はじめに―DFM(Design for Manufacturability)の重要性
近年ものづくりの現場では、2D図面ではなく3D CADによる設計が主流となっています。ただ同時に、開発生産体制のグローバル化に伴う海外展開やベテラン技術者のリタイヤなどにより、企業にとって設計品質の維持向上は難しくなっています。設計品質が低いCADモデルは後工程で手戻りを引き起こす原因となり、効率的な生産プロセス構築の足かせとなります。そのまま改善がなされなければ、3Dでの設計プロセスやそのためのITツールの導入も、単なる見せかけのデジタル化となり、本来のデジタル化の目的である効率的で高品質なものづくりからかけ離れたものになってしまいます。
こうした背景から、現在3D CADデータをもとにしながら、製品開発の初期段階から成形性等を考慮した設計、すなわち「DFM(Design for Manufacturability)」に注目が集まっています。
本来DFMを実現するためには、設計者が製造要件を全て把握し、製造工程で不具合を発生させない設計ができるのが理想です。しかし現実には、設計者が製造要件を漏れなく設計に反映させるのは困難です。また多くの場合、設計者は出図前のデザインレビューで、社内の設計標準を用いて設計品質の向上を図っていますが、目視によるチェックでは抜け漏れが発生します。したがって、設計者自身による検証は後工程での不具合防止策としては不完全なものとなっています。
特に、ベテラン技術者のノウハウが社内で伝承されていなかったり、設計者個人の勘や経験が本人の中に閉じてしまい設計標準として共有されていなかったり、たとえ設計標準があったとしても全てのノウハウがそこに反映されていなかったりする企業や組織では、事前検証のレベルが低下し、設計品質のチェック時の抜け漏れが生じやすいと言えます。
ソフトウェアによる設計品質検証の自動化メリット
エリジオンは、DFMの実現をサポートするソフトウェアとしてDFX Analyzer (旧DFM Studio)を提供しています。本ソフトは、設計者が3D CADシステムで作成したモデルの品質を、あらかじめ設定したルール(設計標準)に照らし合わせて自動検証することにより、後工程で起こりうる潜在的な問題を設計者自身が発見できるツールです。
従来、設計者が個々に行っていた検証作業をシステム化することで、以下のような効果を得られます。
1.自動化による省力化と品質向上
通常、3Dモデルの検証作業は設計者の目視によって行われており、多大な手間と時間を要します。これを自動化することで設計者の負担は大幅に軽減されます。また、目視では見落とされやすい問題箇所もソフトウェアによって徹底的に抽出されるため、モデル品質の向上が実現します。
なお、DFX Analyzer (旧DFM Studio)では、データ検証後に設計標準を満たさない箇所が画面に一覧表示されます。そのため、設計者はリストを見ながら効率的かつ網羅的にチェックすることができ、短いリードタイムでデータ検証から修正までを完遂することが可能です。
設計者のチェックにかかる工数を減らすことは、製品の優れた機能性やデザイン性、低コストを実現する設計など、設計者が本来担うべき創造的な業務に集中できる環境の整備につながります。
2.手戻りの防止
設計部門で品質が改善されれば、当然後工程の確認プロセスの手間と対応時間が削減されます。一般的には、後工程になるほど不具合対策のコストが高くなるため、手戻りの軽減・防止の重要性は言うまでもありません。不具合を設計部門に指摘したり、不具合に気づかずに試作を進めてその後にようやくエラーに気づき、やり直したりするといった無駄も排除することができます。
3.設計・検証ノウハウの標準化
個々の設計者の知識に依存せず、高度な検証を実行することができます。経験豊富でスキルの高い設計者が有していたノウハウ(暗黙知)をシステム(形式知)化することで、組織として安定的に、高品質な設計が可能となります。特に、近年はベテラン技術者のリタイヤにより、厳格な検図を行える人材の不足が問題となっています。そうした状況でも、ソフトウェアが設計品質を担保し、組織として設計品質を維持することができます。
4.検証プロセスの低コスト化
設計品質を最終的に確認する方法として、現在は主にCADモデルをもとにしたCAE(Computer Aided Engineering)や試作が行われています。しかし、CAEを行うには解析者としての専門的な知識が必要な上、結果を判断する知見を要します。また試作時に確認した不具合とは異なる不良が量産時に発生するケースも少なくありません。DFX Analyzer (旧DFM Studio)を用いて設計データを検証することで、これらの手間やコストを大幅に抑えることが可能となります。さらに、検証が手軽にできることにより設計の早い段階で設計品質の検証を実行でき、その結果問題の発見が前倒しされ、トータルの開発コストが大幅に削減されるという効果も見込まれます。
DFX Analyzerの特性―かたちで見極める
ソフトウェアによるCADモデルの設計品質検証を可能にしている最も重要な要素は、エリジオンが有する形状認識技術です。エリジオンは35年以上にわたり、あらゆるCADシステムのデータ変換技術を提供し続けてきました。その中で、ユーザーがどのCADシステムを用いていたとしても、数学的な見地から、またCADシステム開発元からの公式情報を用いながら、意図した「かたち」を見つけ出すことができます。
「かたち」を検出できれば、次にそれが基準に適合しているかをジャッジし、さらに結果を見やすいレポート形式で出力すればプロセスの効率化を実現できます。DFX Analyzer (旧DFM Studio)にはその一連の機能が組み込まれており、ユーザーはシンプルな操作で、従来のような複雑で手間のかかる検証工程をスピーディーに完遂することができます。
大手製造業との協働で導き出したプリセット検証項目
エリジオンは、自動車・自動車部品・電機・精密機器など、これまで多様な製造業のユーザーにDFX Analyzer (旧DFM Studio)を提供してきました。その経験から得た知見をもとに、樹脂部品や板金部品の設計品質の肝となるチェック項目をDFX AnalyzerのDFM用のプリセット検証項目に反映しています。
検証項目例1: 製品肉厚
設計モデル内に厚肉部や薄肉部が混在すると、ヒケ発生や未充填等の成形不良の原因となります。
DFX Analyzer (旧DFM Studio)は肉厚を自動計測した後に基準値との差異を検証し、その程度を結果リストに表示します。設計者は検証結果のリストを見ながら、肉厚の変更の要否について効率的に、また抜け漏れなく検討することができます。
検証項目例2: ボス/リブ
設計したボスの先端基準で抜き勾配を付加した場合は、ボス根元付近の側面肉厚の増大(ヒケ発生の要因)に注意する必要があります。また、根元基準で勾配を付加した場合は、先端外径が小さくなることで充填不良が懸念されます。
DFX Analyzer (旧DFM Studio)では、一度問題箇所を修正した後も、関連する検証項目の結果を確認しながらその影響度を設計者がすぐに判断することが可能です。
検証項目例3: シャープエッジ
設計モデルに、意図せず製品シャープエッジや金型シャープエッジが発生することがあります。不要なシャープエッジは金型コスト、耐久性、成形品コストへの悪影響があるため、事前に全て検出し設計変更を検討する必要があります。
そのほかにも、アンダーカット・微小R・金型薄肉・穴・抜き勾配もプリセットされています。
板金部品向けプリセット項目
- 曲げ穴間距離
- 細い板幅
- 板厚
- ボス
- 丸バーリング/異形バーリング
- 穴
- ハーフパンチ
- 刻印
- 丸ダボ
- ブリッジ
- 張出し
- シンブル曲げ/フランジ曲げ/ヘミング曲げ
具体的な利用シーン
1. 日々のチェックと出図時の最終確認
DFX Analyzer (旧DFM Studio)を導入する企業の中には、設計者と検図担当者の両者がシステムを使っているケースがあります。例えば、設計者が日々の設計業務終了時に検証を開始し、帰宅している間にDFM Studioの処理を実行します。翌日その結果を確認し、必要であればCADモデルに手直しを加えます。こうすることで、時間を効率的に使いながらエラー箇所を残さず設計することができます。
また設計者が日々モデルのチェックと修正を行うことができるため、出図時のマイルストーンチェックでは検図担当者は必要最低限の確認をDFX Analyzer (旧DFM Studio)で行えばよく、検図にかかる手間を大幅に減らすことが可能です。
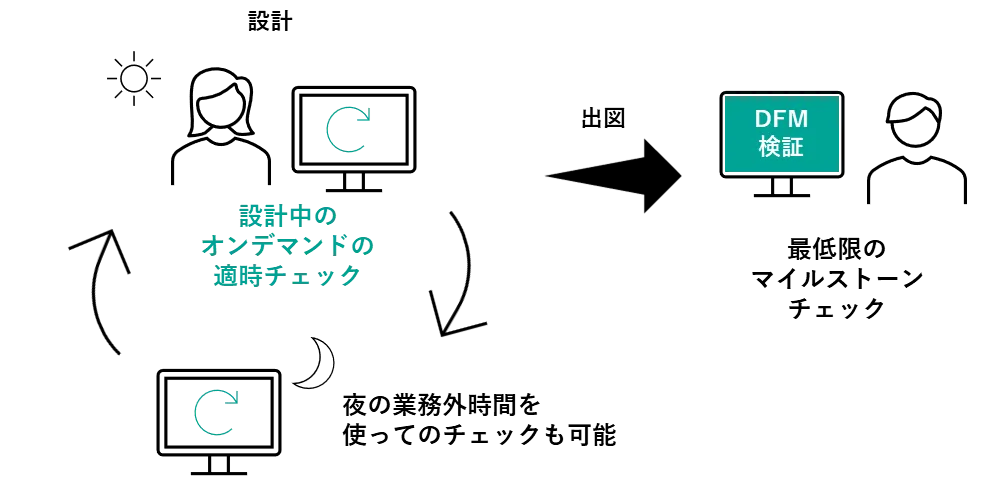
2. 若手技術者への技能継承
DFX Analyzer (旧DFM Studio)では、アプリ内から関連ドキュメントへのリンクを設定することができます。そのため、あらかじめ検証項目に関する説明資料を埋め込んでおけば、例えば若手技術者が自らDFM Studioでデータ検証を実行した際、問題として検出された項目が成形時にどのような不具合を引き起こすかといった知識や、どのように修正すべきかという知見を、DFM Studioからリンクをたどって確認したり学習したりすることができます。
若手技術者はそれを参考に設計の修正を行うことになりますが、多くの場合、一つ直せば玉突きで他の項目の不具合が発生するといった問題に直面します。そこで初めてベテラン技術者にレベルの高い質問を投げかけアドバイスを受けることで、経験値を飛躍的に上げることができます。
こうしたやり取りを逐次DFX Analyzer (旧DFM Studio)の検証項目や検証しきい値に反映させていくことができれば、システムの成熟化を図ることができ、結果として技術者個人の技量の向上と組織としての設計力の成長につなげられます。
個別のニーズも満たす拡張性
1. 検証項目のアレンジ
DFX Analyzer (旧DFM Studio)でプリセットされた検証項目については、エリジオンのこれまでの経験に基づいたしきい値の推奨値がデフォルト設定されています。そのままでも利用可能ですが、ユーザー自身で、製品の材質などに応じて個別に変更できます。
また、ユーザーが独自のルールに準拠するために、プリセットでは用意されていないかたちや計測箇所が必要となる場合があります。そのようなケースであっても、DFX Analyzer (旧DFM Studio)であればカスタマイズによってユニークな検証項目を作成することが可能です。なお、検証しきい値を含む各種パラメーターの一括編集や更新を手軽に行える専用ツールもDFM Studioの導入時に提供されます。
2. 既存システムの連携や運用を考慮した仕組み構築
DFX Analyzer (旧DFM Studio)はエリジオンの3Dデータ処理プラットフォーム3DxSUITE(スリーディースイート)に組み込んで自動処理させることも可能です。3DxSUITEは、大量のCADモデルを別のデータ形式に自動変換する機能を有しています。そのため、DFX Analyzer (旧DFM Studio)を3DxSUITEに組み込むことで、設計者らは製造可能性を検証した後の完成モデルを、後工程に控えている社内関係者や部品サプライヤーに自動で展開することができます。
さらに、3DxSUITEと既存のPDM(Product Data Management)システムと連携させれば、PDM上から設計データを指定し製造可能性に関する検証を実行することができるなど、3Dデータを用いたデジタルエンジニアリングのレベルを大きく高めることも可能です。
かたちを見極めることで実現する本当のデジタル化
この30年余りの間に、設計手法は手書きから2次元CADに変わり、さらに今では3次元CADが主流となっています。旧来は設計者のイメージを後工程の担当者がうまく解釈して現場で帳尻を合わせるといった方法が可能でしたが、3Dデータでは設計の曖昧さが排除されたことに伴って、後工程では設計モデルに忠実に成形するようになり、結果としてさまざまな箇所での不具合が生じるようになりました。言い換えれば、旧来は後工程のベテラン技術者が設計内容をよい塩梅で調整しながら設計者をフォローする余地がありましたが、3D CADが登場したことでそうしたサポートがしづらくなっています。
また、3D CADをはじめとしたデジタルツールの普及によって、皮肉にも、例えばデータの検証や変換といった手間のかかる工程を人が担うという新たな手間が発生しました。
2020年、新型コロナウィルス禍の影響で人々の働き方が大きく変化し、あらゆる分野でDX(デジタルトランスフォーメーション)の重要性が声高に語られるようになりました。これを機に、ものづくりに関わるエンジニアは再度、本当のデジタルエンジニアリングとは何かを考え直す必要があると考えます。
エリジオンは創業以来、マルチCAD環境での設計データの互換性を実現するさまざまなソリューションを提供しながら、一貫して製造業のデジタルエンジニアリングをサポートしてきました。
特に3Dデータから特徴的な形状を自動で検出する機能については、高度な数学力と35年以上にわたる実績をベースにして、世界でもトップレベルの技術力を培ってきました。CADモデルから特徴形状を高精度かつ高速に検出することで、本稿で紹介したDFM(Design for Manufacturability: 製造可能性)はもとより、DFS(Design for Safety: 安全性)、DFA(Design for Assembly: アセンブリー組付性)などさまざまな切り口での設計図の事前検証が可能になります。
ものづくりDXとは、ITツールを利用するがために発生してしまった手作業から技術者を解放し、技術者が本来従事すべき創造的な業務に集中できる環境を整備しなおすことから始める取り組みなのかもしれません。