Pick Up
製品の組付け性検証のデモ
エリジオンが最新の3Dデータ活用方法などについてお伝えするエリジオン・アカデミーでは、「本当のものづくりのデジタル化を考える」をテーマに掲げ、これまでもさまざまな現場の課題について考察してきました。
デジタルツールが普及したのになぜか人の作業量は変わっていない、といったことは多くの企業で問題となっています。その原因の一つが「3Dデータ流通」の問題です。3Dデータがうまく受け渡しできず情報が流れないために、人がデータを見て判断したり、人の手でデータを編集したりしなければならず、結果として人の作業量が減らずにむしろ増えてしまうことがあります。
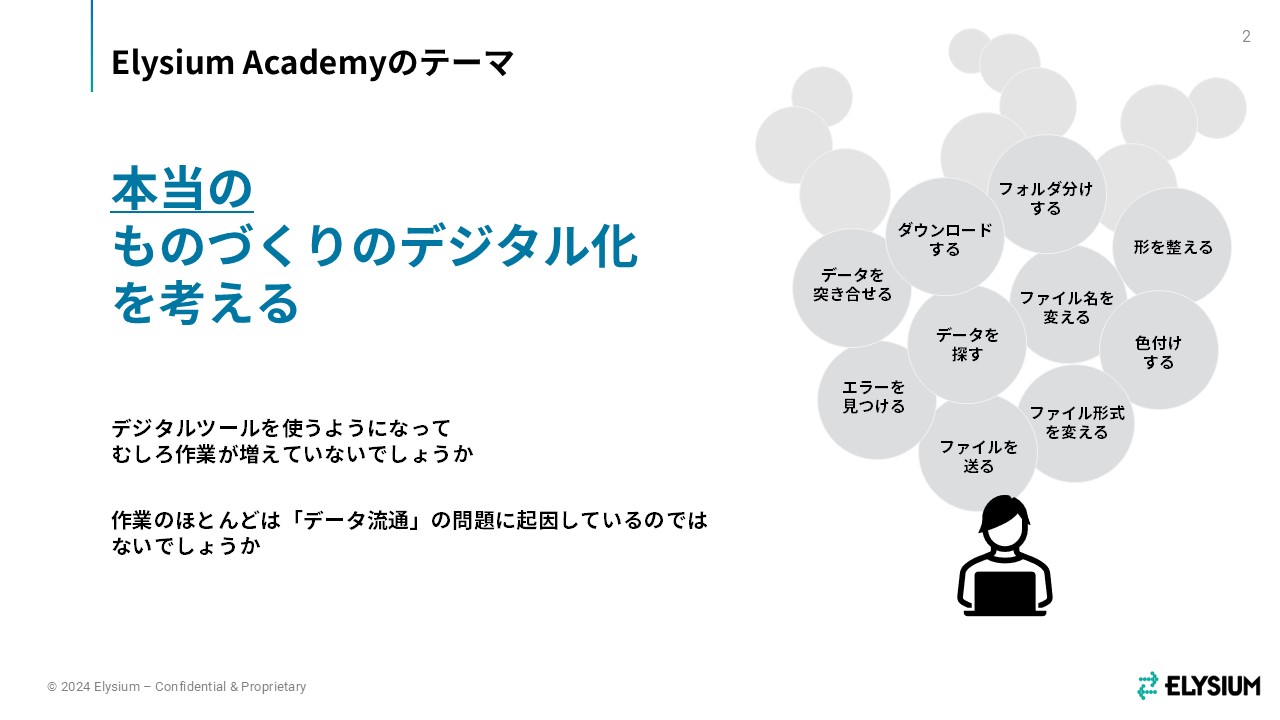
データ流通の重要性
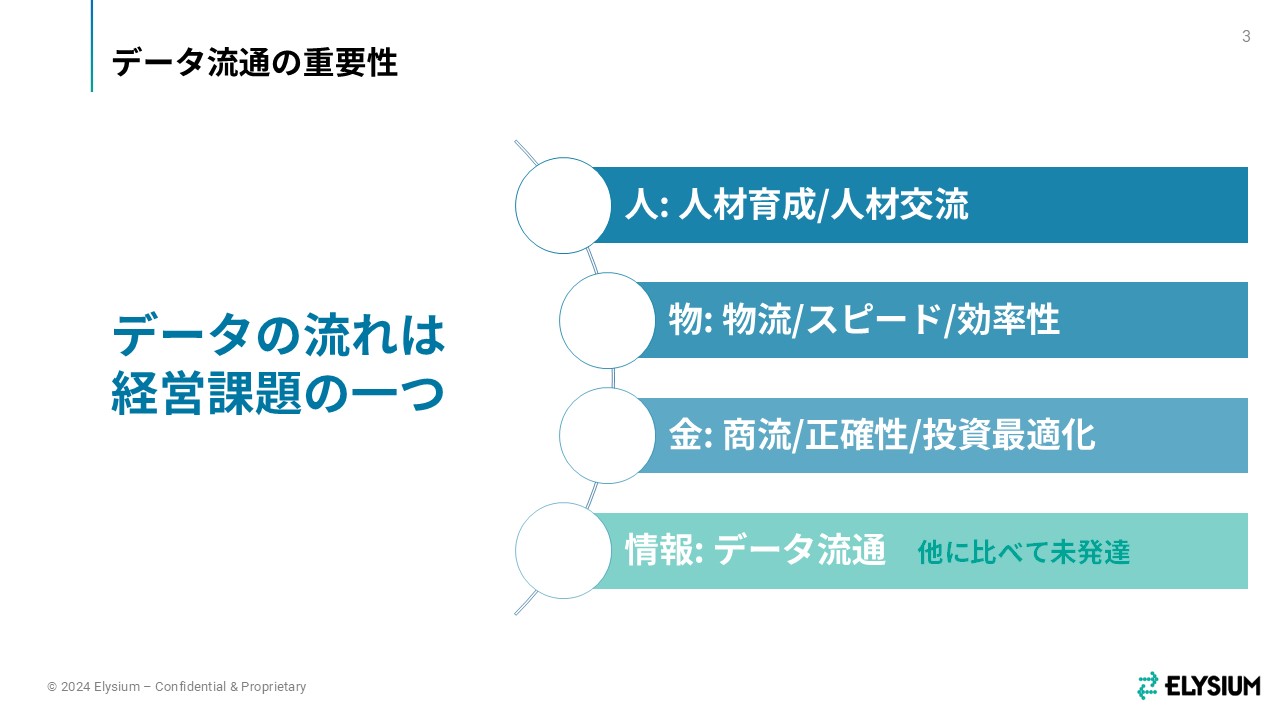
デジタルツールが普及した現代において、データの流通は企業の競争力を左右する重要な要素となっています。しかし人材育成・交流といった人の流れ、物が運ばれる物流、お金のやり取りである商流と比べると、情報・データの流通については重要性があまり認知されておらず、十分な策が施されていないのが実情です。
今回はこのデータ流通の改善を促す一つの方法として、最近注目が集まっているDFX (Design for X)の考え方やそれをDFA (Design for Assembly)に適応する方法をご紹介していきます。
DFXとは「X(さまざまな業務内容やプロセス)のための設計」という意味で、製品のライフサイクル全体を見据え、上流設計段階からさまざまな観点を考慮して設計を行う手法の総称です。
またDFAとは、端的に言えば製品の組付けや分解性をチェックすることです。これができることで、設計者は後工程にデータを渡す前に、設計したデータが製造プロセスや出荷後の保守プロセスの要件を満たしていることを自身で確認し必要であればデータを修正することができます。
組付け性の問題点とその原因
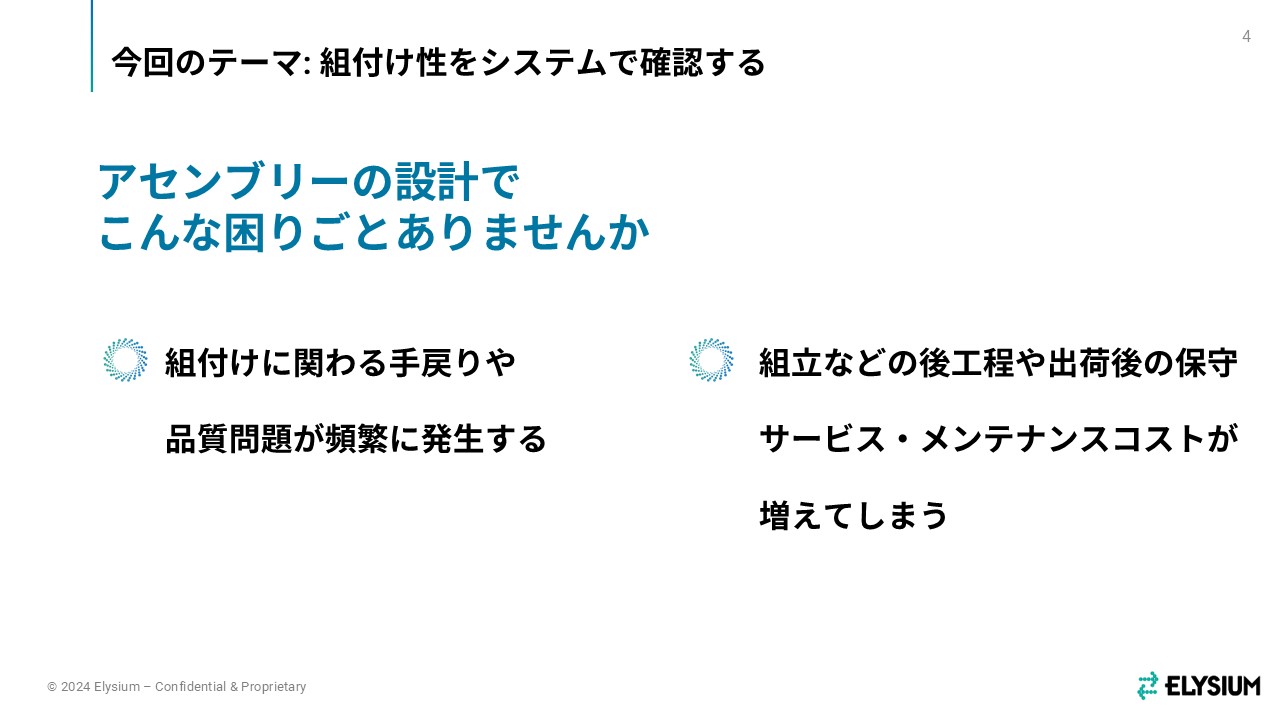
アセンブリーの問題については、お客様から課題として相談をいただくことが多くあります。その代表的なものが以下の二つです。
- 組付けに関わる手戻りや品質問題が頻繁に発生する
- 後工程や出荷後の保守サービス・メンテナンスコストが増える
手戻りや品質の問題をより具体例としては、以下のようなケースが挙げられます。
- ネジの組付け経路に障害物があったため、ロボットが使えずに手作業が必要になった
- 組み付けようとしたところ、部品製造時や組付け時の寸法等のバラツキによって実際には組み付けられないことが分かった
- 組み付けられた部品間の隙間が狭すぎることで、振動によって部品同士がぶつかり騒音が発生する
試作時にこうした不具合がわかると、また設計からやり直さなければなりません。
設計品質に問題が出る原因としては、設計部門と生産部門との連携不足や作業者のスキル不足などが考えられますが、そもそも製品の組付け性のチェックを人が行うこと自体に無理があり、そこに頼っていることが根本的な問題です。
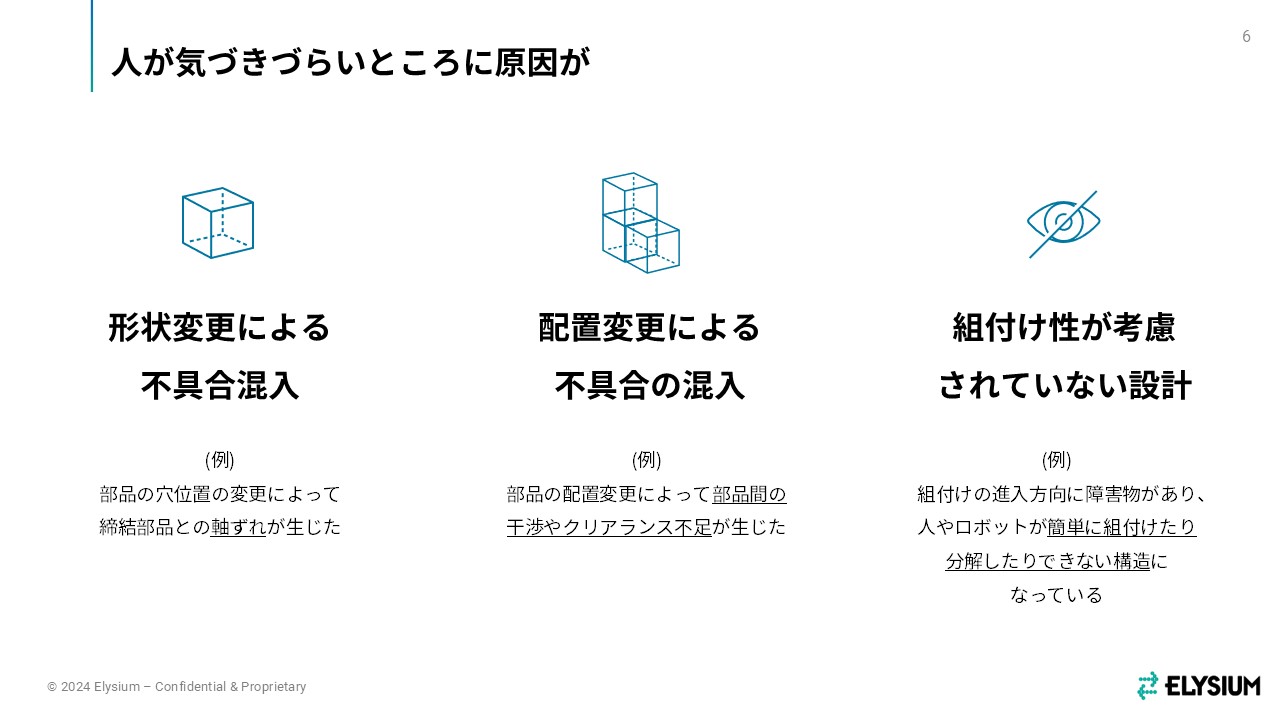
例えば、部品の穴の位置を変更したことで締結部品との軸ずれが起きるといった不具合や、部品の配置を変えたことで部品間の干渉が起きたりクリアランスが足りなくなったりするという不具合は、設計者も意図しないところで起こっているため知らず知らずのうちに必ずCADモデル内に残ります。
また、設計者が組付けプロセスの実態にそぐわない設計をしてしまう場合もあります。例えば、組付けの進入方向に障害物があるような設計をすれば、人やロボットが効率的に組付け作業をすることができません。
組付け性検証の自動化の必要性
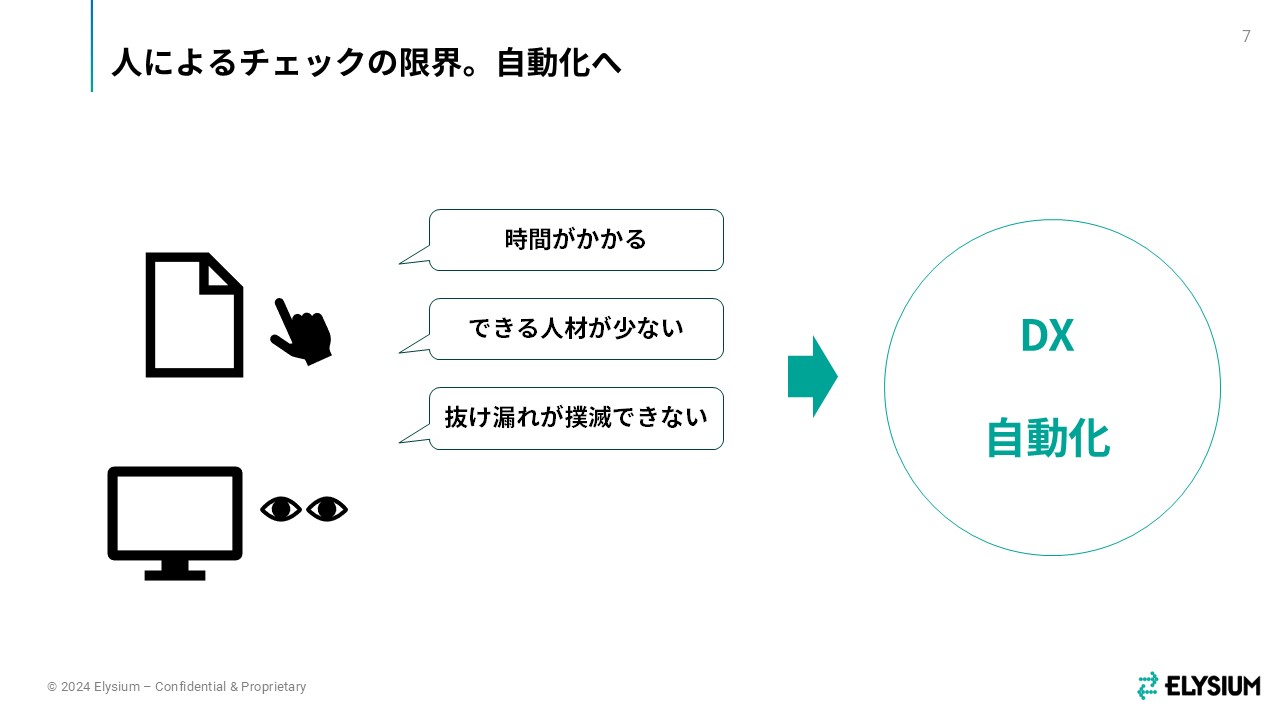
これらはいずれも人がどんなに注意しても完全には対処しきれない現象です。人によるチェックにはやはり限界があると言えます。
それでも多くの現場では、できる限り時間をかけエラーを人力でなくそうと努力されています。ただし、そのチェックを適切に行える経験や知識を持った人材も不足してきており、結果的には不具合を抜け漏れなく見つけ出し、問題をつぶしこめる企業はほとんどありません。
これを解決するには、本当の意味でのデジタル化が必要です。ITツールの導入自体を目的とすることなく人の手を介さないデータ検証の自動化を実現しなければなりません。
自動化は簡単には実現しません。知識と経験が豊富な技術者なら簡単に判断できる事象でも、実はいくつもの基準を組み合わせて善し悪しを検討しているからです。例えば、単純な干渉やクリアランスのチェックをする場合、CADモデル全体で部品間に一定のすき間があればよいということではありません。部品同士の関係性でも適切な値は異なり、ほかにも、部品にかかる力の方向によっても違ってきます。
設計業務に利用しているCADシステムをカスタマイズして、自社に合ったオリジナルの自動チェックツールを導入しているお客様もいますが、中には「人がやる必要のない手作業はそれでもなくなっていない」とおっしゃる方もいます。また、CADシステムは常に製品としてのアップデートが行われるため、カスタマイズした機能もそれに追随してメンテナンスし続ける必要があります。ときにはCADシステム自体の仕様が大幅に変更されたり、取引先との関係で別のCADシステムに乗り換えなけばならなかったりする場合もあります。そうなると、せっかくの独自システムも問答無用で一から作り直さなければなりません。
こうしたシステムの維持管理の苦労を考慮して、試してみる前からチェックの自動化をあきらめ、従来通り人の目によるチェックを続ける企業がほとんどではないでしょうか。そもそも手作業が当たり前になりすぎてわざわざ新しい方法を調べることもなく、自動チェックツールの存在を知らないままの企業も多いかもしれません。
エリジオンの強み
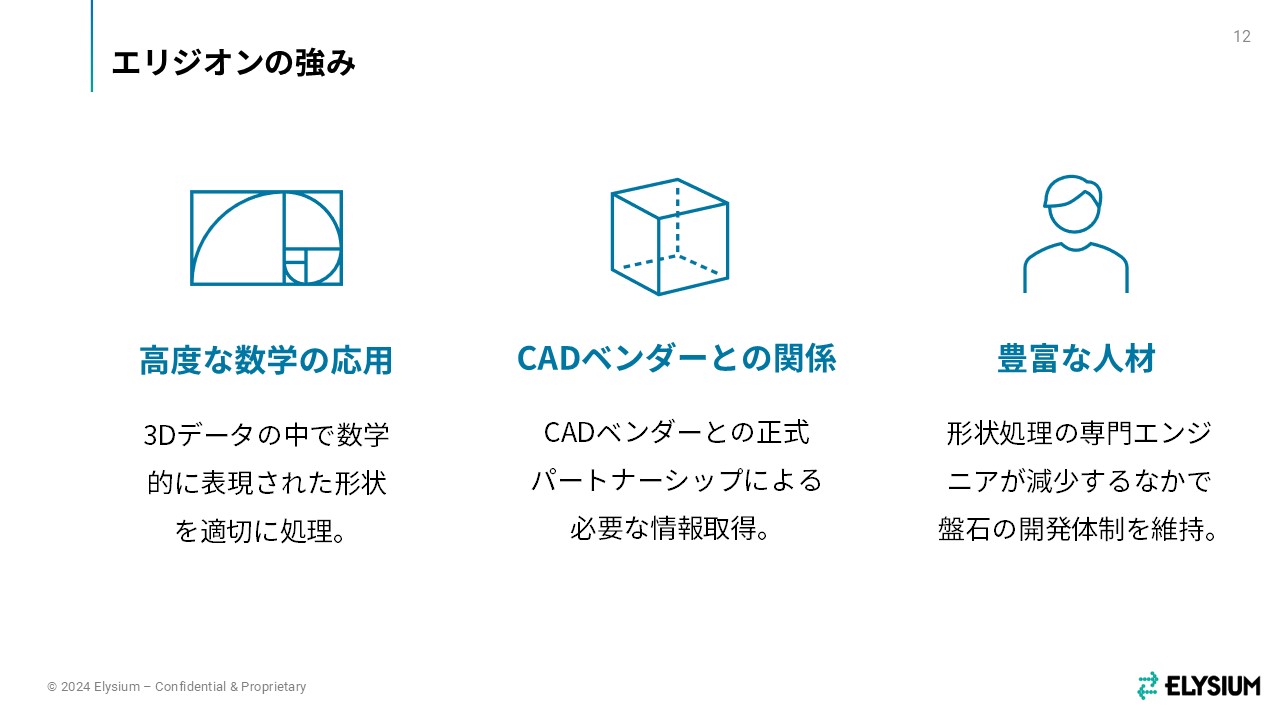
こうした企業の困りごとを解決するため、エリジオンは現在、アセンブリーを検証するソリューションを開発中です。2025年には主力製品の3DxSUITEの一機能として正式リリースすることを予定しています。
エリジオンは高度な数学を応用しながら、3Dデータの中で表現された「形状」を扱う技術を長年磨いてきました。また、CADシステムを提供する大手海外ベンダーとは正式なパートナーシップ契約を結んでいるため、公式APIを利用してCADデータの内部情報を正しく取得することができます。他社がまねできない独自技術とCADベンダーの公式APIの掛け合わせにより、高い精度のデータ処理を実現しています。
一方で、3Dソフトの業界全体を見渡せば、3Dの形状処理を専門とするエンジニアの数は減少傾向にあります。そうした中で、豊富な経験を積んだ技術者が集まり3Dデータ処理の開発を継続的に行っていること自体が今やエリジオンの特長となっています。
部品同士の関係性に意味を与えて検証する
CADシステムや他のソフト開発企業が持ち合わせていない高度な形状処理技術は、エリジオンの強みの中でも特に価値の高い、コアコンピタンスと言えるものです。
この形状処理技術があることで、見せかけのデジタル化ではなく本当の意味でのデジタル化が実現できると言っても過言ではありません。
DFAに役立つチェックツールに関して言えば、例えば部品同士の接触や干渉をなんでも検出すればよいということではありません。ネジや穴など設計者の意図した接触は、検出結果から除外する判断をシステム側で行う必要があります。もしすべての接触や干渉が検出されてしまえば、結局、人が検出結果をすべて確認しなければなりません。
過検出を起こさないためには、高度な形状処理・形状認識技術によって部品同士の関係性に意味を与え、まるで人が判断したような結果が得られる機能を実現しなければなりません。エリジオンが長年蓄積してきた形状処理技術がそこで生かされます。
さらには、会社の独自ルールを反映させたオリジナルのシステムを、エリジオンの技術をベースにするからこそ比較的容易に構築することができます。
CADの形状を使ったプロセス効率化の例
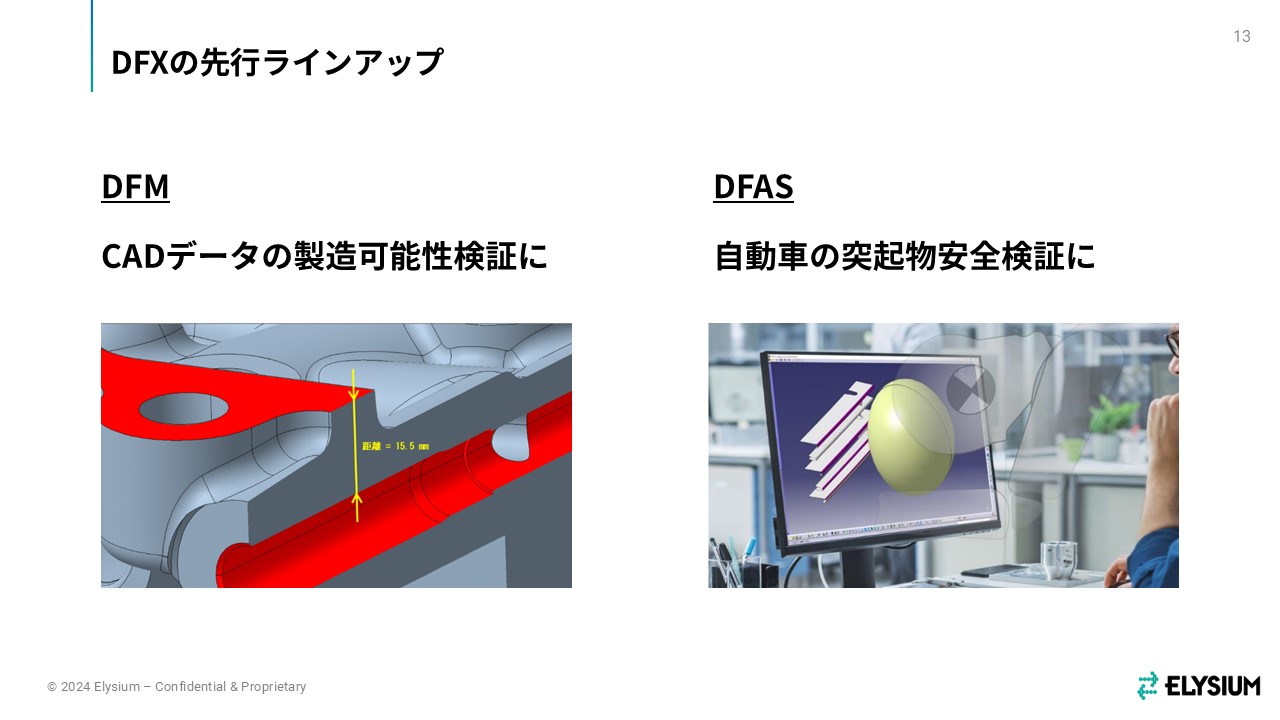
さて、今回のテーマは製品の組付け性検証ですが、設計データの形状を使って設計品質を事前に検証するツールとして、エリジオンはすでに二つの製品をリリースしています。それが、
です。
こちらのツールも、エリジオンの主力製品である3DxSUITEの一機能として利用いただけます。
特徴形状の自動認識と評価
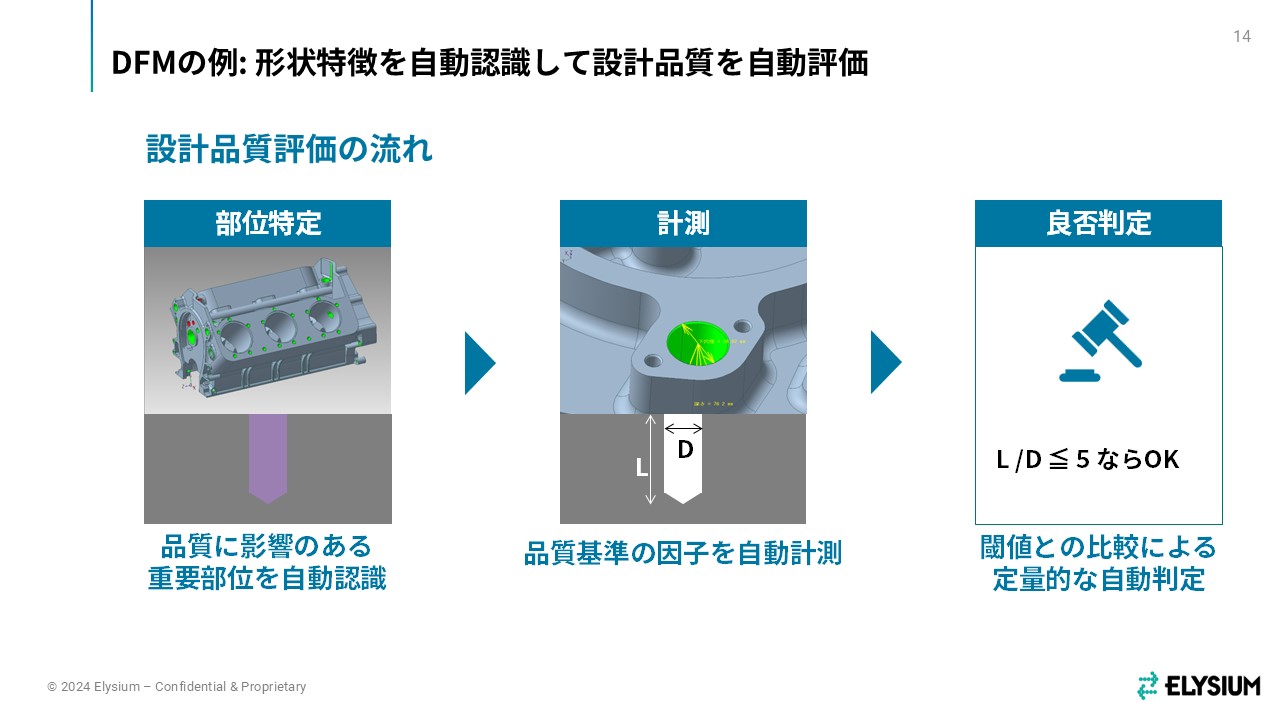
CADデータをもとにした検証プロセスをイメージしていただくために、DFMツールを用いた設計品質評価の流れを具体的に紹介します。
まずCADデータをエリジオンのソフトウェア3DxSUITEにインポートするところからスタートします。 CADデータの種類は問いません。お客様が日頃利用しているソフトウェアでモデリングしたものをそのままインポートいただけます。
次にDFMのためのデータ検証を行います。検証の前段階として、3DxSUITEでは設計品質に影響する特徴形状をモデルの中からすべて見つけ出す処理を行います。このとき、CADソフトウェアによるモデリング時のフィーチャー(設計手順)情報がなくても問題ありません。純粋にかたちの情報だけを頼りに検出を行います。これは、エリジオンが専門として蓄積してきた形状処理技術だからこそ実現できるプロセスです。
先述の通り、通常モデルの中には設計者も意図しなかった形状が形成されるため、設計者自身もすべての特徴形状をリストアップすることはできません。ましてや後工程で受け取ったエンジニアが、複雑なCADモデル全体をチェックして抜け漏れなく特定の形状を見つけることは不可能です。この部分を全自動で精度よく行うことで、プロセス全体の効率化が大きく進展します。
続いて、検出した特徴形状やその周辺のサイズや距離の計測を行います。例えば穴の直径、深さ、その比率などです。もちろん計測するだけでは終わりません。事前に設定した基準と照らし合わせその形状が正しいものであるか、修正が必要かを自動で判定します。
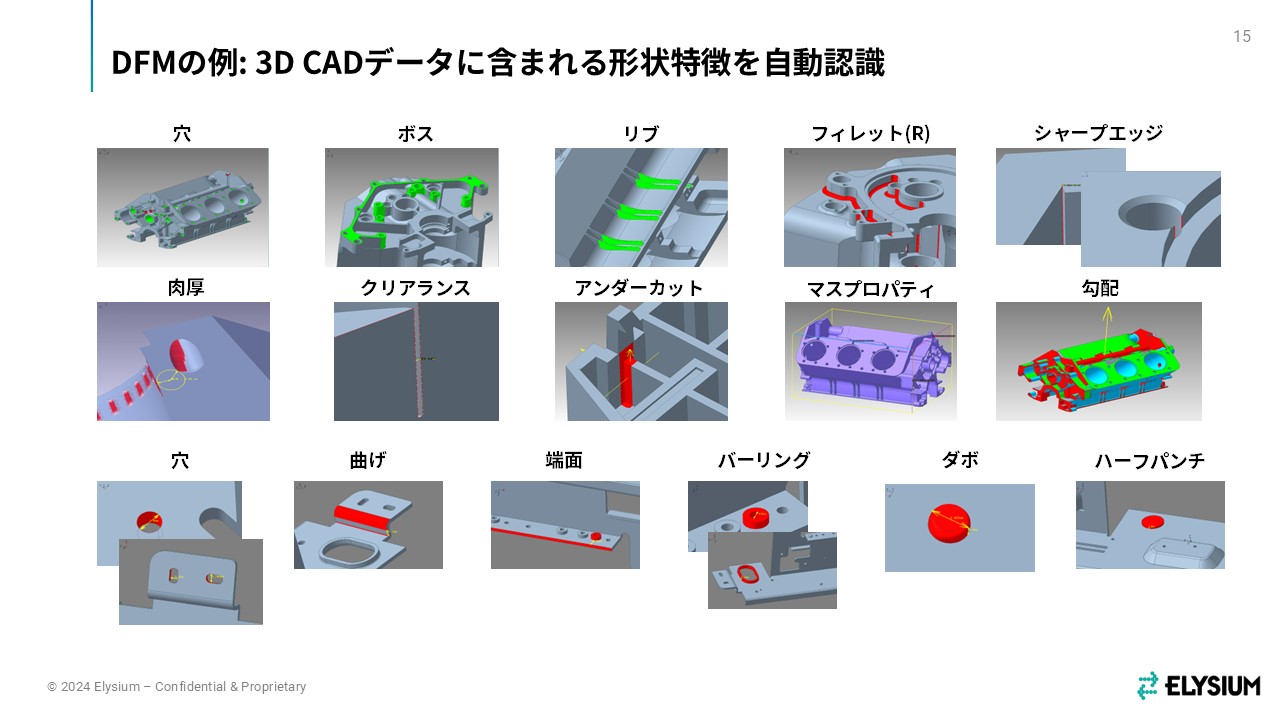
エリジオンのDFMツールでは以下のような形状特徴の自動認識と評価を行います。
樹脂部品向け
- 製品肉厚
- ボス
- リブ
- シャープエッジ
- アンダーカット
- 微小R
- 金型薄肉
- 穴
- 抜き勾配 他
板金部品向け
- 曲げ穴間距離
- 細い板幅
- 板厚
- ボス
- 丸バーリング/異形バーリング
- 穴
- ハーフパンチ
- 刻印
- 丸ダボ
- ブリッジ
- 張出し
- シンブル曲げ/フランジ曲げ/ヘミング曲げ 他
さまざまな分野に応用できる、形状認識と評価の技術
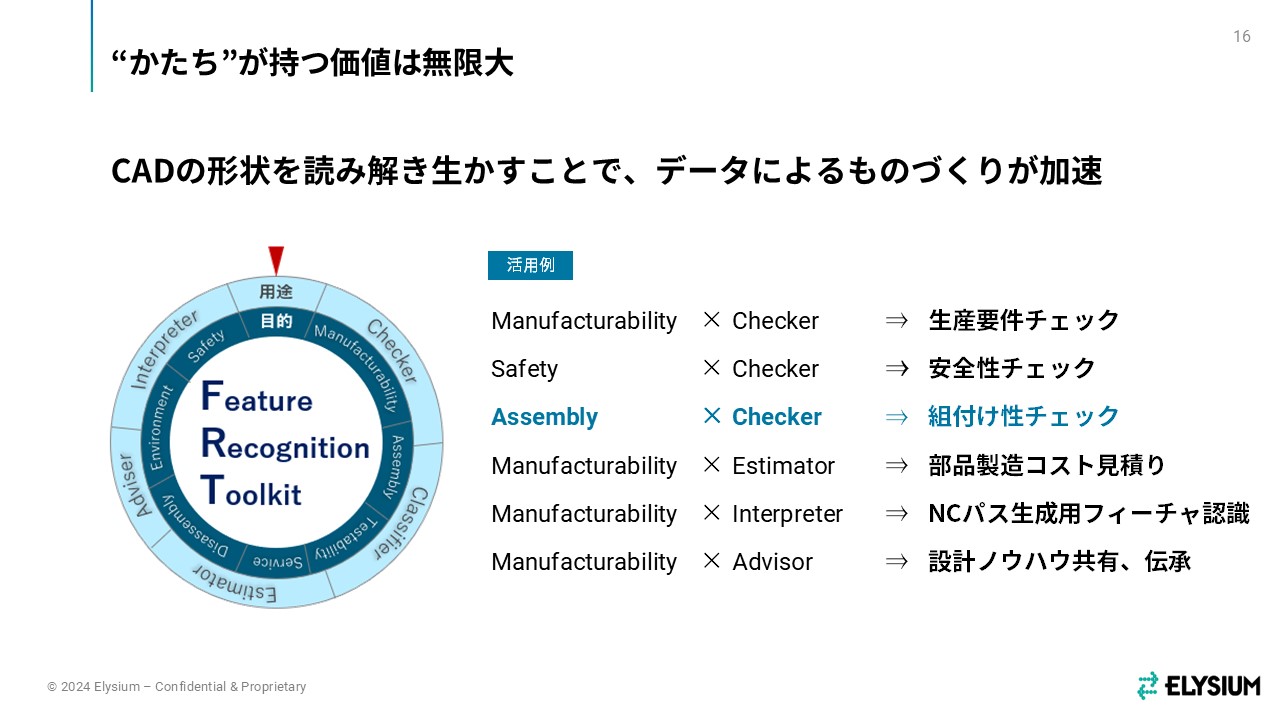
DF”M”のほかにも、DFXのXの部分にはさまざまな用途を当てることができます。
エリジオンのDFMツールに並ぶ製品、DF”AS”(自動車の安全性)もその一例です。そのほか、コストの見積もりやNCパス生成も、CADモデルの形状を見ることで適切かつ迅速に解にたどり着くことができると期待されています。
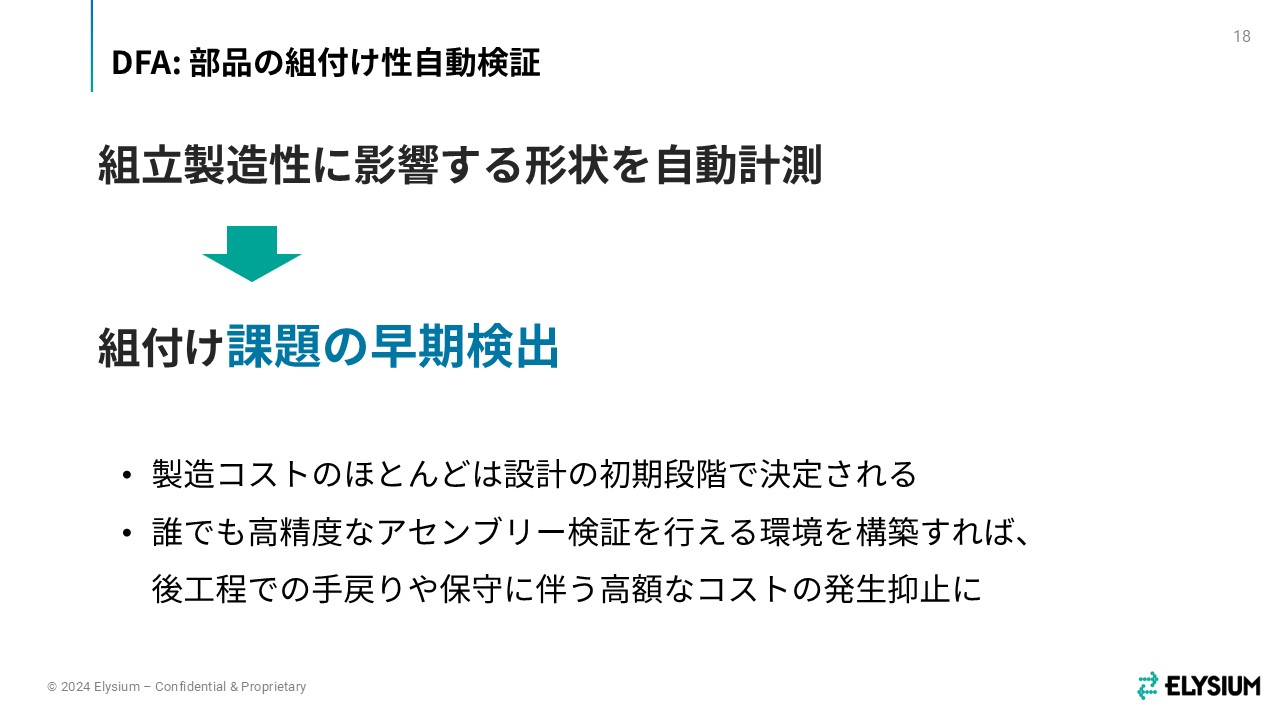
そして今回の本題、組付け性の問題解決にも、CADモデルの形状処理が有効です。組付け性の問題は、製品のジャンルに関係なくものづくりに携わる多くの設計者の方の悩みとなっています。
製造コストのほとんどは設計の初期段階で決定されると言われています。また実際の現場では形状を変えたり配置を変更したりと常に設計変更が行われます。そのため、 製品を設計したときやそれを変更するたびに、誰でも、高精度な組付け検証を行えるようになれば問題が適時解消され、後工程での手戻りや保守に伴う手間を減らすことにつながります。もし重大な不良が最後まで見過ごされ製品が市場に出回った後に見つかった場合には、補償や回収にかかるコストは膨大になります。
そうしたリスクを減らせることも、設計データチェックを自動化する大きなメリットです。
組付け性検証のプロセス
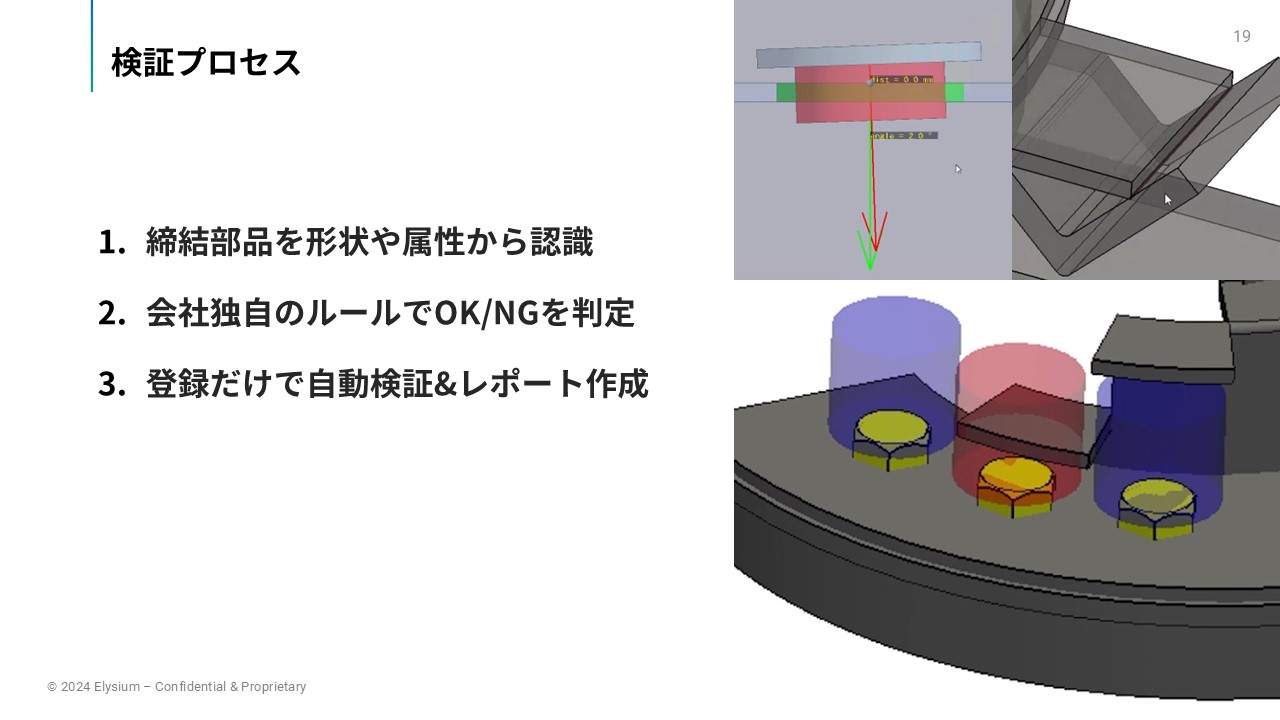
組付け性検証ツールによる検証プロセスをご紹介します。
ここでは締結部品の一種であるボルトの組付けを検証していきます。
まず、アセンブリーデータの形状や属性をもとに、CADモデルに含まれるボルトを洗い出します。そして各社で定められたルール・しきい値などから組付け性の善し悪しを自動で判定します。
さらに、検証結果を視覚的にわかりやすく表したレポートファイルを出力します。
このレポートファイルには検証結果がリストとして表示されます。このリスト化には大きな意味があります。例えば、CADシステム上のモデルのカラーマップなどを見ながら検証結果を確認するのに比べ、リストを見ながらなら担当者が検証結果を抜け漏れなくすべてを見られます。
多彩なアセンブリー検証項目
製品の組付けや分解性に関する検証項目としては以下のようなものが挙げられます。
- クリアランス
- 穴接合性
- 軸ずれ
- 標準径
- 通し穴クリアランス
- 浮き
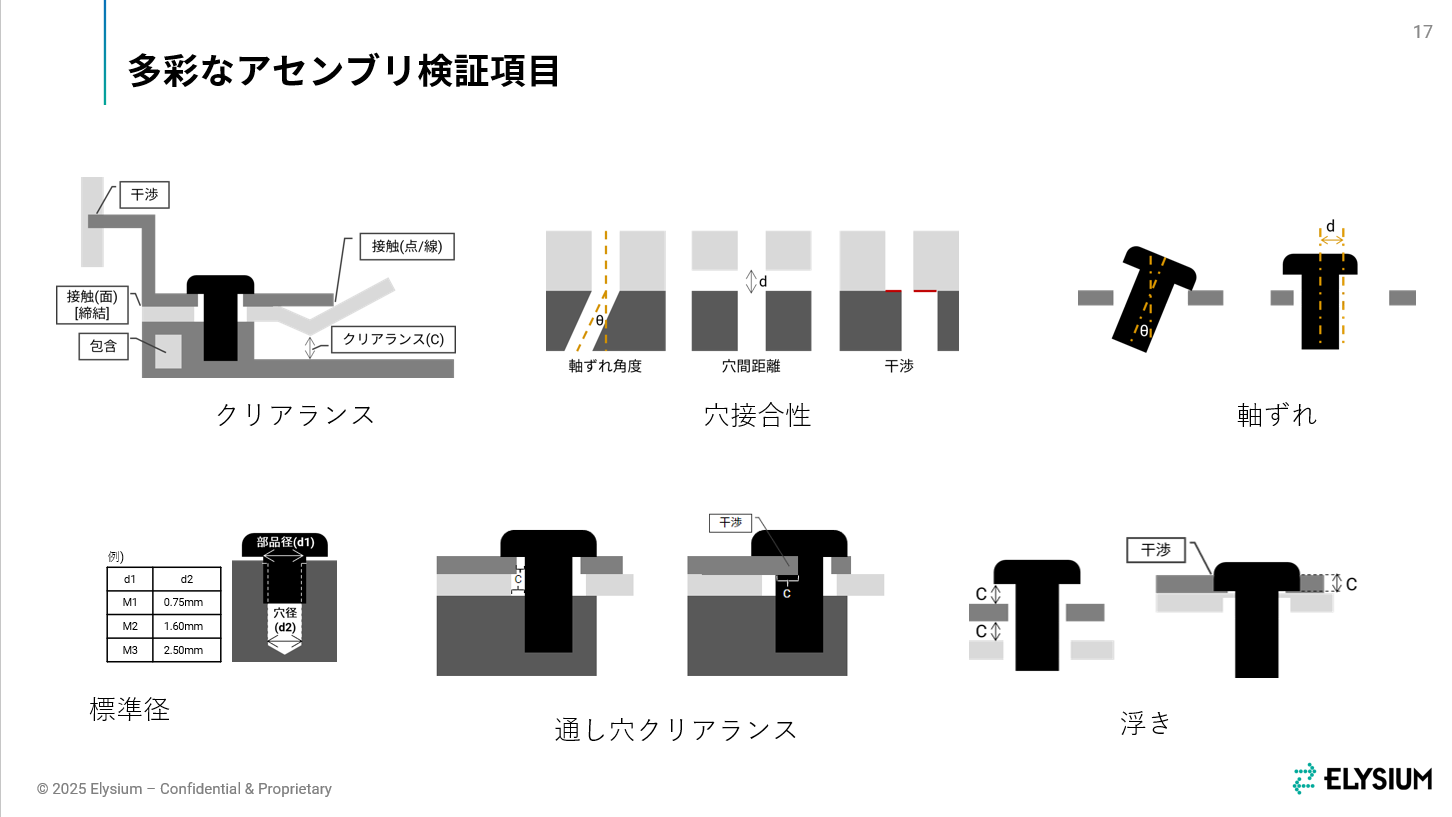
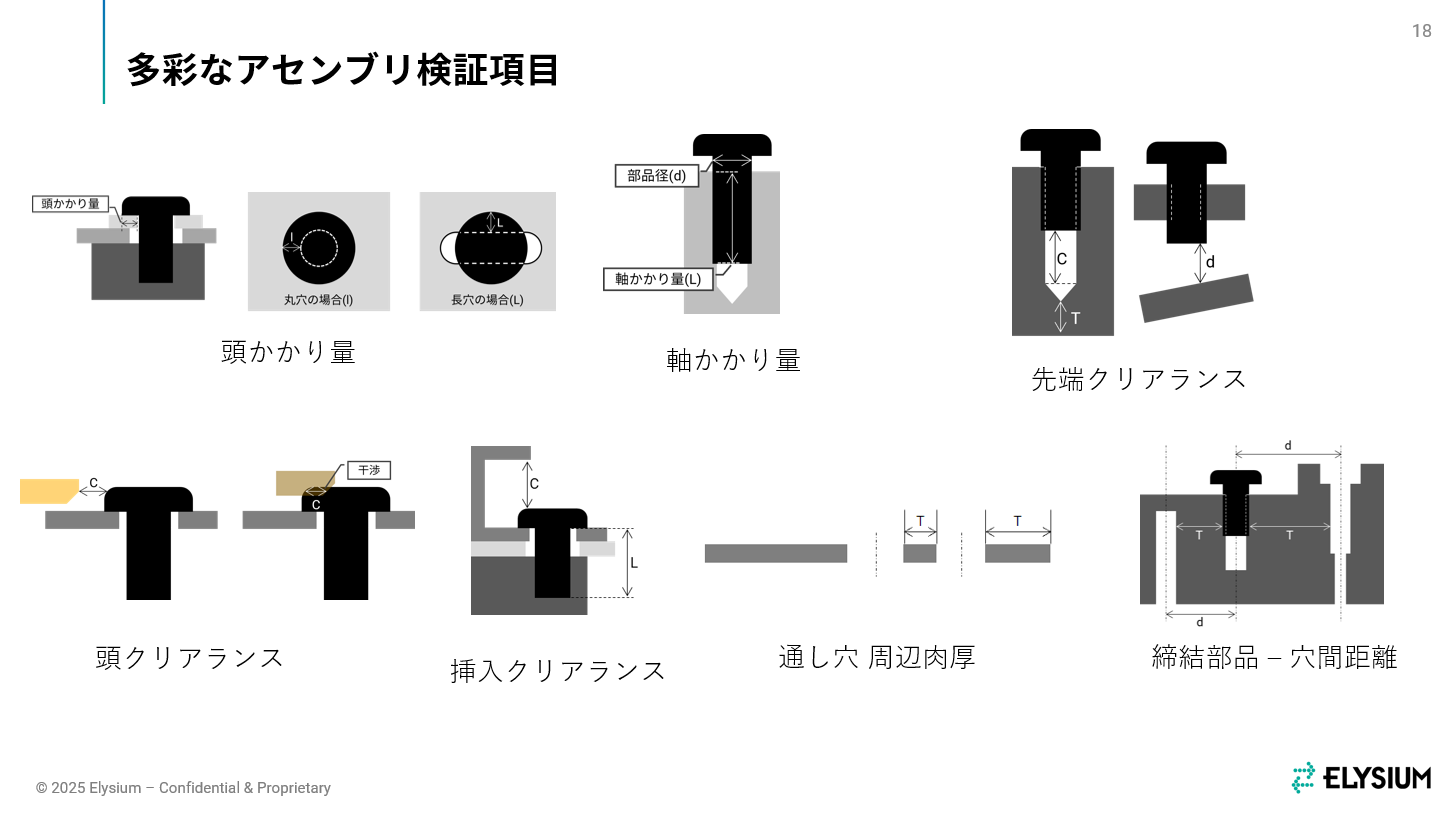
これらの要件をすべて理解しCADモデル全体をチェックするのは、どんなに優秀な設計者でも不可能です。たとえ惜しみなく時間をかけたとしても完璧なチェックは望めません。
なお、先にエリジオンの技術でエラー箇所の過検出を抑えることができるとお伝えしましたが、アセンブリーを対象としたときに特に多く検出されるのが面接触です。単に形状の重なりだけを見ればクリアランス不足と検出されてしまいます。エリジオンでは、まず締結部品を自動認識させたりすることで、その部分の面接触を干渉チェックから除外します。
こうした環境を整えることで、検証という、設計者にとっては本質的ではないとも言える付帯作業をシステムに任せることができ、設計者自身はよりよいものづくりに集中して取り組めるようになります。
DFAソリューションの実装方法は二通り
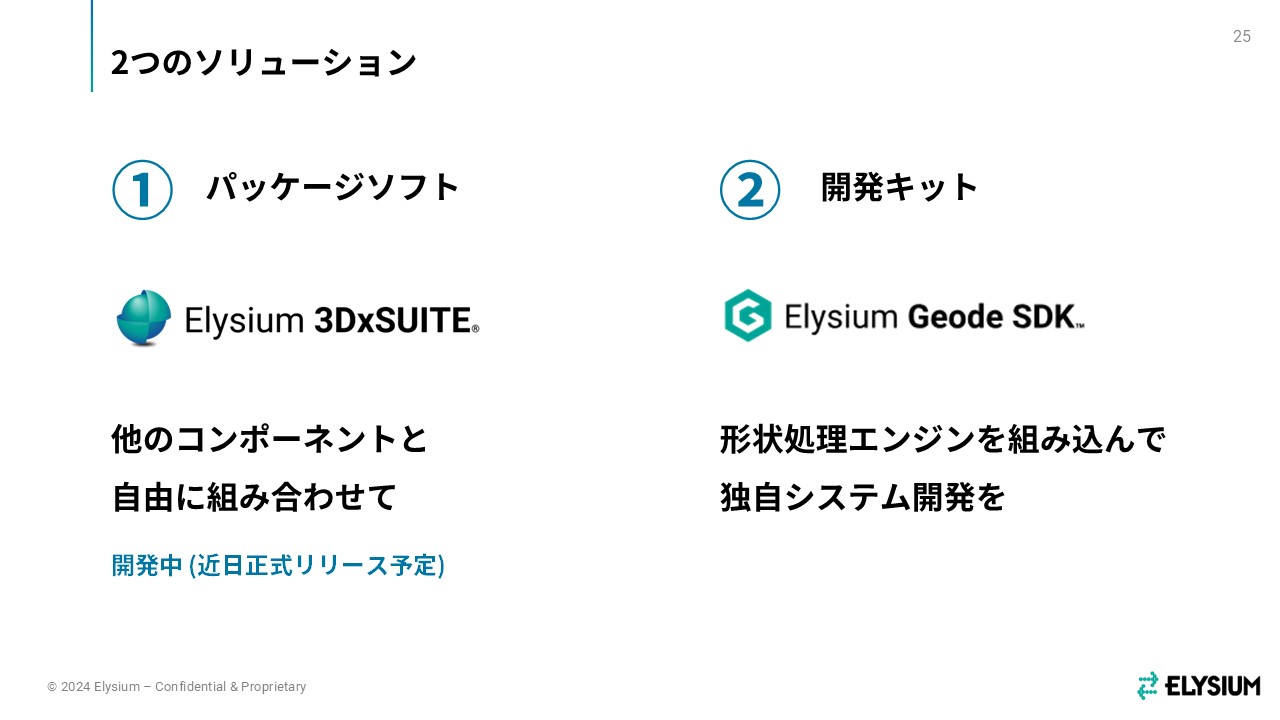
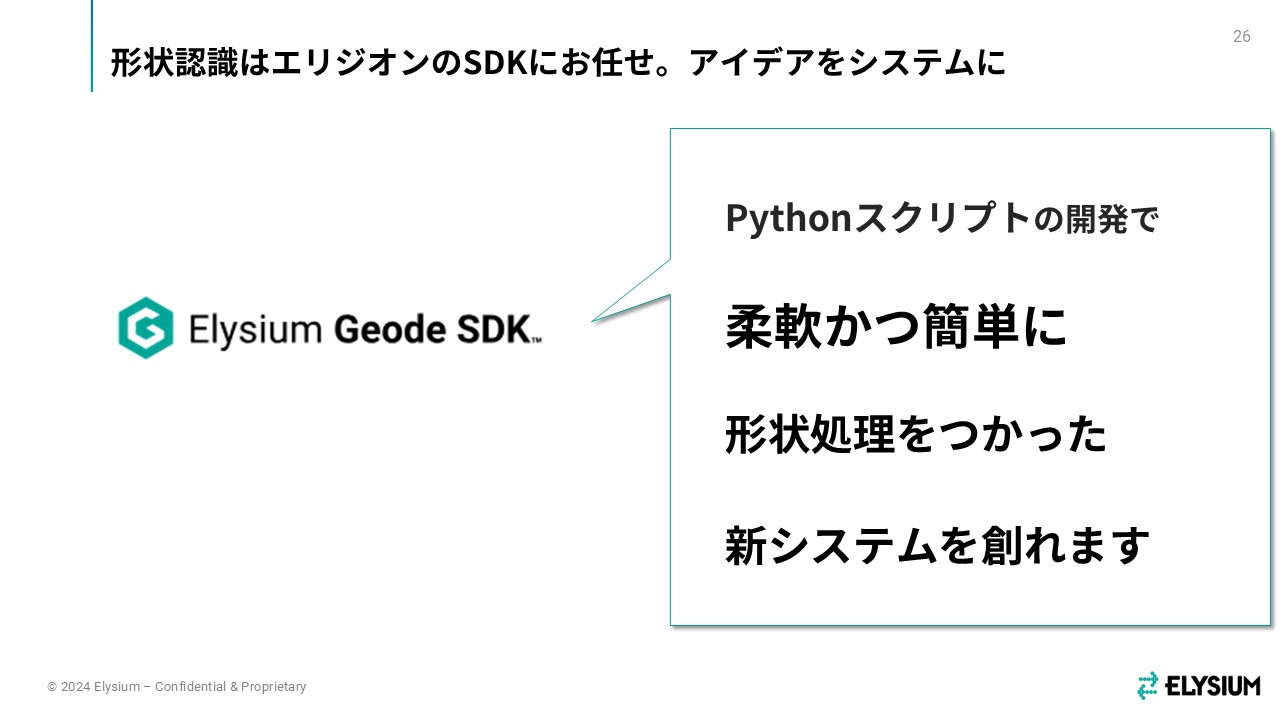
Geode SDKを使うことで、エリジオンが長年培ってきた形状処理技術をエンジンとして取り入れ、お客様自身で、独自の3Dデータ活用システムを開発いただけます。なおGeode SDKにはチュートリアルやPythonのサンプルコードも含まれています。3Dデータを扱ったことがないエンジニアの方でも安心してシステム開発を進めていただける内容となっています。
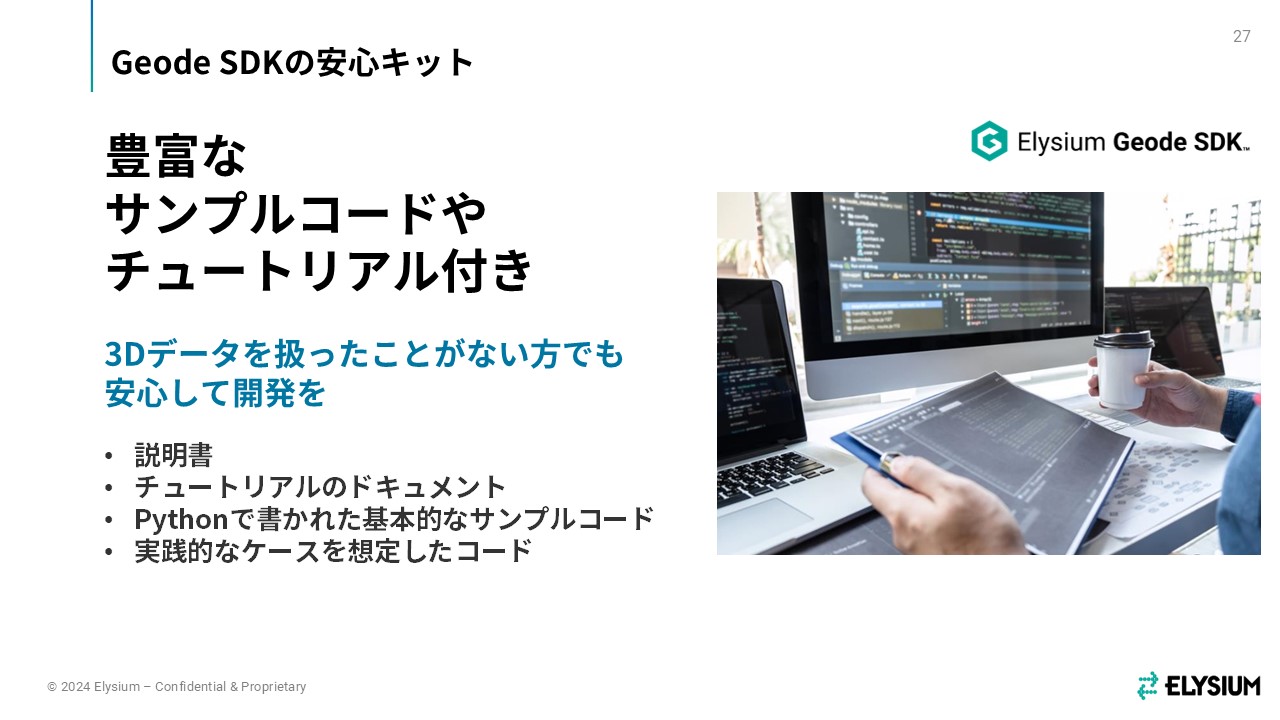
DXのテーマの一つにDFAを
昨今、「製造DX」を全社的な方針として掲げる企業が増えています。
当社にも、DXをテーマにご自身で具体的な課題や要望を整理し、やりたいことを明確にされているお客様からご相談いただくことが多くなりました。一方で、「DXと上から言われたが何をしたらいいかわからない」「まずはどんな事例や技術があるかを教えてほしい」といった、まだ施策についてイメージをお持ちでないお客様からのお問い合わせもあります。
今回ご紹介したDFA(アセンブリーデータの組付け性検証)の取り組みは、これまで人の手で行われていた作業をシステムに置き換えることでチェックの精度とスピードを向上させ、それがプロセス全体のコスト削減やリードタイム短縮につながっていく効果的な施策と言えます。
ぜひ一度、いま現場で行われている組付け性検証のプロセスを確認してください。自動化の必要性をお感じになったら、製造DXの次の重点テーマとして取り上げていただきたいと思います。