4. 3DAモデル流通を成功させるための鍵② — データ品質
4-1. 単純な変換では不十分
これまで、3Dデータを異なるフォーマットに高い精度で変換する技術の難易度と重要性を説明してきましたが、実は変換時に単純に左から右へ情報を移すだけでは3DAモデルのスムーズな流通は実現しません。重要になるのは変換されたデータの品質です。
ここで言う品質とは「要件をどの程度満たすか」です。注記・属性については企業ごと、部門ごと、ツールごとに要件・ルール・表現方法が多種多様で容易にはその品質を確認することはできません。
そのため当社は顧客によるカスタマイズを前提としたデータ変換、および品質チェックを行うツールを開発しています。品質を確認する工程をあえて標準化の思想から切り離すことで、かえって3DAモデルの流通を促すという考え方です。
カスタマイズ前提の製品の例としては、当社のENF Editorが挙げられます。これはエリジオン独自のファイル形式であるENF(Elysium Neutral File)のデータを用い、顧客が自由に変換方法の設定を行えるツールです。例えば特定の色が付与されたパートには特定の属性を付与した上で変換するなど、企業や部門ごとの違いを踏まえた高度な変換を行うことを可能とします。ENF Editorでデータ変換のルールを設定すれば、ボタン一つで意図通りのデータを出力でき、手間をかけず3DAモデルの流通を実現することができます。
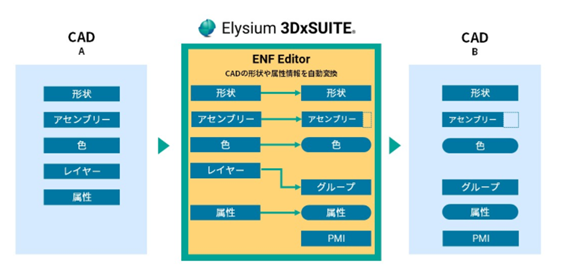
図3. データ変換のカスタマイズの例
4-2. 2種類の品質チェック
データ品質を保証する方法は大きく二つに分けられます。単体のデータをチェックする検証と、元データと変換後のデータを比べそれらが同一であることをチェックする同一性検証で、そのいずれも必要不可欠なプロセスです。
4-2-1. 設計データの単体でのチェック
(1) PDQ (Product Data Quality) 検証
そもそもなぜデータ検証や修正が必要となるのでしょうか。それには四つの理由を挙げることができます。
初めの三つは図1ですでに示したとおりですが、一つ目は、CADソフトウェアやシステムごとに曲線や曲面の数学的表現方法が異なることです。二つ目は、CADごとに要素のつながり具合を表現する位相情報の制限が異なることです。このような表現方法や仕様の差によって異なるソフトウェアやシステム間のデータの互換性が乏しくなります。三つ目の理由としては、CADソフトごとに設定されている許容誤差の値が異なることが挙げられます。例えば、あるソフトウェアではエッジの離れが0.1mm以内であればその二つのエッジの端点は一致していると認識しますが、別のものでは許容誤差の値がさらに小さいためにエッジは離れたものとして処理されるといった現象が生じます。
これらに加えて四つ目として、データを作成する過程でオペレーター自身も気づきにくい人為的なミスが発生することが挙げられます。微小な段差や重複面などがこれに当たります。
こうしたデータの不具合を人力でくまなく探し出すのは不可能です。
そこで当社はこれらの不具合を自動で検知し、さらに自動で修正までを行うソフトウェアを開発しています。
このソフトウェアはあらゆるCADソフトウェア・ファイル形式に対応しています。データ検証時に後工程で使われるCADの種類を設定すれば、自動的に最適な検証項目がセットされるなど、ユーザーを迷わせない細かな機能も持ち合わせています。
設計データの自動修正においては、ユーザーが各種パラメーターを任意で設定することができ、用途に応じた柔軟な処理を実行できることも重要なポイントとなっています。例えば、製品の成形時に重要となる「面のなめらかさ」を優先したい場合には、離れたフェースの連続性を保持して修正されるような設定を行うことができます。また、修正を施す対象面を限定することも可能で、デザインとして重要な意匠面を一切変更しないようあらかじめ指定することができます。
このように、デジタル化・自動化を目指す中でも、単に一括処理するのではなく細かくカスタムできる点も実際には必要とされることは認識すべき点です。
(2) DFM (Design for Manufacturability) のための検証
ものづくりの業界では、近年、製品開発の初期段階から成形性等を考慮した設計、すなわち「DFM(Design for Manufacturability)」に注目が集まっており、それをデジタルで支援する検証ツールも登場しています。
本来DFMを実現するためには、設計者が製造要件をすべて把握し、製造工程で不具合を発生させない設計ができるのが理想です。しかし現実には、設計者が製造要件を漏れなく設計に反映させるのは困難です。また多くの場合、設計者は出図前のデザインレビューで、社内の設計標準を用いて設計品質の向上を図っていますが、目視によるチェックでは抜け漏れが発生します。したがって、設計者自身による検証は、後工程での不具合防止策としては不完全なものとなっています。
当社は、DFMの実現をサポートするソフトウェアを開発しています。設計者が3D CADシステムで作成したモデルの品質を、あらかじめ設定したルール(設計標準)に照らし合わせて自動検証することにより、後工程で起こる潜在的な問題を設計者自身が発見できるソフトウェアです。
自動化によって検証にかかる時間やコストの軽減はもちろんのこと、抜け漏れのないチェックによって設計品質が向上します。設計部門で品質が改善されれば、当然後工程の確認プロセスの手間と対応時間が削減されます。一般的には、後工程になるほど不具合対策のコストが高くなるため、手戻りの軽減・防止の重要性は言うまでもありません。不具合を設計部門に指摘したり、不具合に気づかずに試作を進めてその後にようやくエラーに気づき、やり直したりするといった無駄も排除することができます。
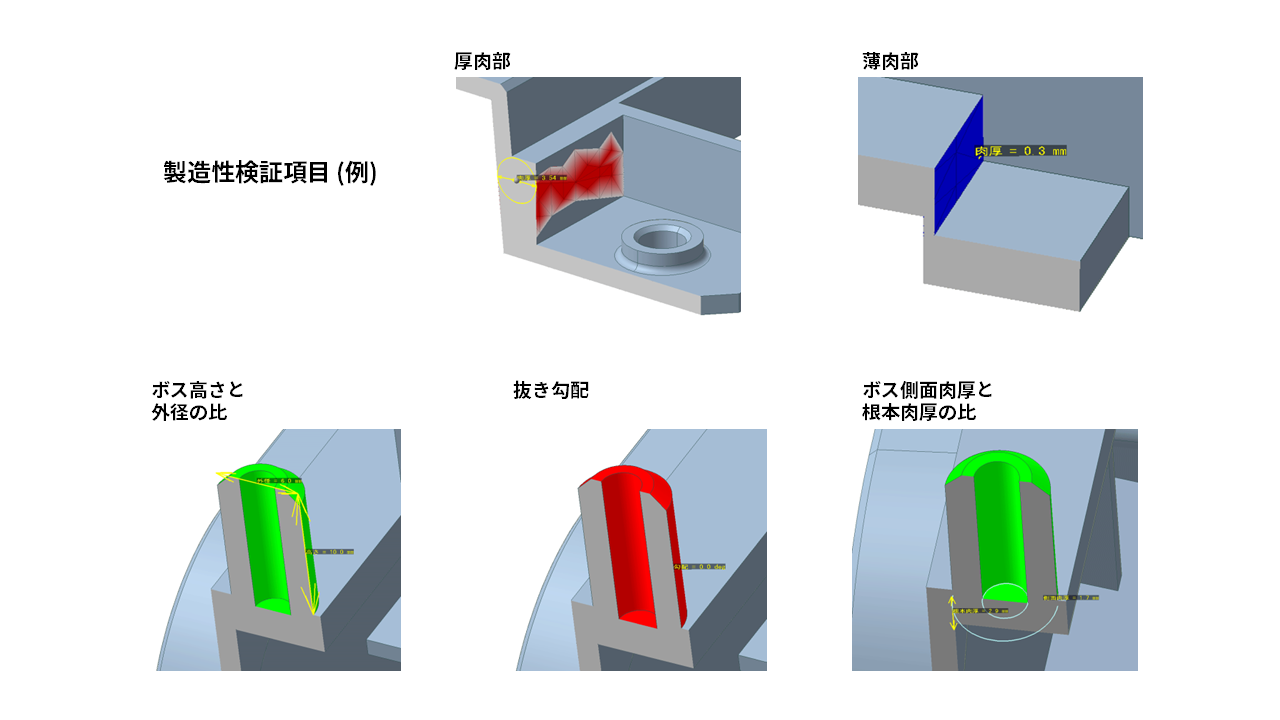
図4. CADモデルを使った製造性検証の例
このソフトウェアは、CADモデルから特徴形状を高速かつ高精度で検出する当社の独自技術がベースとなっています。形状認識の技術を発展・応用させることで、製造性の観点にとどまらず、例えばDFS(Design for Safety: 安全性)、DFA(Design for Assembly: アセンブリー組付性)といった切り口で、設計図の事前の検証が可能となります。
4-2-2. 複数データ間の同一性チェック
標準フォーマットによって複数のツールを連携させるためには、流通する標準フォーマットデータの信頼性、特に元データの内容が忠実に含まれているかという観点での信頼性保証が重要です。その中で、ここまで見てきた形の情報については、例えば面の欠落や接合の失敗など、比較的不具合を検出できる場合が多いと言えます。それに比べ、マシン・リーダブルな属性情報などは、情報の一部が欠落してもそれ単体をチェックするだけでは不具合に気づかないケースが多くなります。
そのためマシン・リーダブルなデータの検証を行う場合にはマスターデータと現在のデータを用いた「同一性検証」がより重要です。
当社は同一性検証のためのソリューションも提供しています。形状・アセンブリー構造・PMI・属性情報について、二つのCADデータを比較して漏れなく差異を検出する技術をもとにしたものです。検証結果は専用のビューアーのほかHTMLや3D PDFで閲覧することができます。
ただし単純に3D CADデータを比べるだけでは、ものづくりに有効な比較結果は得られません。具体的には、ユーザーが使用しているCADソフトウェアやデータ変換ツールの仕様を熟知した上で、意味のある差分だけを検証しなければ実用には耐えられません。
当社では、何を差異とするかを顧客が自ら設定できるカスタマイズ性をあえて持たせることで、この課題を解決しています。
なお、二つのデータを比較し意味のある差分だけを確認できる機能は、設計変更時に変更した箇所を漏れなく検出して後工程に伝えたり、CADソフトウェアのアップグレードによってデータに変更が加わっていないかを確認したりする場合にも有効で、効率的なものづくりのプロセスを確立するために不可欠な機能の一つと言えます。
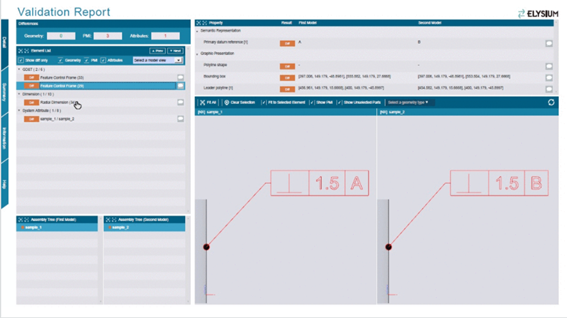
図5. CADデータ比較結果レポート
5. データから知識・叡智へ―ものづくりDXの目指す先
ものづくりのDXを実現するためには、単純にツールやフォーマットを採用するだけではなく、実務にもとづき、あるべき姿をしっかりと見据えたさまざまな取り組みが必要です。
データの活用が議論される際、よくDIKW(Data(データ), Information(情報), Knowledge(知識), Wisdom(叡智))ピラミッドが用いられます。これは、ものづくりDXの主役とも言える3Dデータにも投影して考えることができます。
ピラミッドの各層に 3D データに関する要素を当てはめると、まず数学的な形状情報は裾野にあたる「データ」に位置付けられます。そこに属性が加われば「情報」となります。人が介在してものづくりを行う、つまりヒューマン・ヴィジブルな情報を整備するだけならここまでで十分です。
そこに設計手順や公差指示など、ものづくりに関して意味を持つ情報を付加することでデータは「知識」に昇華されます。ここまで情報がリッチになって初めて、ソフトウェアが自動で処理を行えるマシン・リーダブルなデータとなります。
当社はここ十数年をかけ手掛ける技術領域をピラミッドの底辺から徐々に階層を上げてきました。
まず、裾野に位置する形状の異なるフォーマット間での互換性を高めるため、データ変換や品質検証の技術開発に取り組みました。続いて形状簡略化、点群からCADモデルを作成するリバースエンジニアリングを手掛けました。これらはどちらも数学的な形状の「データ」に意味を与え、「情報」とする取り組みであったと言えます。
そして現在、産業界全体でDXに注目が集まってきた追い風も受けて、PMI・属性・注記を含むマシン・リーダブルな3DAモデルの効率的な活用を重要な開発テーマと位置付けて取り組んでいます。それはこれまでのデータ活用とはレベルの異なる、人の「知恵」をデジタル化する領域であり、今後ものづくりDXにおいてもっとも注力されるべき分野です。
今後デジタルトランスフォーメーションというワードが単なる掛け声に終わらず、実際にものづくりの分野に変革がもたらされるためには、上述のような人の知恵をデジタル化する理想像を目指しながら、一方で各社の運用実態や現実的な制約を受け入れつつDXの効用を段階的に確認していくプロセスも重要です。当社もこれまで培ってきた技術や知見をベースとしながら、現場に寄り添うかたちで、既存技術の向上とその先にある革新的な技術の開発に今後も取り組んでいきます。
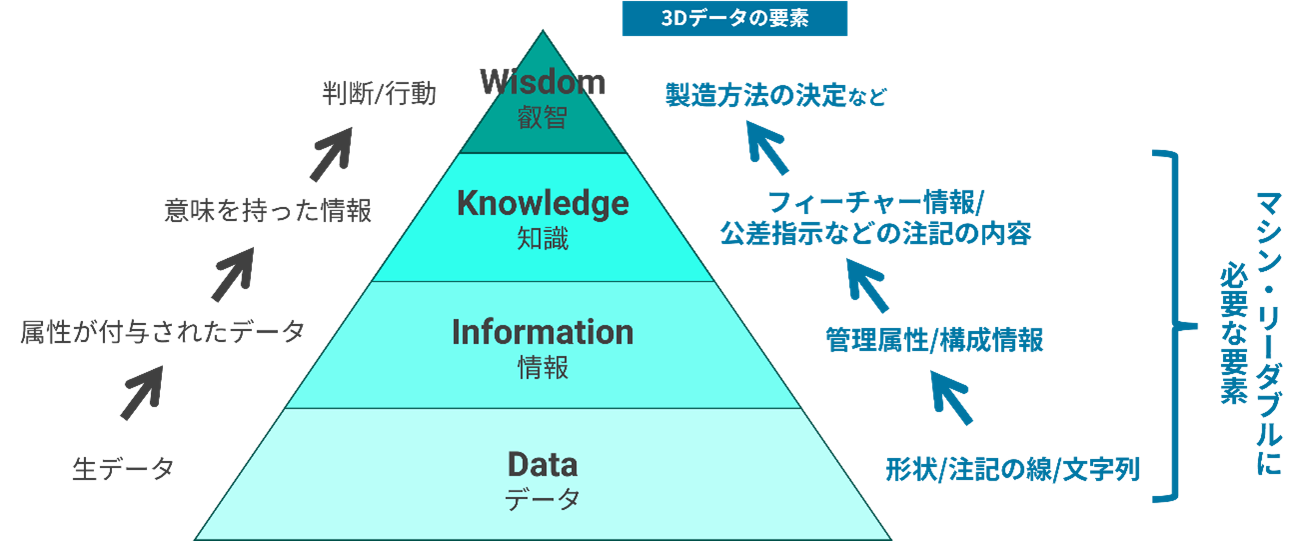
図6. DIKWピラミッドと3Dデータの要素