4. Essential to Successful MBD Model Distribution – Part 2: Data Quality
4.1 Simple Translation is Not The End
So far, we have explained the technology difficulty and importance of accurately translating 3D data into different formats. However, simply transferring information from left to right does not ensure the smooth distribution of MBD models. What becomes crucial is the quality of the translated data. The term ‘quality’ here refers to “how well it meets the requirements.” Regarding annotations and attributes, a wide range of requirements, rules, and representation methods across companies and tools make it challenging to confirm the quality easily. Elysium has developed a tool for users to customize each customer’s data translation and validation needs. The idea is to separate the validation process from the standardization, thereby promoting the distribution of MBD models.
An example of a customization product is ENF Editor. The tool allows users to set translation methods freely over Elysium’s proprietary file format, ENF (Elysium Neutral File). It enables advanced translation considering differences between companies or departments, such as assigning specific attributes to parts with certain colors. Setting conversion rules with ENF Editor enables outputting data as intended simply with a click, facilitating MBD model distribution without extensive effort.
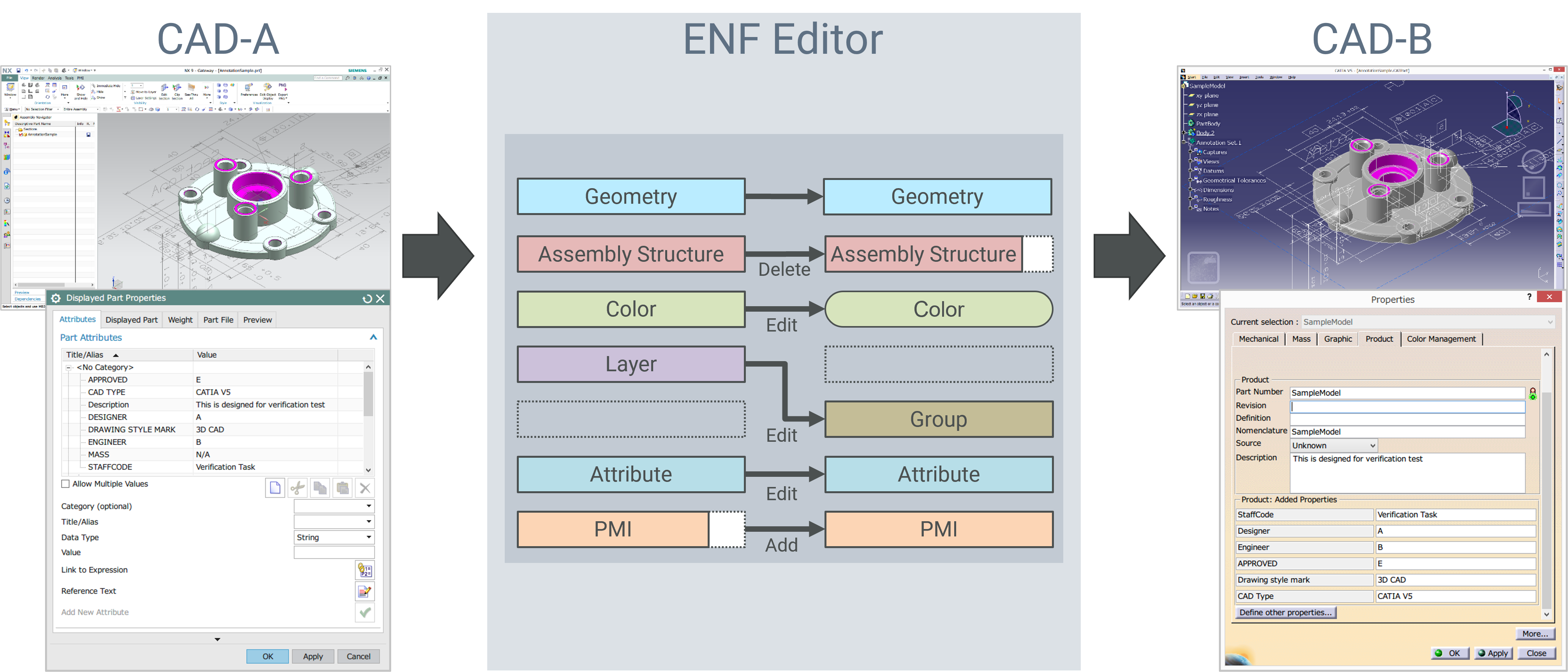
Figure 3. Customization example of data translation
4-2. Two Types of Quality Checks
Two primary methods to ensure data quality are validation of a particular data and comparison between before and after translated data to ensure their identity. Both processes are essential.
4-2-1. Validation of Design Data
(1) PDQ (Product Data Quality) Validation
Why do we need data validation and healing? There are four reasons for this.
The first three reasons are illustrated in Figure 1.
First, each CAD software and system has its mathematical representation of curves and surfaces. Second, there is a variation in the limitations of topological information expression between CADs. This discrepancy in representation methods and specifications reduces data compatibility. Thirdly, each CAD has different tolerance value sets. For example, in one software, if the gap between edges is within 0.1mm, the endpoints of those edges are considered identical, while in another software, with a smaller tolerance, those edges might be treated as separate.
In addition to these reasons, the fourth is the occurrence of manual errors that are hard for users to notice during data creation, like tiny gaps or duplicate surfaces. Finding all these data defects manually is nearly impossible.
Therefore, Elysium developed a solution to detect and correct(heal) these defects automatically.
This software is compatible with many CAD software and file formats. During data validation, the user defines the CAD type used in subsequent processes, and the tool sets the optimal validation items, providing users with detailed functionalities without hassle. In automated healing, users can set various parameters as needed, allowing flexible processing based on usage. For instance, if prioritizing the “surface smoothness” during product molding, settings can be adjusted to maintain the continuity of separate faces while healing other issues. Additionally, limiting the surface for modification is possible, preserving crucial design aspects. Thus, recognizing the need for detailed customization is crucial in pursuing digitization and automation.
(2) Design for Manufacturability (DFM)
In manufacturing industries, attention is shifting towards considering factors like moldability during initial product development, termed “Design for Manufacturability (DFM)“, and digital validation tools have emerged.
Ideally, achieving DFM involves designers comprehensively considering all manufacturing requirements to avoid issues in the manufacturing process. However, it is difficult for designers to reflect manufacturing requirements in their designs. Moreover, designers typically use internal design standards to improve design quality, but manual visual checks by designers can lead to oversight. Therefore, it is an incomplete preventive measure.
Elysium has software to support DFM checks. Automatically verifying the quality of models created by designers in 3D CAD systems against preset rules (design standards) enables designers to identify potential problems in the post-process. It reduces time and cost, improves design quality, and reduces the effort and time needed for subsequent processes. It can prevent costly rework or oversight if defects are pointed out in the product design department or discovered only after prototype creation.
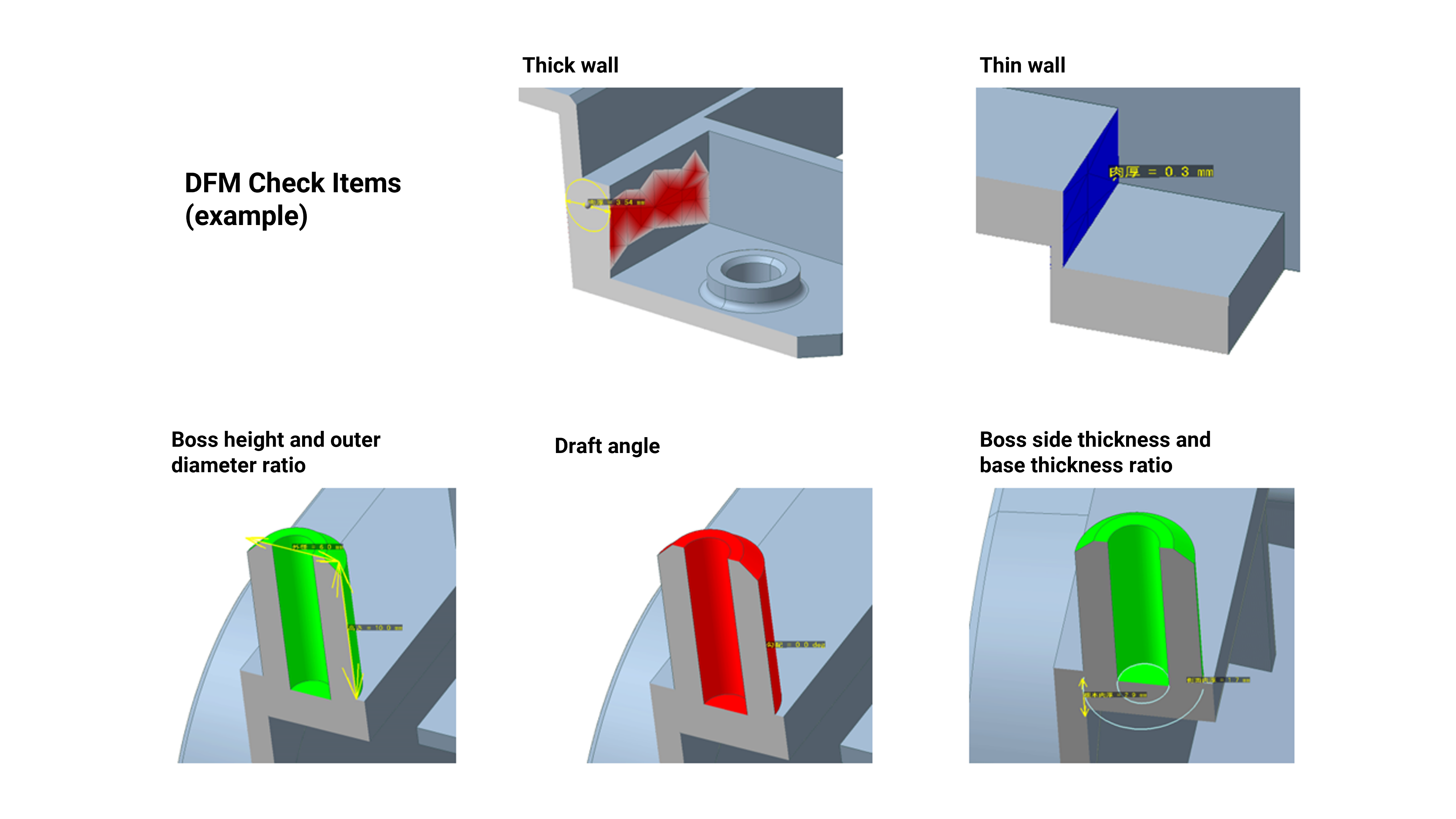
Figure 4. Example of DFM check with a CAD model
The check is run based on Elysium’s proprietary technology that can swiftly and accurately detect key features from CAD models. Advanced geometry recognition technology allows for pre-validation of design perspectives such as DFS (Design for Safety) and DFA (Design for Assembly).
4-2-2. Validating Between Multiple Data Sets
To integrate multiple tools via standard formats, ensuring the reliability of the data is crucial. Regarding the geometry information discussed so far, it is relatively easy to detect differences, such as missing surfaces or gaps. In contrast, machine readable information might go unnoticed if checked independently. Therefore, when validating machine readable data, “identity checks” using the original and current data become even more critical.
Elysium has the technology to compare and validate two CAD data sets in geometry, assembly structure, PMI, and attribute information. Validation results can be confirmed via a dedicated viewer or HTML/3D PDF format.
However, purely comparing 3D CAD data does not necessarily provide practically valuable results. Specifically, verifying only meaningful differences is critical for practical use with a profound understanding of the specifications of the CAD software or data validation tool. Elysium deliberately allows customers to customize what they consider to be differences.
Moreover, the functionality to identify meaningful differences between two data sets is valuable for detecting changes accurately during engineering change and confirming whether data has been altered due to CAD software upgrades. It is crucial for establishing an efficient manufacturing process, ensuring complete detection of changes and accelerating communication for subsequent stages.
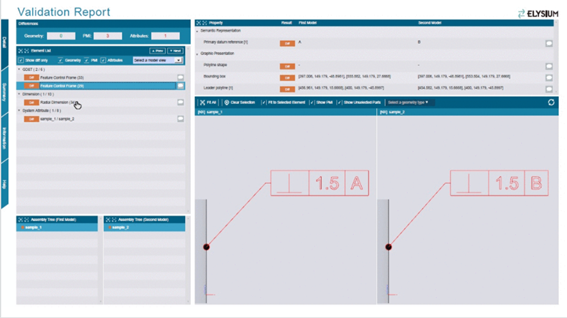
Figure 5. CAD data validation report
5. From Data to Knowledge and Wisdom—Future of Manufacturing Digital Transformation (DX)
Various initiatives based on practical experiences and a sharp vision of what should be necessary are required to achieve manufacturing DX. The DIKW (Data, Information, Knowledge, Wisdom) pyramid is often referenced when discussing data utilization. We can apply this framework to 3D data, which plays a significant role in manufacturing DX.
We can map 3D data elements onto each pyramid layer. The mathematical geometric information is at the base as “data.” With attributes, it becomes “information.” If the information is satisfactory for humans to engage in manufacturing—that is, if it is human readable, this stage is adequate. By adding design procedures, tolerance instructions, and other information pertinent to manufacturing, the data ascends to “knowledge.” The additional enriched information transforms the data into machine readable data that software can process automatically.
Over the past decade, Elysium has progressively elevated its technological capabilities, starting from the base of this pyramid. Initially, Elysium focused on enhancing compatibility between different geometry formats at the base for data translation and validation. Subsequently, Elysium developed simplification and reverse engineering to create CAD models from point clouds. Both endeavors provided meaning to mathematical geometry “data” and converted it into “information.”
Now, the momentum of DX is gaining attention across industries. Elysium has positioned the utilization of machine-readable 3D models, PMI, attributes, and annotations as one of the most critical development goals. The aim is to digitize human “wisdom,” which significantly changes data utilization efforts and is one of the most vital areas to focus on for manufacturing DX.
To ensure “digital transformation” brings actual changes in the manufacturing sector, aiming for the ideal image of digitizing human wisdom, as described above, is necessary. At the same time, adapting DX based on each company’s practical constraints and operational realities is also essential. Based on the technology and knowledge Elysium has cultivated over the years, continues to improve existing technologies and develop innovative ones.
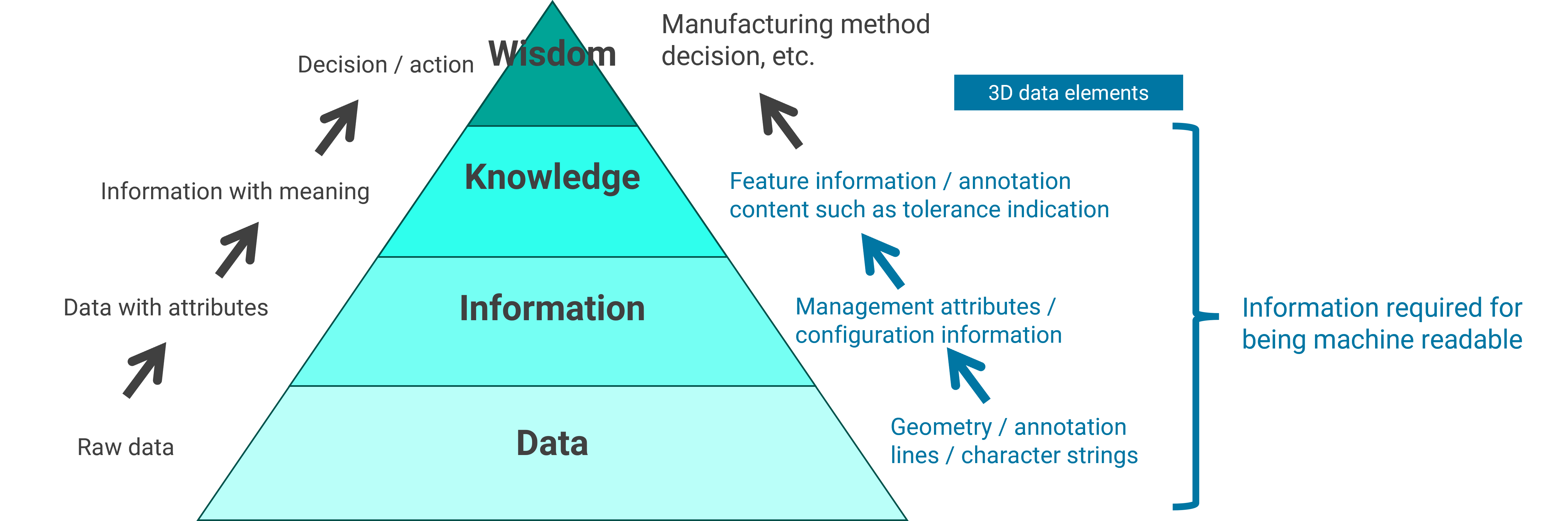
Figure 6. DIKW pyramid and 3D data elements