かたちを見れば安全性を確認できる
今回は「特定のかたちを漏れなく見つける」と題したシリーズの2回目として、「危険な突起をデジタルの目で洗い出す ― 自動車安全基準チェックのための突起検証ツールDFAS」というタイトルでお話しします。
そもそもかたちを見ることがなぜ安全性の向上につながるか、皆さんは想像できるでしょうか。
例えば自動車では、使われる部品の材質が柔らかかったり、シートベルトやエアバッグなどの安全装備が備わっていたりすれば安全性が高くなるとイメージができると思います。しかし、そうした事後的な対応ではなく、自動車のかたちそのものを見直すことでも安全性を向上させることができます。安全性の観点から自動車のかたちを規制する国際的な法規もあります。本日はそうした周辺情報とともに、安全な製品・社会づくりに貢献するエリジオンならではの技術・商品を紹介します。
メーカーの内外突起規制への対応
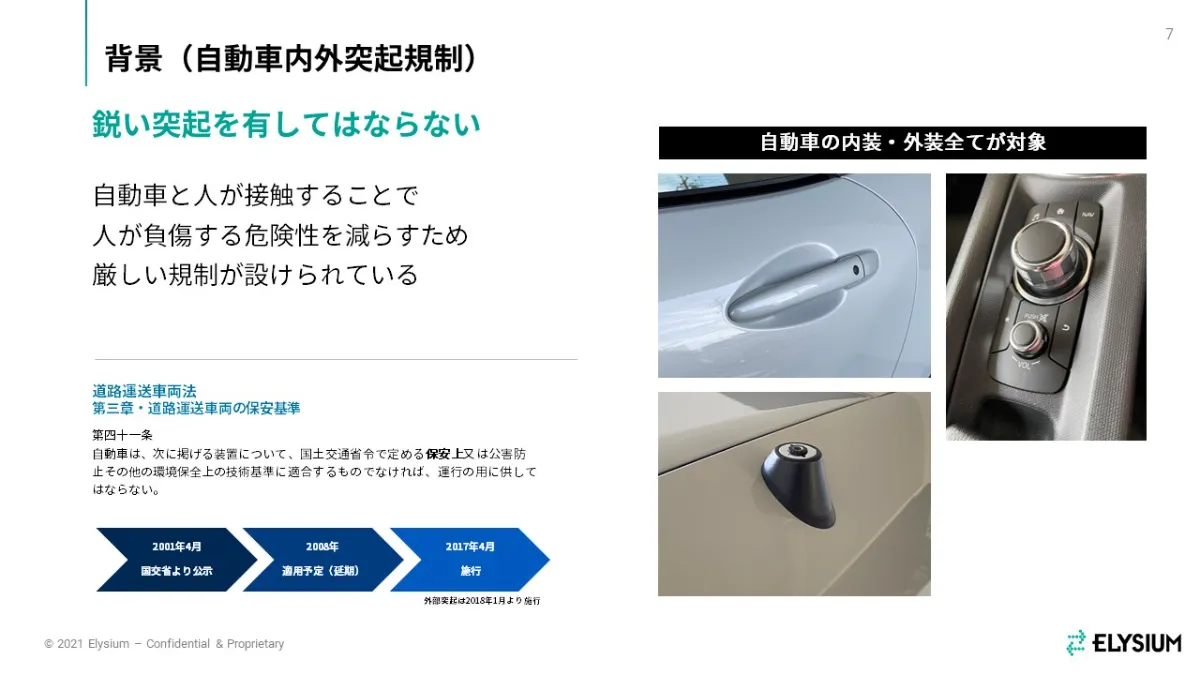
自動車メーカーやそのサプライヤーは「内外突起規制」を守るためさまざまな取り組みを行っています。この規制は、端的にいえば「自動車は鋭い突起を有してはならない」と定めたものです。事故が起こったときに、ドライバーや乗員、歩行者を自動車の鋭利なパーツで怪我をさせないことがこの規制の目的です。自動車の内装・外装を問わず全ての部品が対象です。
新車として市場に出される自動車は、必ずこの法規を守った仕様でなければならず、日本では、国土交通省から委託された独立行政法人自動車技術総合機構・交通安全環境研究所が最終的に審査しています。
突起検証プロセスの課題
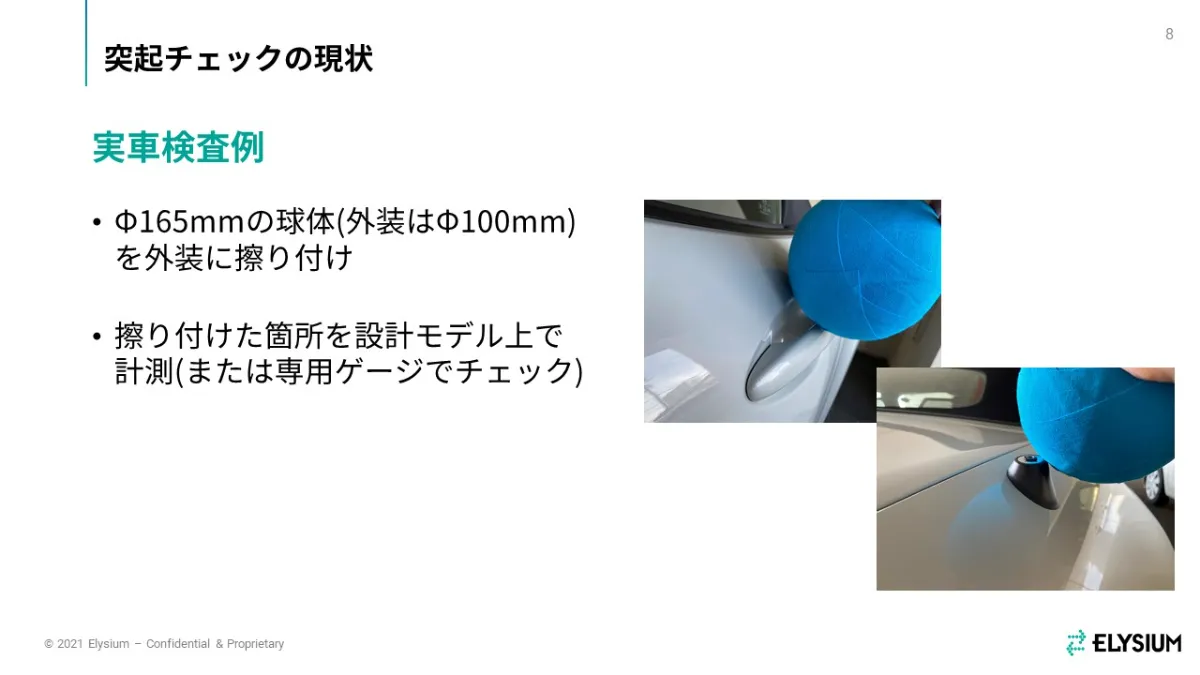
検査の一例を紹介します。
ご覧いただいている写真は球状の治具です。これは子どもの頭のかたちと大きさを模したもので、まずこの球体に粉を付け試作車の突起部分に当てます。粉の付着した箇所は子どもの頭が触れる可能性があるため、次にその部分の鋭さを確認します。直接Rゲージを当てて計測したり、Rゲージが当てられない部分は紙に印刷した図面を見ながら確認したりします。
このように、現在は人が手間と時間をかけながら試作車と治具を使って一つ一つ検証しています。
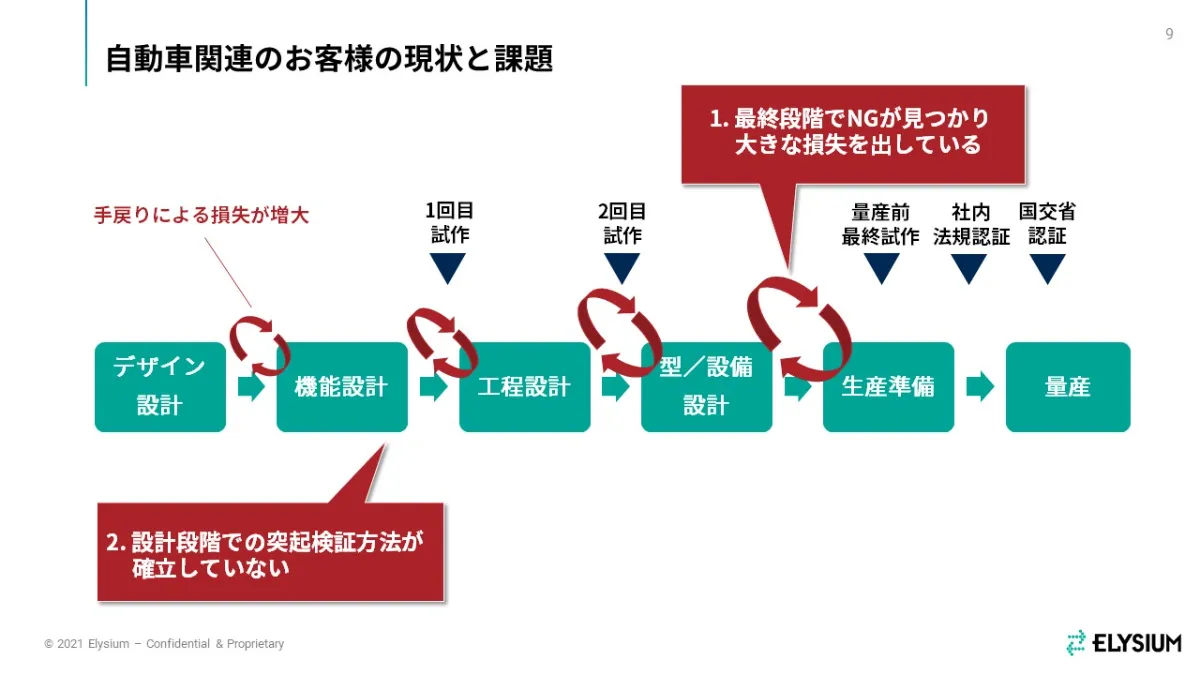
こうした人の手による検証には二つの問題があります。一つ目は、人力や目視では必ず抜け漏れが発生することです。二つ目は、部署ごとや個人ごとに検証方法がばらつき、検証の品質が保たれないことです。
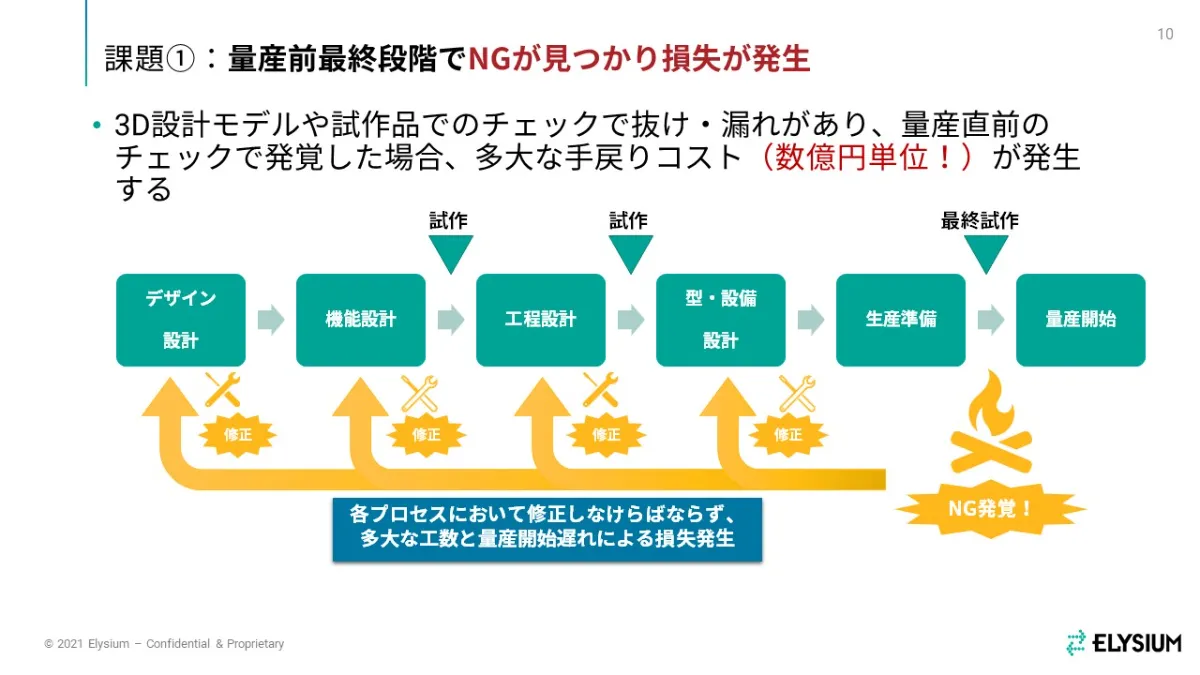
3Dの設計モデルや試作品を使って手作業で検証する場合、時間が限られているためどうしても問題が見過ごされ、量産直前になって大きな問題が見つかるケースがあります。その場合、上流工程までさかのぼってデータを修正したり、出来上がった物を作り直したりする必要があり、こうした手戻りによって数億円から数十億円の損失が発生することもあります。
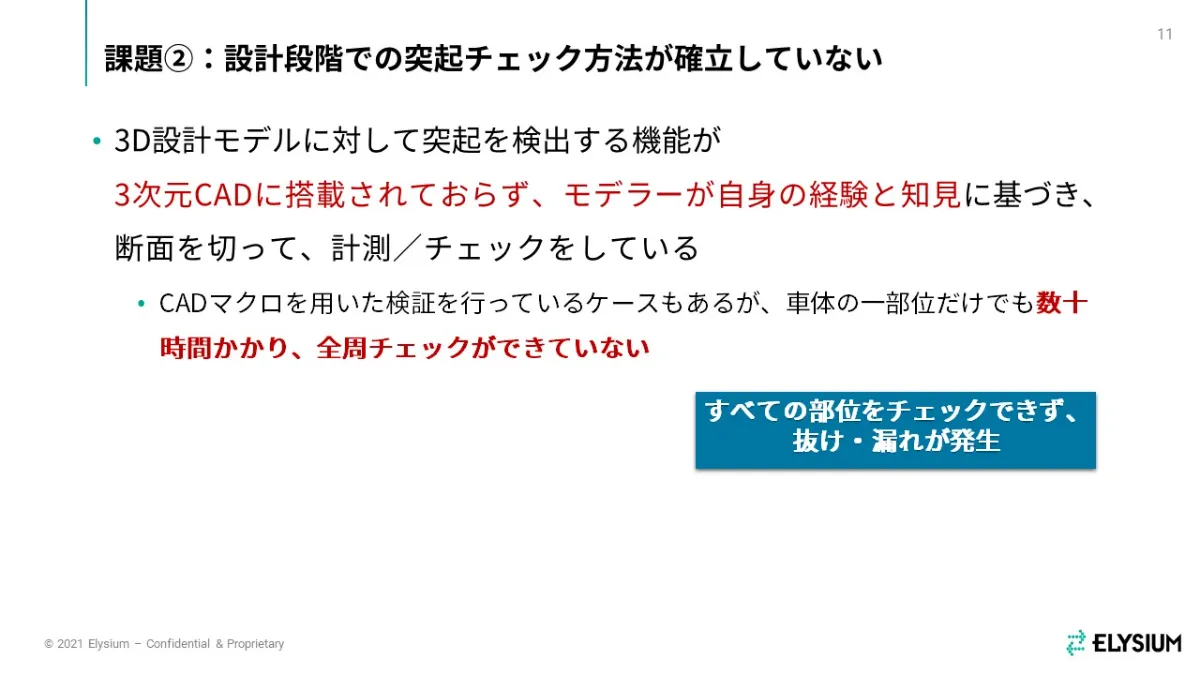
現在、業界を見渡してもCADモデルに含まれる突起を自動検出するソフトウェアは多くありません。そのため、メーカーごと、部署ごと、設計者ごとにやり方が違います。例えば、設計者が自身の経験に基づいて感覚的に場所を見定めモデルを輪切りにして断面を計測しています。このような方法では必ずチェックのばらつきや抜け漏れが発生します。メーカーの中には、CADソフトウェアのマクロ機能で一部の作業を自動化している例もありますが、その検証には長い時間がかかることが多く、例えば自動車の一部分の検証だけで数十時間かかり、時間切れのためそのまま次の工程に進んでしまい後工程で重大なエラーが見つかるといった問題も起きています。
内外突起検証を自動化するElysium DFAS
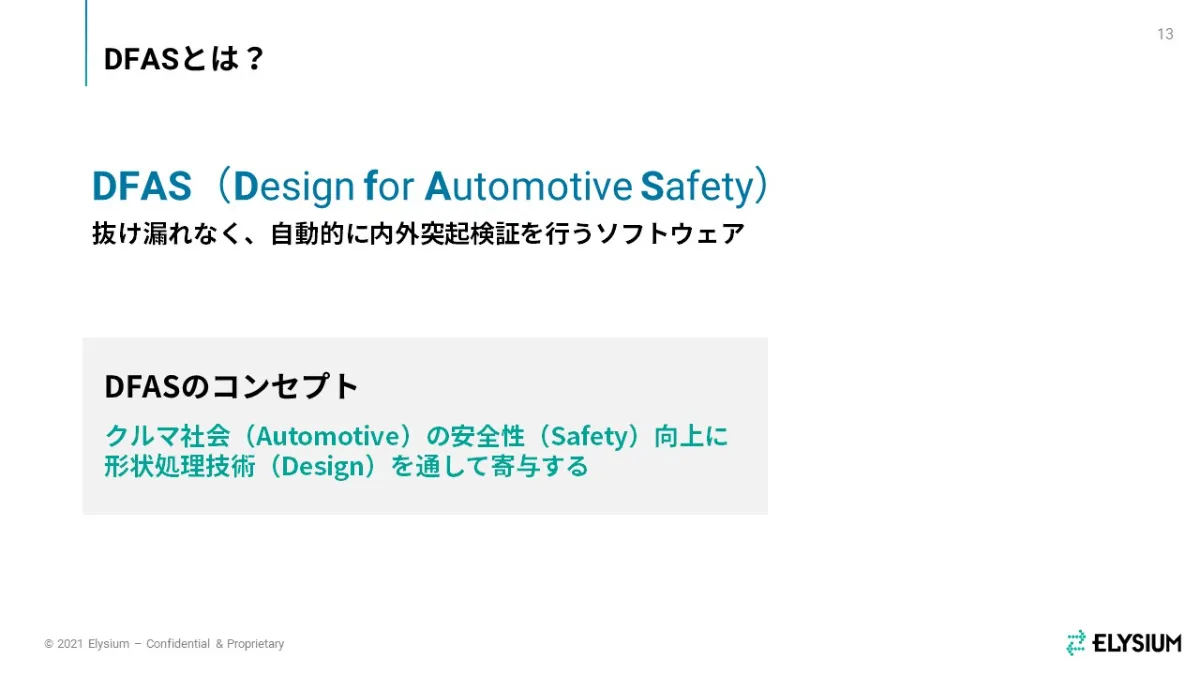
これらの課題を解決するためエリジオンが開発したソフトウェアがDFAS(Design for Automotive Safety)です。
DFASのコンセプトは「クルマ社会の安全性向上に形状処理技術を通して寄与する」ことです。DFASは自動車の安全性に着目した製品ですが、特定のかたちをCADモデルから認識して必要な箇所を測定する技術は、今後さまざまな産業に応用できると考えています。
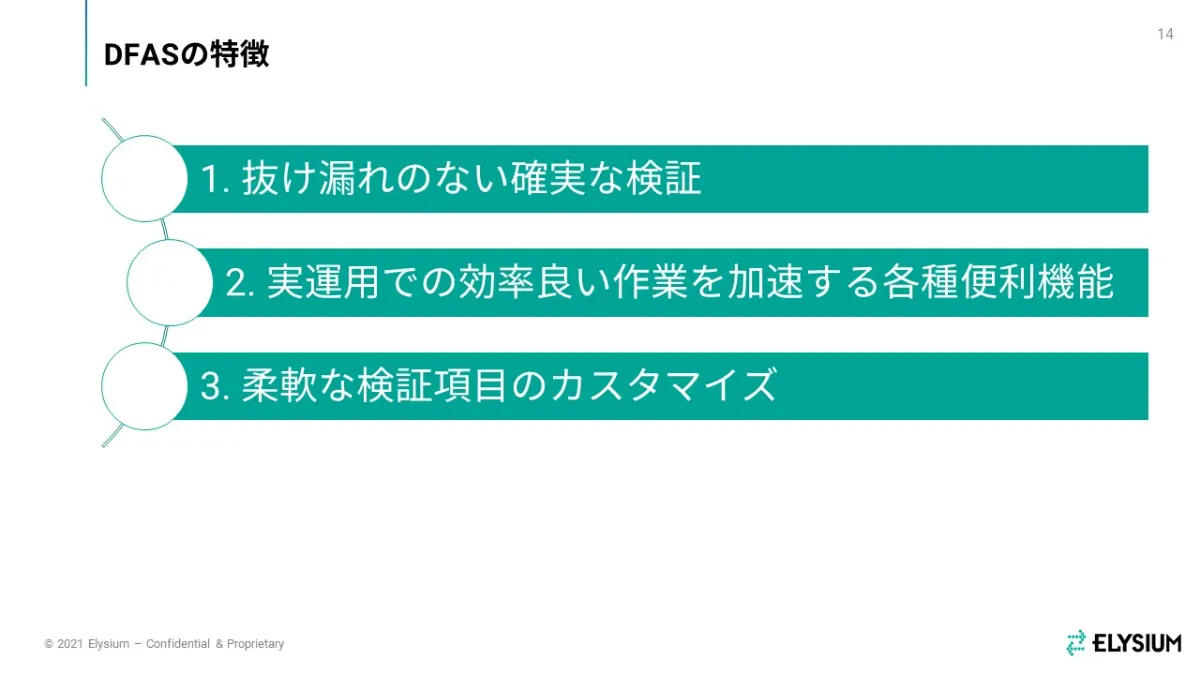
DFASには三つの特長があります。
一つ目は抜け漏れのない確実な検証を行える点です。
二つ目は、実用性の高い便利な機能を多く備えている点です。例えば安全性に問題のある箇所を検出するだけではなく、問題のない箇所のエビデンスを示すことができます。また、何か要因が加われば問題ありと判定され得る、判定が難しい箇所をレポートに含める機能があります。
三つ目は、検証項目を柔軟にカスタマイズできる点です。エリジオンが長年培ってきた形状処理技術を活用して、特定の項目だけを検証するのではなく、内規や法規の変更に柔軟に対応できるつくりになっています。
高精度でスピーディーなヘッドフォーム・二ーフォーム検証
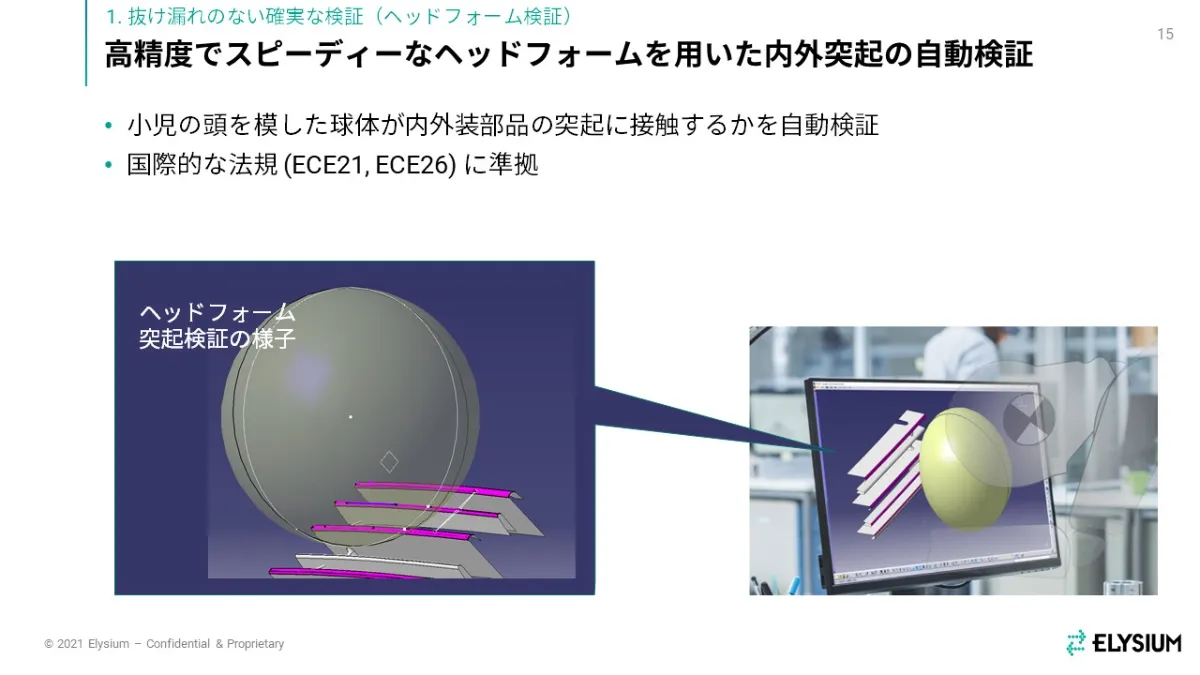
一つ目の特長として、抜け漏れのない検証ができるとお伝えしましたが、DFASは法規の中の2種類の検証に対応しています。
ヘッドフォームを用いた検証は、先に説明した通り試作車と球状の治具を使って行われます。治具の表面に粉を付着させ、試作車の表面に当てていき、粉の付いた部分の曲率半径をRゲージで測ります。
従来の試作車でのそうした測定方法を想定して、DFASではCADデータから問題のある箇所をあらかじめ自動的に抽出します。CADデータの種類は問いません。利用しているCADソフトウェアやCADのデータ形式が何であっても検証することができます。
DFASは国際的な法規であるECE21・ECE26に対応しており、内装と外装の両方をチェックします。
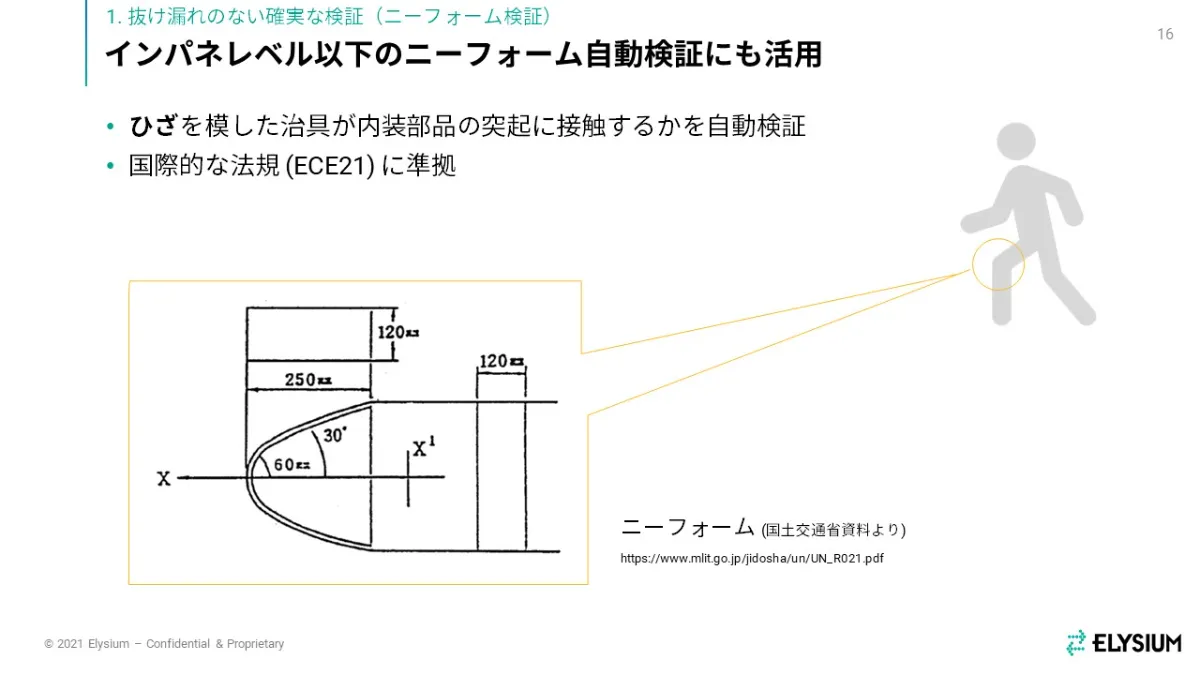
次に、二ーフォームの検証です。こちらは頭ではなく膝のかたちを模した治具を用いて検証されています。対象は内装部品の中でもインパネより下の部分で、膝に当たる部分に鋭い突起がないか確認されています。こちらもヘッドフォームと同様にDFASが該当箇所の鋭さなどを自動的に計算しながら、危険性のある箇所を抜け漏れなく抽出します。
見やすい検証結果レポート
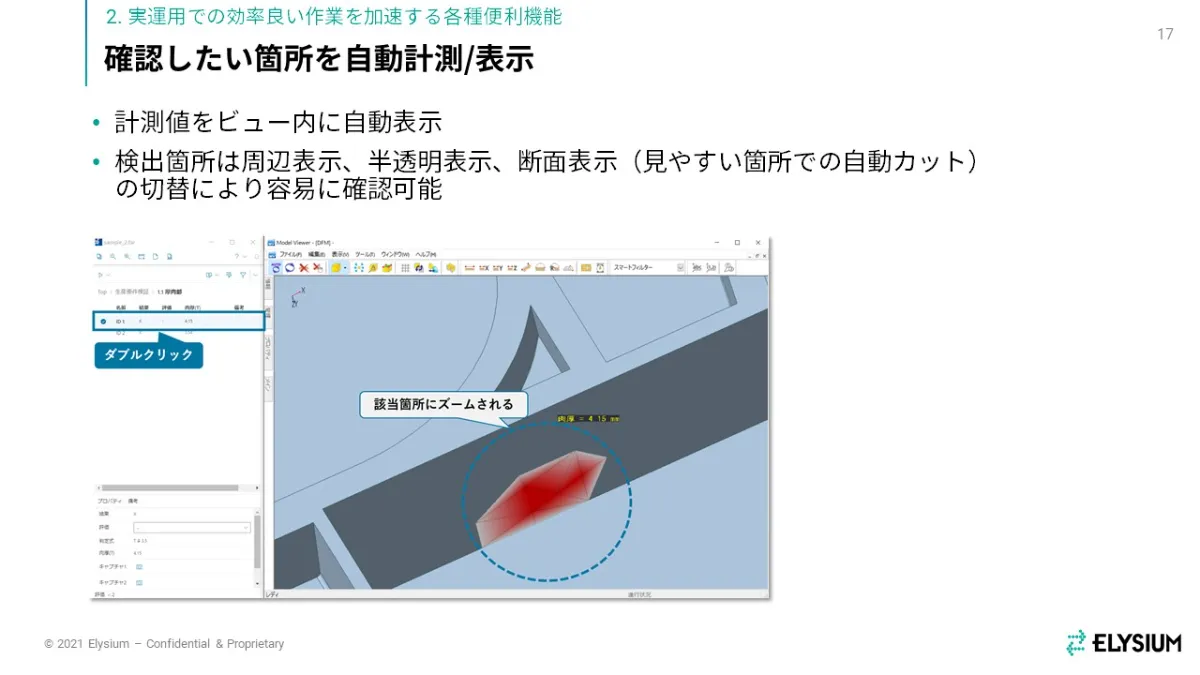
こちらが実際に検証結果を表示させた例です。エリジオン・アカデミーの別の回で紹介したDFM Studioと同様に、見やすいレポートをDFASから出力します。
左側で検出された箇所を一覧でき、これをもとに設計者自身が抜け漏れなく問題のある箇所を確認できます。リストのそれぞれの項目をクリックすれば、右側でその箇所がズームアップされます。このとき、計測された曲率半径や距離などの数値情報も表示されます。
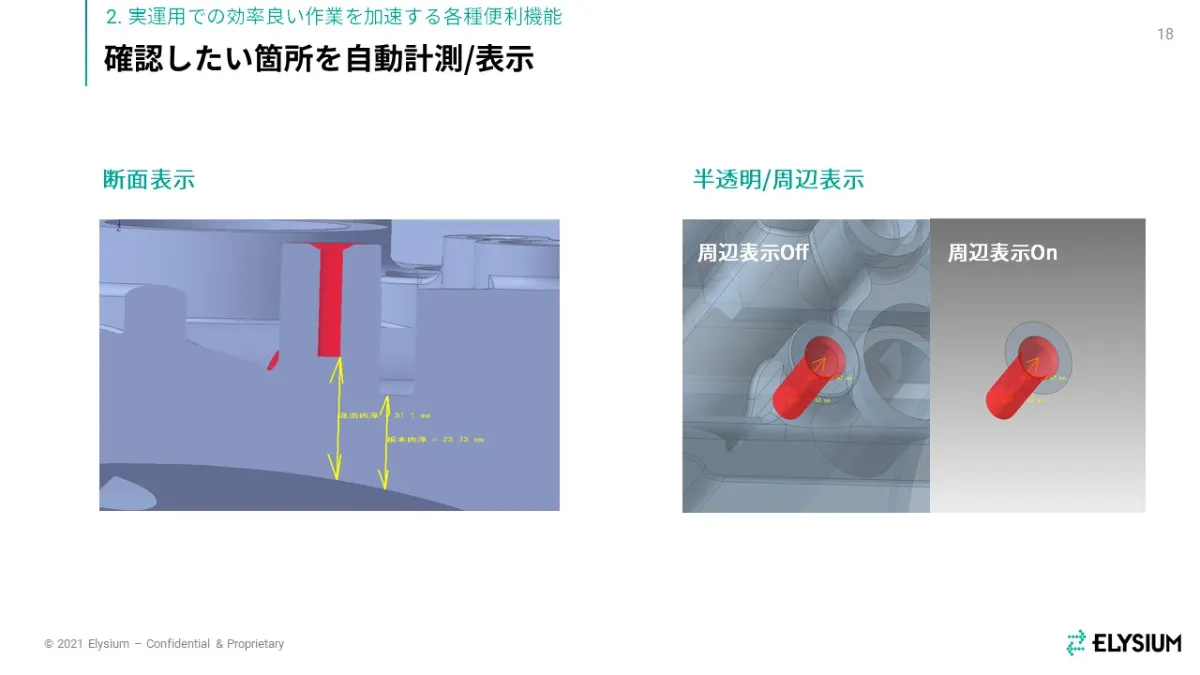
3Dのビューでは、単にズームして該当箇所を見るだけではなく、断面を表示させたり周辺のかたちと合わせて表示させたり、ヘッドフォームや二ーフォームがどのように接触したか確認したりすることができます。
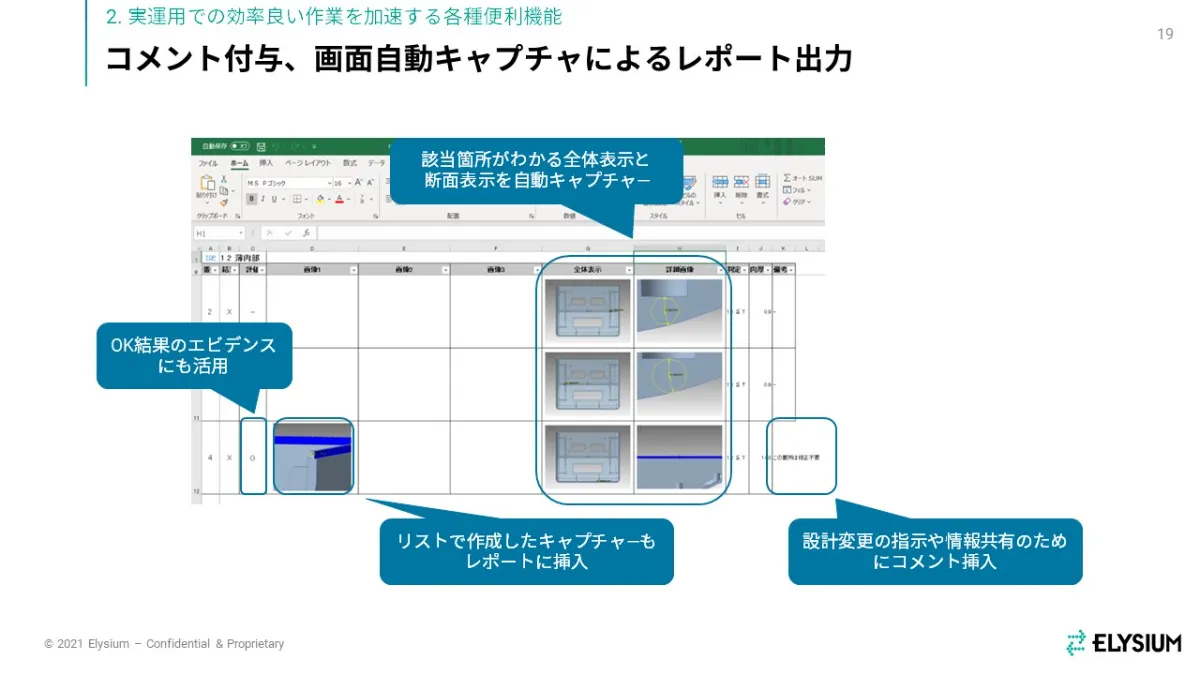
こちらはエクセルファイルで書き出された検証結果のレポートです。エクセルファイルはほとんどの方がPCで開くことができるため、部署を越えて情報を共有するのに便利なファイルです。レポートの中には、検証箇所の問題の有無だけではなく、例えば該当箇所をズームして撮った画像と引きで撮った画像が自動で貼り付けられます。また、なぜ問題がないと言えるのか、なぜ問題があると判断したのかコメントを挿入して後工程の担当者に伝えることも可能です。
カスタマイズによる実用性の向上
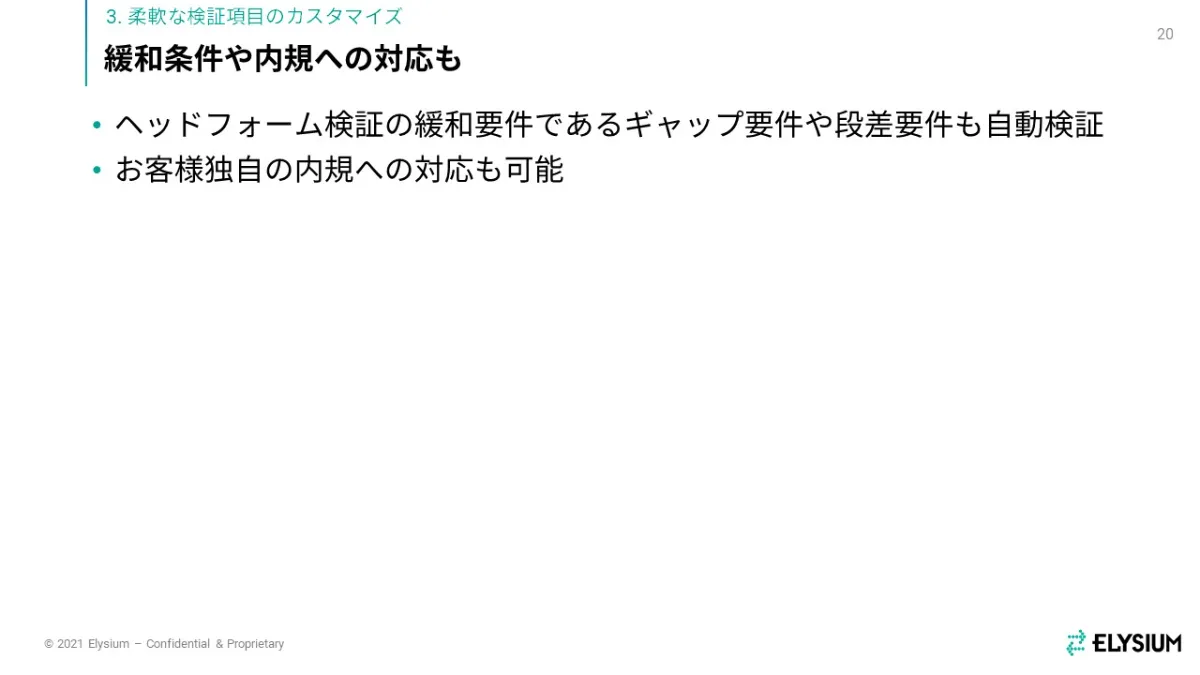
柔軟に検証項目をカスタマイズできる点もDFASの特長です。例えば、法規の中に「緩和要件」があります。ヘッドフォームの検証でいえば、球体が接触した2点の距離が一定の値より小さければ、曲率半径の値を緩くしても問題ないことが定められています。DFASはそういった複雑な条件にも対応しており、自動的に検証を行います。また、企業によっては法規で定められた値や項目以上に厳しいルールを設けています。それらをDFASで検証できるよう設定することも可能です。
誰にも扱いやすく、見やすいレポート
実際にどのように検証結果を確認できるか紹介します。
こちらはDFM Studioで出力したレポートですが、DFASも同様のレポートを出力します。
先にご紹介した通り、左側に検証で抽出された箇所のリストを表示します。右側には検証したCADモデルを表示します。
検証で問題が見つかった箇所については、左側の項目を選択すると右側のビュー画面でその箇所がハイライト表示されますので、モデルのどこに問題があるか一目で把握できます。また、どのような根拠で問題があると判定されたか知ることができ、断面表示を用いてその箇所を詳しく確認することもできます。
さらに、単にその箇所を見るだけでなくエクセルファイルでレポートを出力することができます。フィルター機能があるため、検証結果の値で並び替えしながら、重要度の高い問題から対処していくことができます。
確認をする過程で、例えば一次判定としては問題があるとされた箇所に「これは直さなくてよい」などの訂正コメントを入れることもできます。
DFASの具体的な操作画面もお見せします。動画の後半で確認できるように、赤いフェースが問題があると判定された箇所です。緑のフェースは問題のない箇所、黄色の注記は曲率半径です。黒い線は緩和要件を検証した結果で、球状の物体が接触した2点の距離を注記として表示したものです。
検証フローの自動化の効果
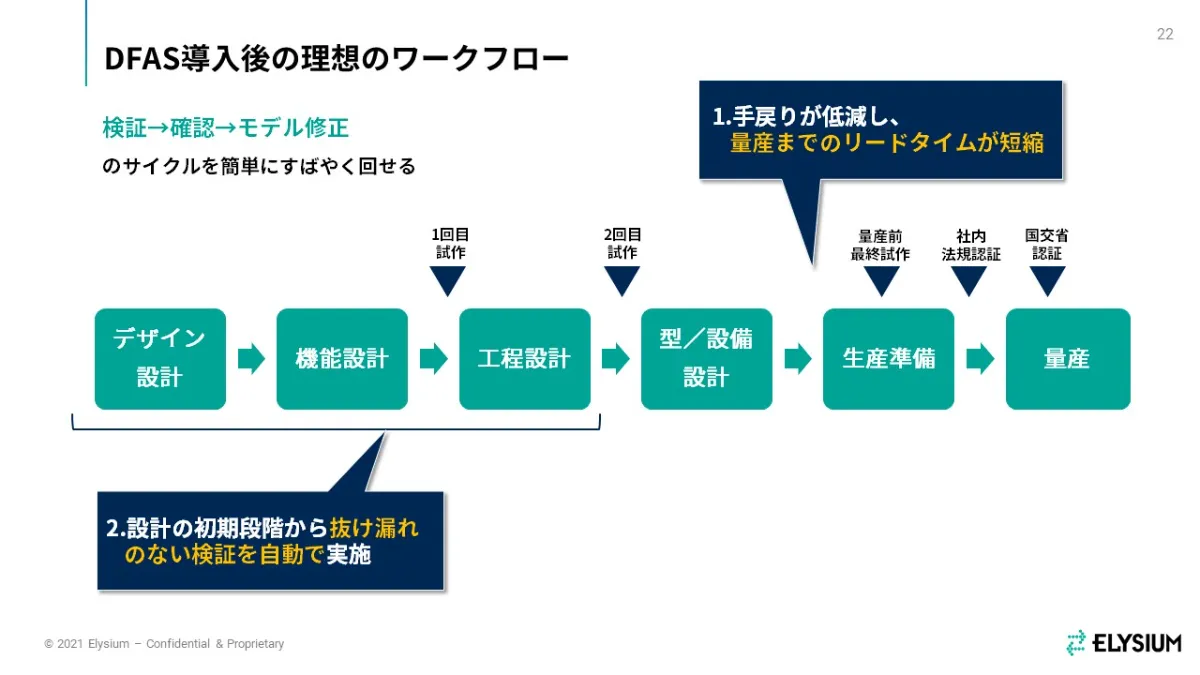
DFASを利用いただくことで、二つの問題を解決できると考えています。
一つ目は、最終段階で手戻りが発生する問題の解決です。DFASで早い段階での問題のつぶしこみをすることで、量産までのリードタイムの短縮と大きな損失の抑制を図ることができます。二つ目は、設計段階での検証方法が確立していない問題の解決です。DFASを利用することで、設計者は設計データの検証・確認・修正のサイクルを高速に何度も回せるようになり、誰でも高い品質の検証ができるようになります。
トヨタグループへの専用ツールの導入実績
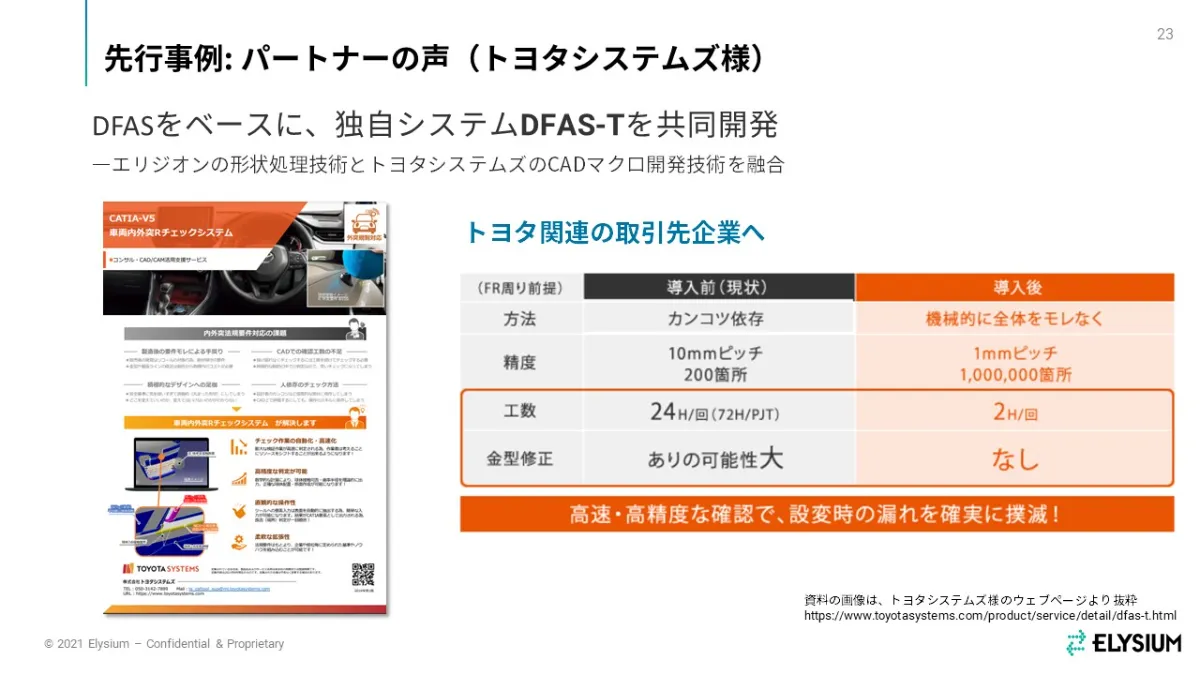
自動車以外の業界、安全性検証以外の分野への応用も
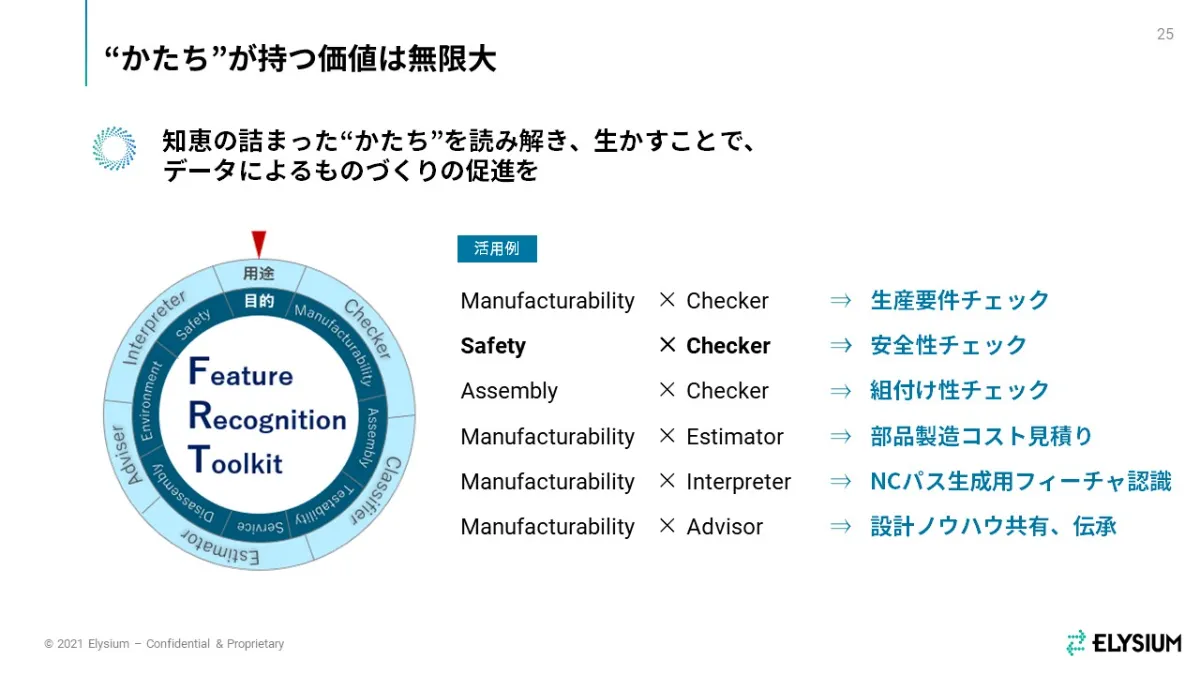
DFASは自動車の安全性に特化した商品ですが、同様のコンセプトで自動車以外の業界にも役に立つソリューションを今後展開できると考えています。
また安全性以外にも、設計データのかたちを見ることで、組付性や部品製造コストの計算も自動化できるはずです。
3D CADを使ったプロセスの効率化をお考えのお客様は、ぜひお気軽にエリジオンにお問い合わせください。