-world scan data. It removes unnecessary pre-processing and manual modeling
steps, enabling simulation teams to focus on analysis and decision-making.
Case Studies
1. Interior Space HVAC and Airflow Analysis
Maintaining optimal air circulation is critical for comfort and health, especially in post-pandemic building management. Using InfiPoints, a point cloud of an interior space was processed to generate a CFD-ready model.
- Number of scans: 9
- Scanning time: ~1.5 hours
- Total data points: ~96 million
- Point cloud pre-processing time: ~ 1 hour
- Modeling time: ~3-4 hours
- CAE Tool: Inspire Ver. 2024
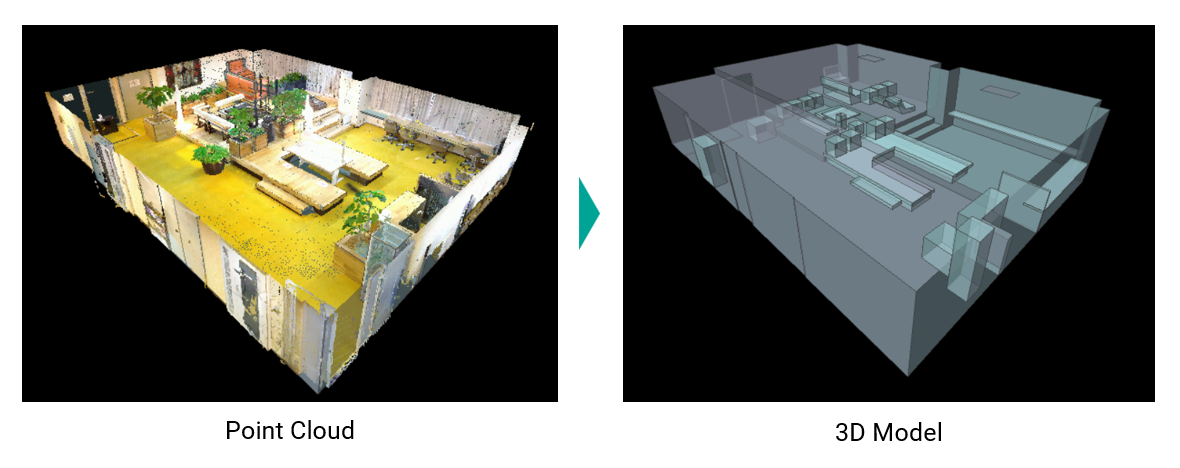
Picture 1: HVAC Analysis (CFD) Using Point Cloud-Based Model
(Simulation Powered by APA Using InfiPoints and Altair Products)
2. Interior Space Radio Wave Propagation
A similar dataset was used to simulate wireless signal behavior across a scanned environment, useful for network planning and IoT deployment.
- Scans and processing time identical to HVAC case
- CAE Tool: WinProp
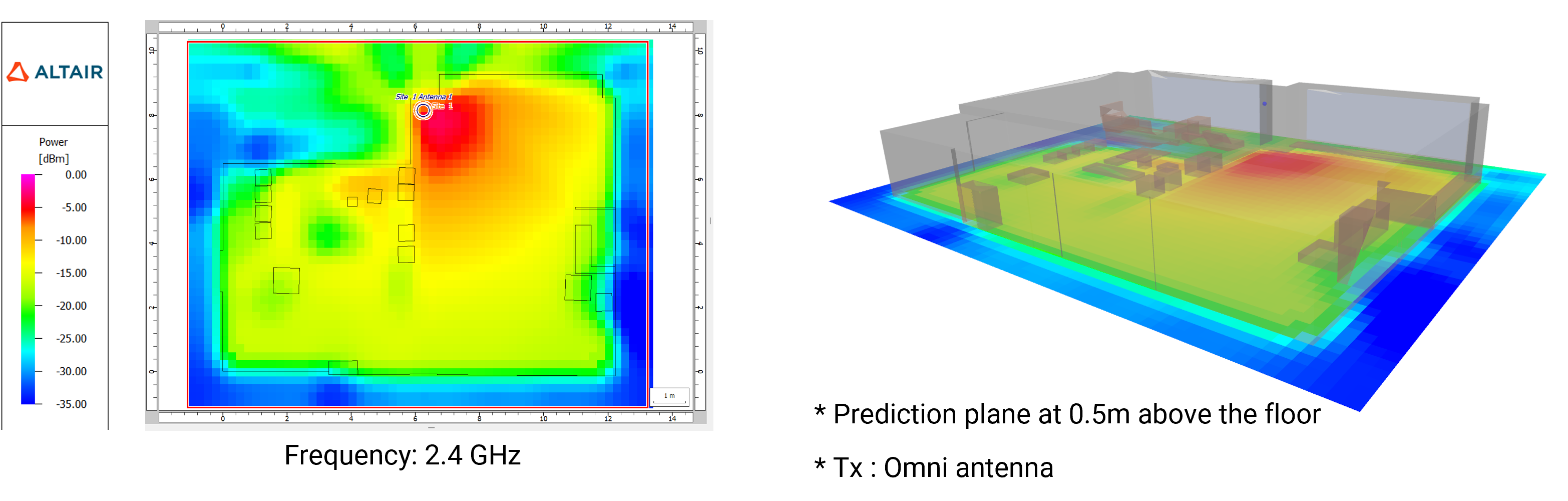
Picture 2: Radio Wave Propagation Analysis
3. Large Building Structure Structural Analysis
In a structural engineering application, the “Scan to CAE” process was applied to analyze resonance and static load-bearing behavior.
- Number of scans: 6
- Scanning time: ~ 1 hour
- Total data points: ~ 250 million
- Point cloud pre-processing time: ~ 1 hour
- Modeling time: ~ 0.5 hours
- CAE Tool: Inspire Ver. 2024
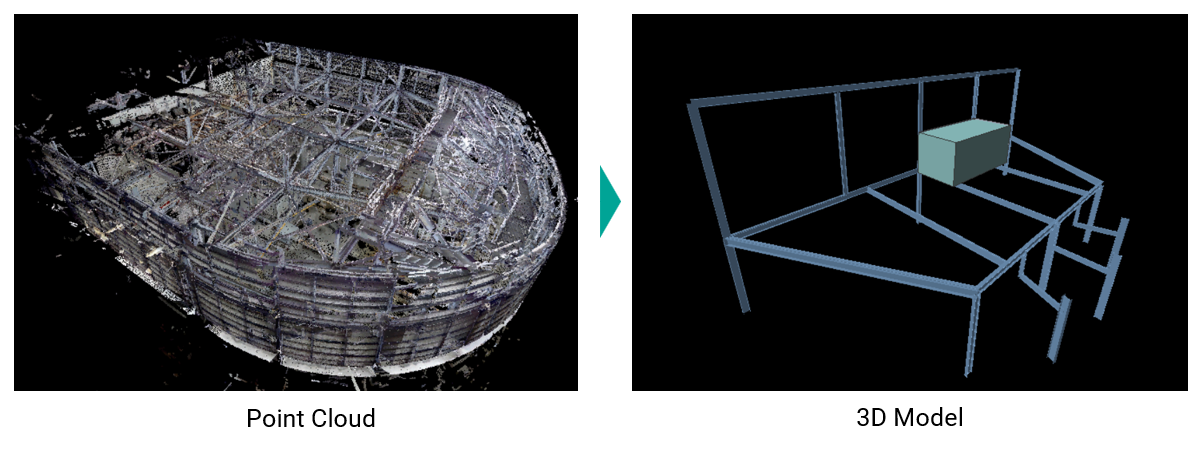
Picture 3: Structural Analysis Eigenvalue and Static Load
(Simulation Powered by APA Using InfiPoints and Altair Products)
Conclusion
The synergy between 3D scanning technology and InfiPoints software introduces a simplified and efficient method for preparing 3D models used in CAE simulations, including CFD, radio wave propagation, and structural analysis.
By capturing the physical environment of offices, commercial spaces, or large facilities with 3D scanners, users can generate accurate point clouds. These are then automatically processed by InfiPoints to extract surface geometries that are directly usable in simulation tools. This significantly reduces the burden on CAE engineers, who traditionally needed to recreate models manually—a process both time-consuming and often outside their core focus.
The “Scan to CAE” workflow improves simulation accuracy and accessibility by grounding the models in real-world conditions. It enables engineers to perform more simulations with minimal setup time, maximizing the value of actual environment data and enhancing the relevance of the results.