1. Pitfalls of Digitalization in Manufacturing
Decades have passed since 3D CAD software was introduced into the workflow of design departments in many manufacturing firms. Unlike the previous methods that relied on specialized knowledge and experience to envision 3D objects based on 2D drawings, it is currently natural for anyone to subconsciously grasp the final form of a product starting from the design stage. With the spread and gaining popularity of Product Data Management (PDM) systems for managing product data and solutions for translating 3D data among different formats, 3D data is now being shared not only in the design phase but throughout numerous processes in manufacturing.
It may seem that the manufacturing industry has determined a mechanism for manufacturing based on 3D data and is moving towards digitalization. However, reliance on 2D drawings and paper documents to supplement necessary information besides the geometry is still relatively high. Focusing solely on “digitalization” and unthinkingly incorporating 3D data and digital tools into manufacturing can create a sarcastic situation where analog manual work increases. In this process, some companies are blinded to streamlining the manual work, losing sight of digitalization’s true purpose and meaning.
2. Importance of “Model Based Definition” (MBD)
2-1. What is MBD?
To elevate the digitization of 3D data, there is a movement to consolidate necessary information into a single data source. A model that includes various attribute information (product manufacturing information (PMI), dimensions, annotations, quantities, etc.) attached to the geometry is known as “Model Based Definition“ (MBD). The MBD model’s PMI would contain information usually conveyed in a 2D drawing.
Efficiency can be dramatically increased if it becomes possible to pack all necessary information into a single MBD and use the same model throughout manufacturing. Creating an ecosystem for MBD model interaction will lead to the manufacturing industry’s future growth. However, creating such a system is not easy. In the modern era, global partnerships and alliances have become the common ground. It is extremely rare for two companies in a partnership to use the same CAD software. Exchanging data between different software almost always results in issues, making it nearly impossible for both companies to share MBD Models 100% automatically.
2.2 Expectations and Reality of International Standard Formats
There is a growing expectation for 3D data international standard formats to resolve issues sharing MBD models across different CAD software. What kind of information should be stored will be discussed to achieve a seamless transfer between different software.
Examples of standard formats include JT and PDF. These formats come along with free viewers. It offers the advantage of accessing the 3D data without CAD software, eliminating the restriction of checking 3D data. It is user-friendly in downstream processes such as inspection, assembly, purchasing, logistics, and sales.
Additionally, another format, STEP, is an ISO format. For instance, the automotive and aerospace industries must store product information for decades ahead. To meet this requirement, the utilization of STEP AP242 is in progress. These formats encompass geometries, annotations, and attributes, aiming to realize MBD model distribution independent of CAD software. However, required attribute information in practical applications spans a wide range, and the implementation in the standard format has not yet caught up.
3. Essential to Successful MBD Model Distribution – Part 1: Data Translation
3-1. Adapting to Various Data Representations
Ideally, when sharing 3D data across processes or companies, it is most effective for each company to agree and adopt the same CAD software or format. However, in reality, different CAD software is chosen based on purposes and budget. The diverse domains required in the product development process make handling everything in a single software impractical. Even if the same CAD software is adopted, issues may arise due to version differences that hinder smooth collaboration. Prioritizing overall optimization can lead to inefficiency in individual tasks, which decreases the overall productivity of the process. Addressing these practical challenges involves translating 3D data into other file formats and achieving system interoperability through data translation technology.
“Translation” might imply a straightforward process of changing file extensions and outputting data. However, translating 3D data requires sophisticated processes. For instance, even concerning geometry, the representation differs significantly based on CAD (refer to Figure 1). It is not as simple as transferring information from left to right. It requires a genuine “translation.”
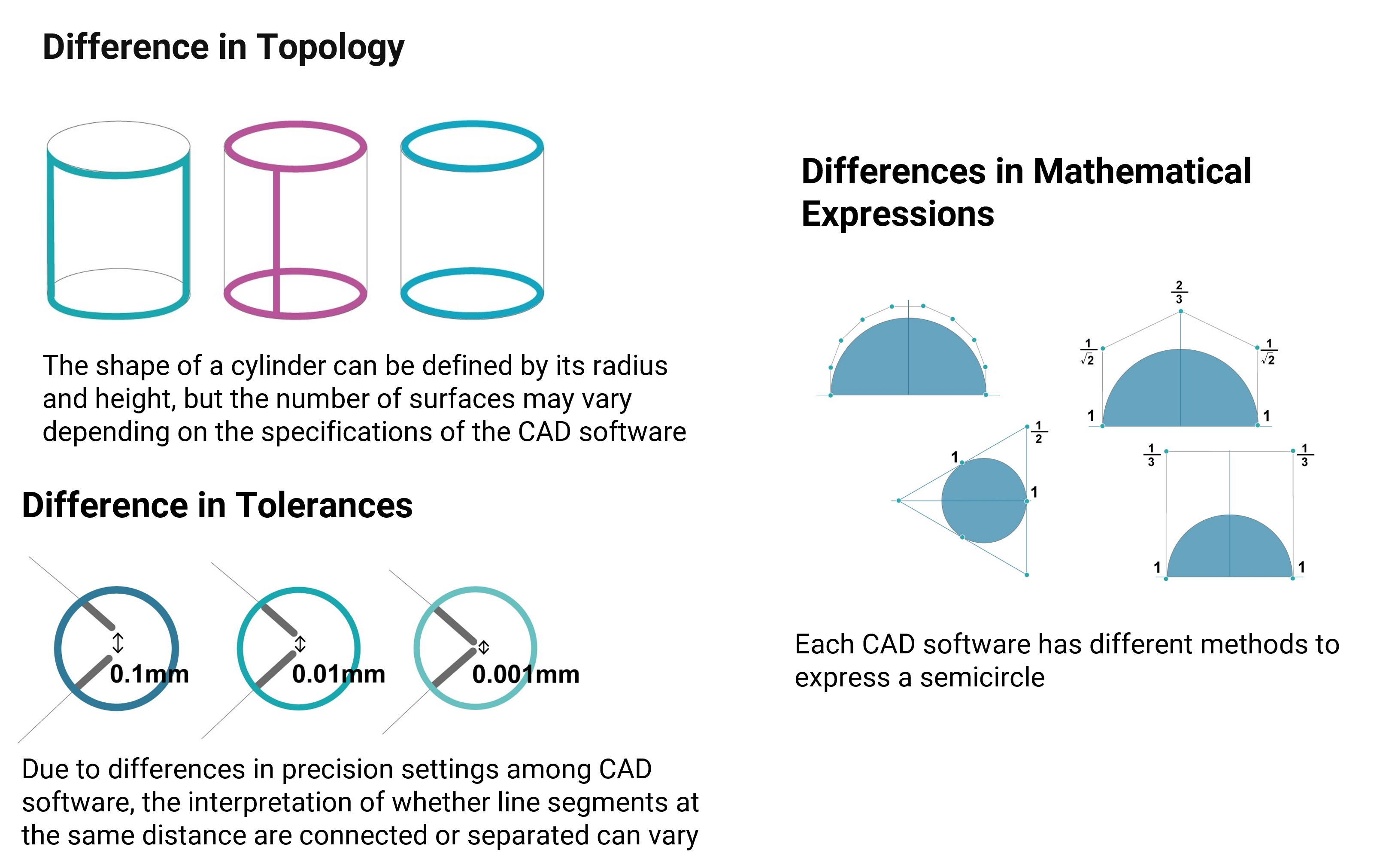
Figure 1. Issue examples arising from data translation
3-2. Over 40 Years of Data Translation Technology
Elysium has accumulated over 40 years of expertise in 3D data translation technology. High-precision data processing has been recognized based on proprietary algorithms leveraging mathematical insights and partnership with CAD software. Elysium provides technology to over 4,000 companies, including international companies like Daimler and Boeing and Japanese automotive or electronics manufacturers like Toyota and Nissan. Elysium is improving translation technology for product manufacturing information (PMI) and attribute information in 3D data translation.
3-3. Graphical and Machine-Readable Translation
Data translation technology is one step toward achieving a more advanced manufacturing process. As a fundamental effort towards digitization, MBD models need to follow the two points below.
The first is retaining information people can see and read, or human readable data. Rotating the 3D model on the screen allows a person to intuitively understand the geometry of an object and its image in the finished form. Features like text and drafting symbols expressed in 3D are also understandable to humans.
The second is having machine readable information for software (with attributes and annotations). It can be said that PMI can be both human readable and machine readable. One primary goal of MBD is to automate workflow to eliminate manual work.
We can say au revoir to manual work when software and hardware can automatically interpret the 3D data and act on it. Until this level is achieved, human interaction/confirmation work will remain. Fully automated is the ideal state of digital transformation, where humans are shifting towards more creative work. Elysium is continually developing technology that accurately converts Human Readable and Machine-Readable information, including PMI and attributes, regardless of the file format.
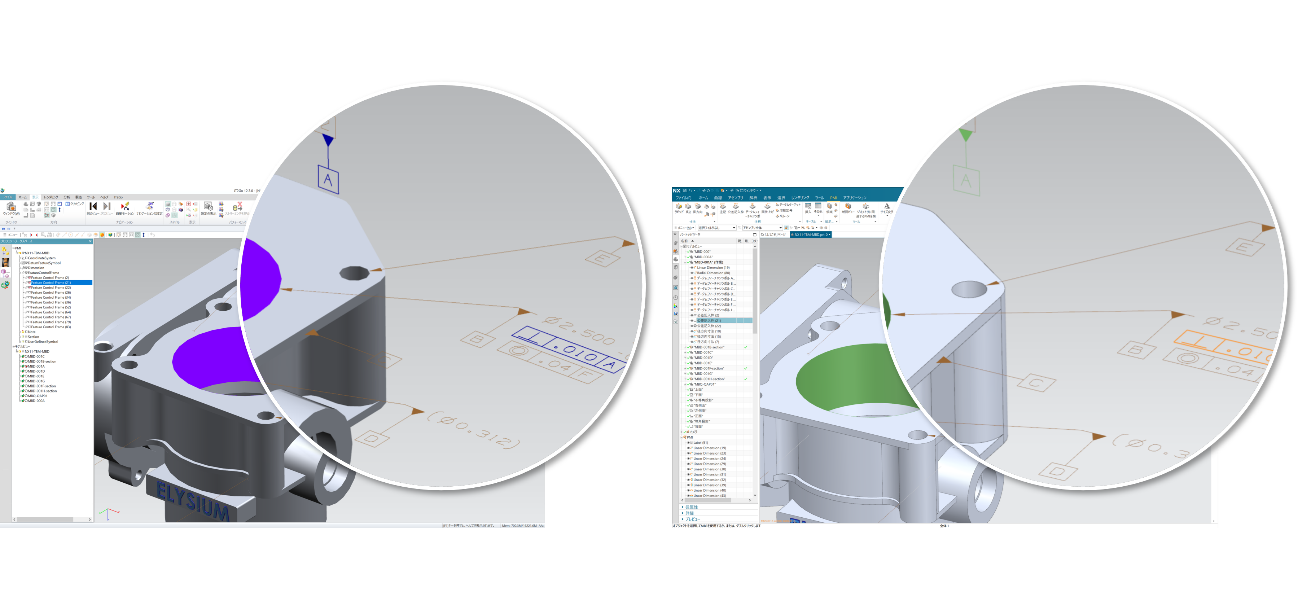
Figure 2. Example of translation from CAD native file to a standard format